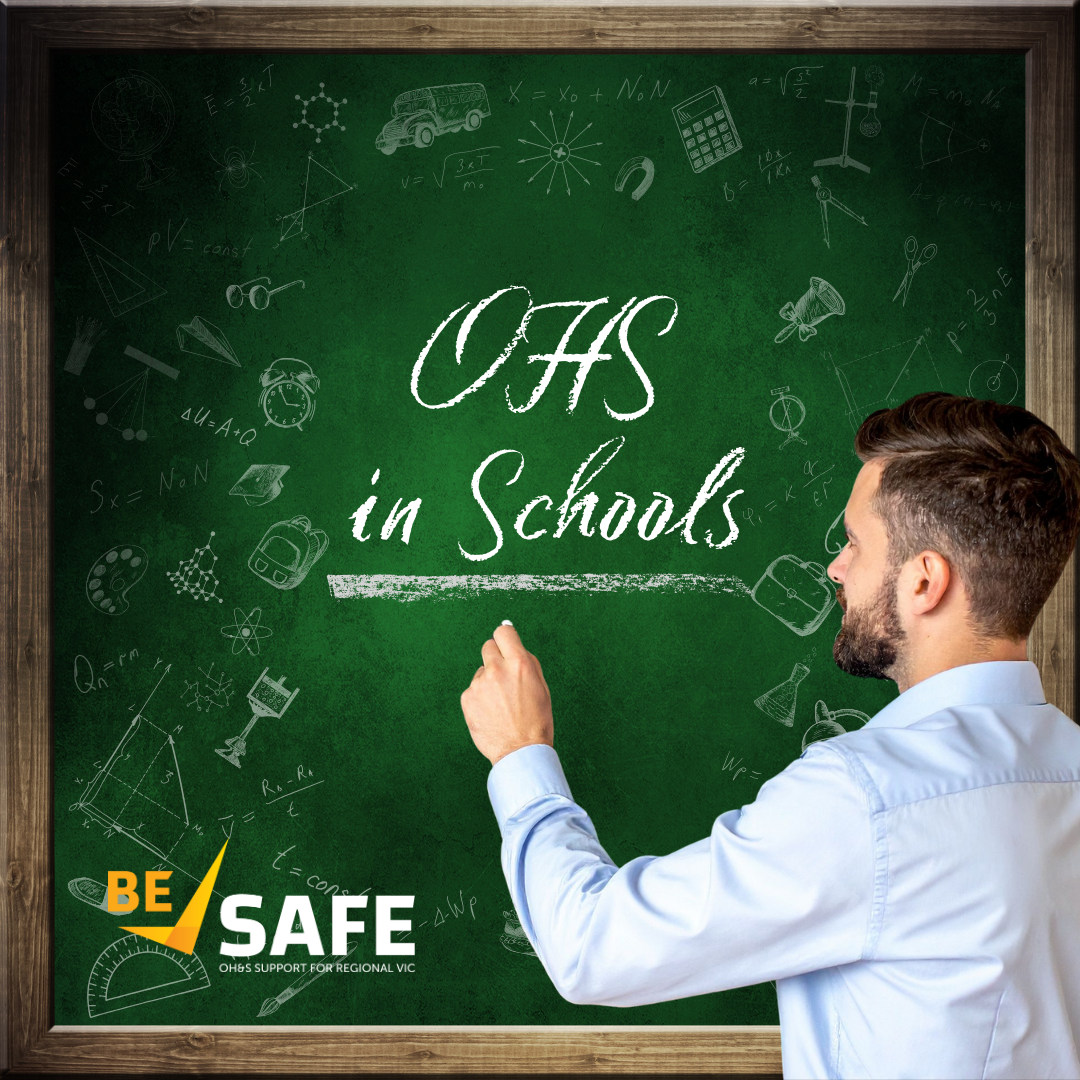
School Education is an industry with specific OHS challenges. In fact, The Department of Education has been flagged as one of the highest risk government employers and the Government sector has been announced as one of 5 key industries of focus for WorkSafe in reducing workplace harm. Government-health-safety-strategic-approach-2025-08.pdf OHS Law requires that educational institutions of all types adhere with their legal obligations – and this includes schools. Schools are not just places of learning—they are workplaces for staff and environments where students spend much of their time. Ensuring safety and well-being through Occupational Health and Safety (OHS) is not only a legal requirement, but is also essential for fostering a positive workplace culture. The employer has a duty to provide a safe workplace to its’ employees, and also to the students and members of the public. Part of meeting safety obligations means effectively consulting with their employees on matters relating to safety. The best way for safety matters to be effectively communicated is through proper consultation arrangements. This includes: · The establishment of Designated Work Groups (DWG) · Electing Health and Safety Representatives · The establishment of Health and Safety Committees Don’t forget that effective consultation is a legal requirement under The OHS Act and that employers are required to set up DWGs if requested by a worker. They are also required to assist with how HSR’s will be elected for each DWG. If an HSR then asks for an HSC to be established, the employer has 3 months to do so. (For more information, see Part 7 of the OHS Act.) Also, don’t forget that HSRs have a right to attend HSR training at a provider of their choice! HSR Training Courses | BeSafe | Regional Victoria Key OHS Risks in schools may include: · Hazardous manual handling · Work-related stress, violence, harassment and bullying · Slips, trips and falls · Plant and equipment · Hazardous substances and dangerous goods · Additional risks associated with school excursions and camps While there are specific hazards and risks in the school workplace which need to be addressed, all of the usual obligations and duties under the OHS Act apply. WorkSafe Victoria has some guidance material relating to OHS in Schools which can be found at: Occupational Health and Safety (OHS) in schools: A practical guide for school leaders | WorkSafe Victoria Additional resources can also be found here: Education Websites & information - OHS Reps As always, BeSafe Victoria are happy to help – so give us a call and we can help to point you in the right direction: HSR Training and support | BeSafe | Regional Victoria
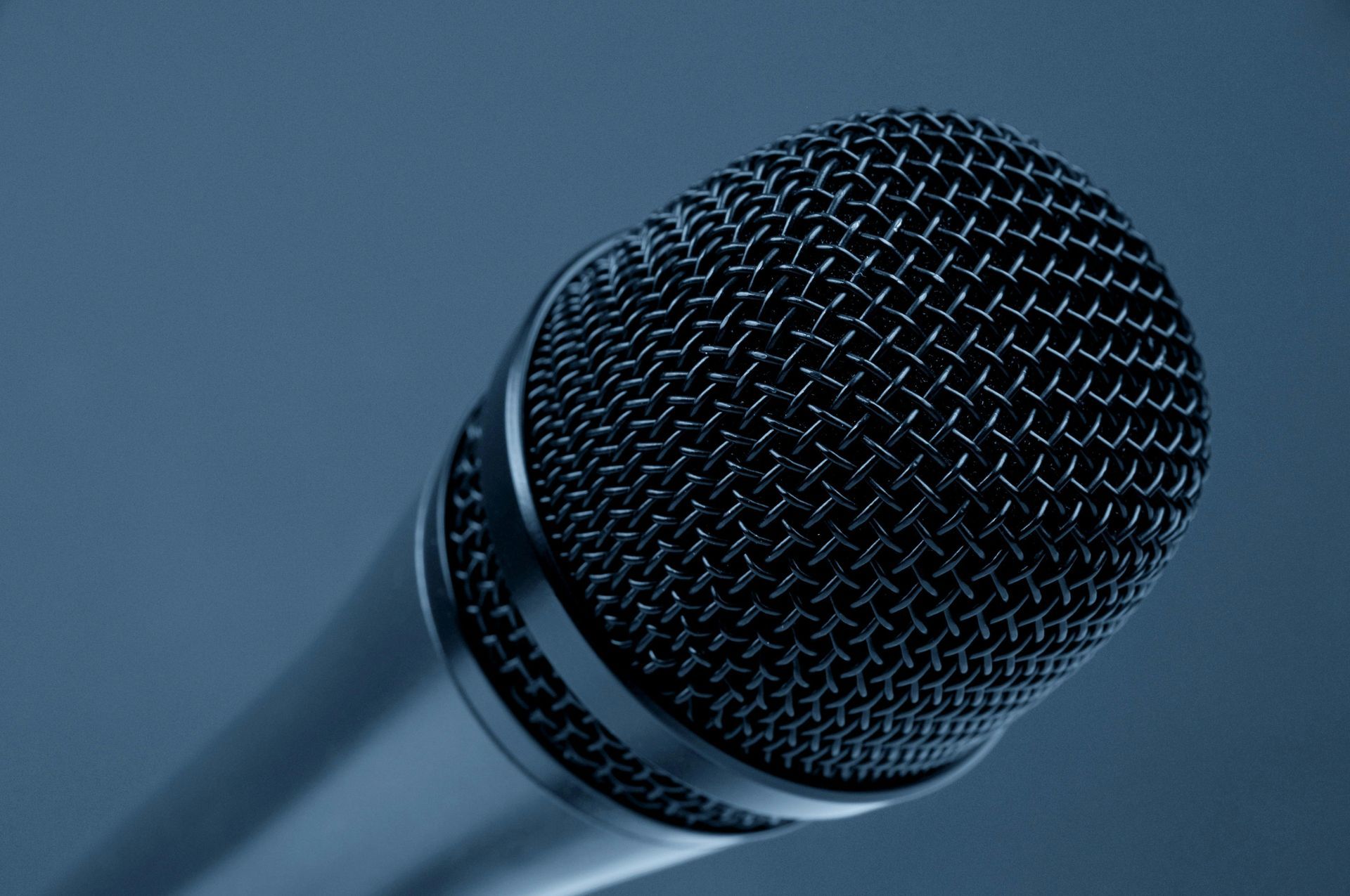
The Minister for WorkSafe recently made an announcement which included a warning to employers who put workers’ lives at risk. In the press release, the data shows that WorkSafe is issuing more fines - up by $1.1million from the previous financial year. He also stated that WorkSafe have inspected more workplaces, with nearly 7,500 more inspections conducted. Furthermore, there have been more compliance notices – with 13,943 notices issues, compared with 16,300 from the previous year. The Minister announced the launch of a new “Statement of Regulatory Intent” which plans to target the 5 most high-risk industries: Healthcare and social assistance Construction Government Agriculture Manufacturing These industries are responsible for 60% of all deaths and injuries in the workplace. The Minister stated that “Criminal prosecution, substantial fines, and potential imprisonment await employers who fail to meet their legal obligations to protect workers' lives.” The Statement of Regulatory Intent has been published on the WorkSafe website, and it includes an overarching summary document as well as several documents relating to each of the key target industries. Each industry also has some key hazards which will be targeted within that industry, while in all industries a key area of focus will be workplace consultation and psychological health. Falls from heights were called out as a key issue to address in the construction industry, while in the agriculture industry, powered and mobile plant are the deadliest issues to address. In the manufacturing sector, there was a key geographic location of concern - being the 3175 post code (Dandenong and surrounds). The greatest number of injuries were caused by manual handling, with most fatalities being due to lung disease and traumatic injuries. The healthcare and social assistance sectors have safety issues in hazardous manual handling, aggression/violence and slips, trips and falls, which will be areas of focus for WorkSafe. The government sector continues to have major issues around psychosocial hazards. The highest risk of injury is seen in police services, followed by ambulance services and the department of education. However, in terms of fatalities, the worst areas are the Fire Services and Victoria Police. It was notable that employee representation and consultation were identified as a specific area of focus in a number of industries – and this is of course a key area for our Health and Safety Representatives! The Minister’s statements are strong: “Every workplace death is unacceptable – that’s why we are working towards a future of zero deaths and zero excuses.” "If a worker dies on your watch due to negligence, you risk criminal charges. We will not tolerate employers who gamble with workers' lives." We can only hope that this ‘new’ WorkSafe approach may lead to safer workplaces for all. To read the full press release from The Minister for WorkSafe: 250815-Workplace-Prosecutioncts-Hit-Successful-Milestone.pdf The full WorkSafe documents can be found at: Statement of Regulatory Intent 2025-26 | WorkSafe Victoria
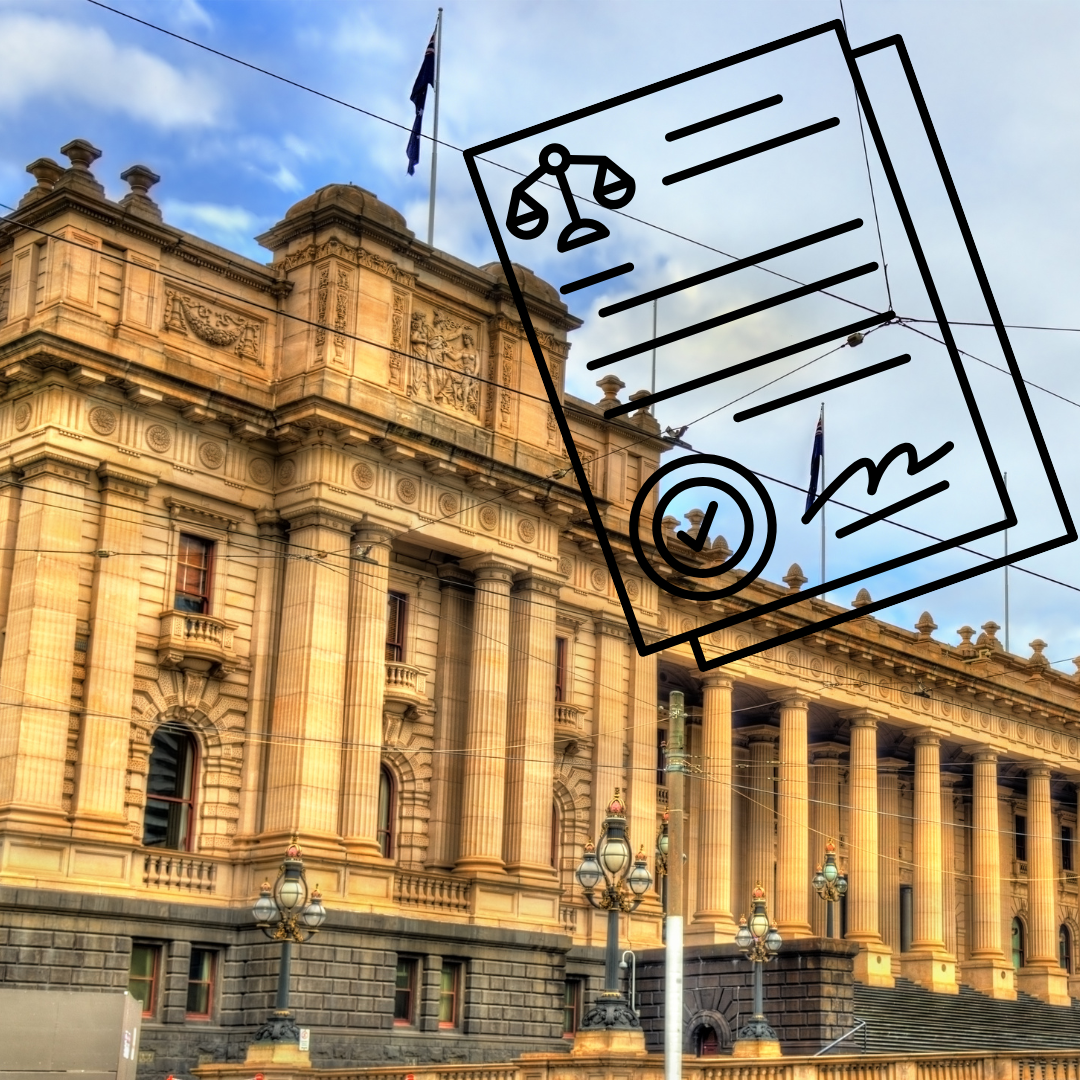
The Workplace Injury Rehabilitation and Compensation Amendment Bill 2025 has passed Parliament. It makes changes to three pieces of legislation: 1. The Workplace Injury Rehabilitation and Compensation Act 2013, 2. The Occupational Health and Safety Act 2004 and 3. The Accident Compensation Act 1985 The changes aim 'to improve support for injured workers and their families in Victoria, enhancing compensation entitlements and rehabilitation processes.’ In summary, the key provisions of the Bill are: 1. Code of Claimants' Rights to be created to ensure injured workers are treated with dignity and respect 2. Lived Experience Membership on WorkSafe Committees . It is now required that there be lived experience membership on the WorkSafe Board Advisory Committees, creating a ‘seat at the table’ for those personally affected by poor safety practices. 3. Return to Work (RTW) Coordinators: Employers will be required to provide RTW coordinators with necessary assistance and training to improve return-to-work outcomes for injured employees. T he details of this are yet to be made clear, pending directives form The Minister and WorkSafe. There will be penalty units attached to this requirement. 4. Compensation for Families of deceased workers: The bill improves compensation by: a) Allowing for provisional payments be made to dependants following a work-related suicide. b) Extending the length of the provisional payment period from 13 weeks to 26 weeks for dependent partners of deceased workers. This will mean that dependants will be less likely to be left without an income while the claim is being processed. c) Increasing the weekly payments to the dependent children of deceased workers. This is an increase from 5% of ‘pre-injury average weekly earnings’ to 12.5%, allowing for improved financial support of children. d) Grief and Loss payments to be made to close family members following the death of their loved one. This will acknowledge the loss of family members who previously had no eligibility for compensation. 5. Broader Support Services: The amendments will allow access to a wider range of therapy and support services for families affected by work-related deaths and serious injuries. This change allows for ‘support services’ to be broader than just psychology. 6. I ndependent Review Requirement: The bill mandates an independent review of the workers' compensation scheme at least every five years, starting in 2030, to ensure ongoing improvements and accountability. The Bill passed the Victorian Parliament on the 31 st July 2025. The primary aim of the Workplace Injury Rehabilitation and Compensation Amendment Bill 2025 is to strengthen the support system for injured workers and their families. It also requires for injured workers to be treated with dignity and respect during their recovery and rehabilitation processes. Any improvement to the support of those affected by work related injury and death can only be a good thing. For more detail on the changes, take a look at: Workplace Injury Rehabilitation and Compensation Amendment Bill 2025 | legislation.vic.gov.au
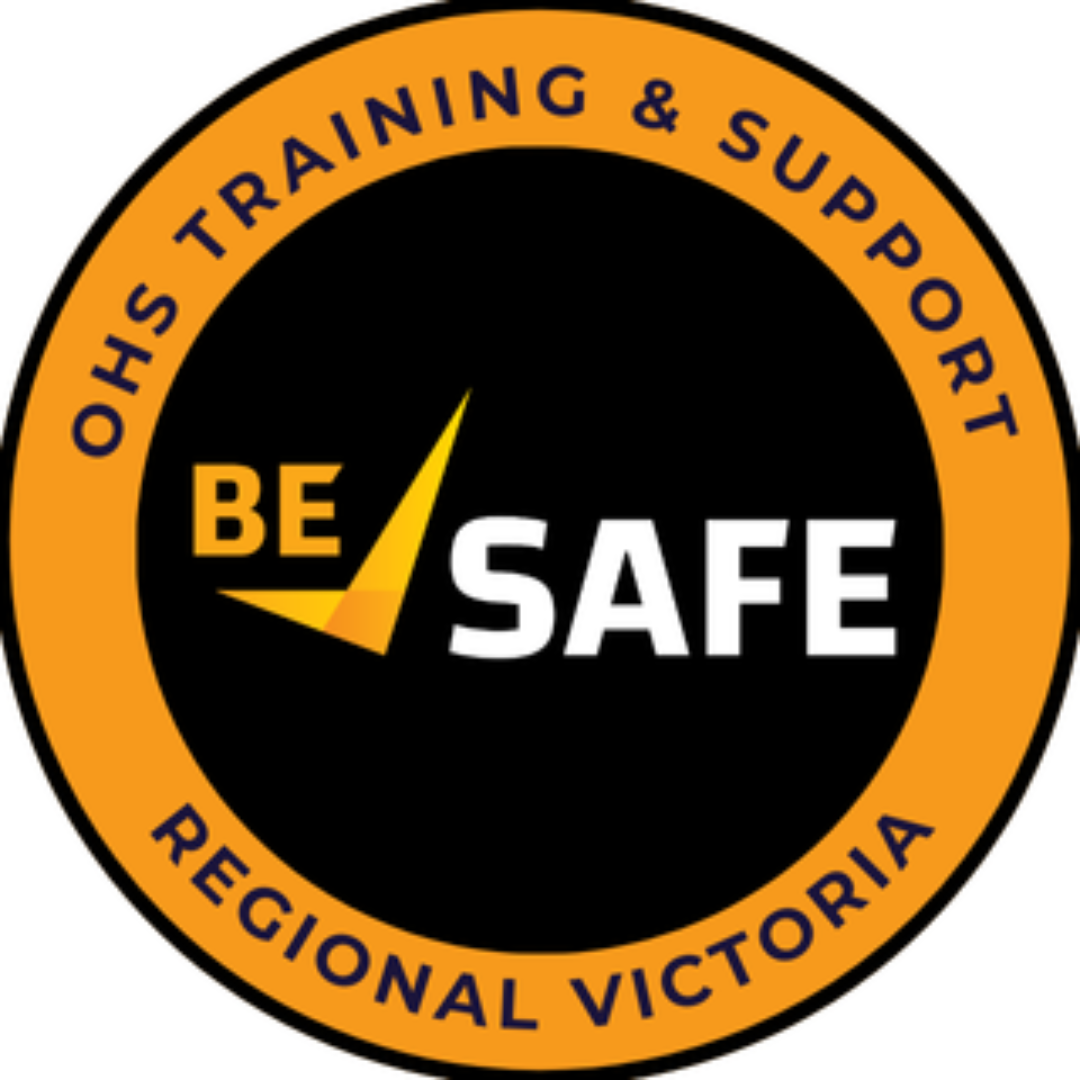
When it comes to workplace safety, the stakes are high. When it comes to safety training, BeSafe Victoria has emerged as a leader, setting the gold standard for occupational health and safety (OHS) education in Regional Victoria. Here’s why they stand out as the best safety trainers: 1. Passion for Safety At BeSafe Victoria, safety isn’t just a job—it’s a calling. Their team lives and breathes safety education, driven by a genuine passion for creating safer workplaces. BeSafe Victoria’s team is driven by a genuine commitment to creating safer workplaces. Their approach makes their training impactful and memorable. 2. WorkSafe-Approved As a WorkSafe-approved provider , BeSafe Victoria ensures their courses meet the highest standards. Their Health and Safety Representative (HSR) training courses include 5 Day HSR Initial OHS Training and 1 Day HSR Refresher OHS Training Courses. This stamp of approval ensures participants receive credible and up-to-date training, with the added benefit of BeSafe’s passionate delivery and follow-up support. 3. Regional Reach with Local Expertise Although headquartered in Ballarat, BeSafe Victoria’s impact extends far beyond. Their experienced trainers are available to deliver courses across all regional areas of Victoria, ensuring that even remote workplaces have access to top-tier safety education. BeSafe have booked courses in Morwell, Shepparton, Wodonga, Ararat, Portland, Traralgon, Bendigo and more. This regional focus makes them an invaluable resource throughout the state – booking courses anywhere there is a demand – just get in touch. BeSafe is passional about bringing OHS training to where it is needed most – in Regional Victoria. 4. Ongoing Suppor t Beyond Training Their commitment doesn’t end with training - BeSafe is committed to providing ongoing support. BeSafe offers free follow-up support and assistance to help their network of participants after they finish training and are working to resolve safety issues in their workplace. 5. Leaders training for Every Workplace BeSafe knows that being a great leader means understanding your OHS obligations. They also understand that many managers and supervisors don’t feel confident that they have enough OHS knowledge. That’s why BeSafe have developed a Leaders Introduction to OHS Course – to help managers and supervisors develop their OHS Leadership skills and understanding. Safety Starts with BeSafe Victoria In a world where workplace safety can mean the difference between life and death, choosing the right training provider is crucial. BeSafe Victoria’s passion, expertise, and commitment to excellence make them the clear choice for Regional Victorians. Ready to take the first step toward a safer workplace? BeSafe Victoria is here to guide you every step of the way. Get in touch at: HSR Training and support | BeSafe | Regional Victoria
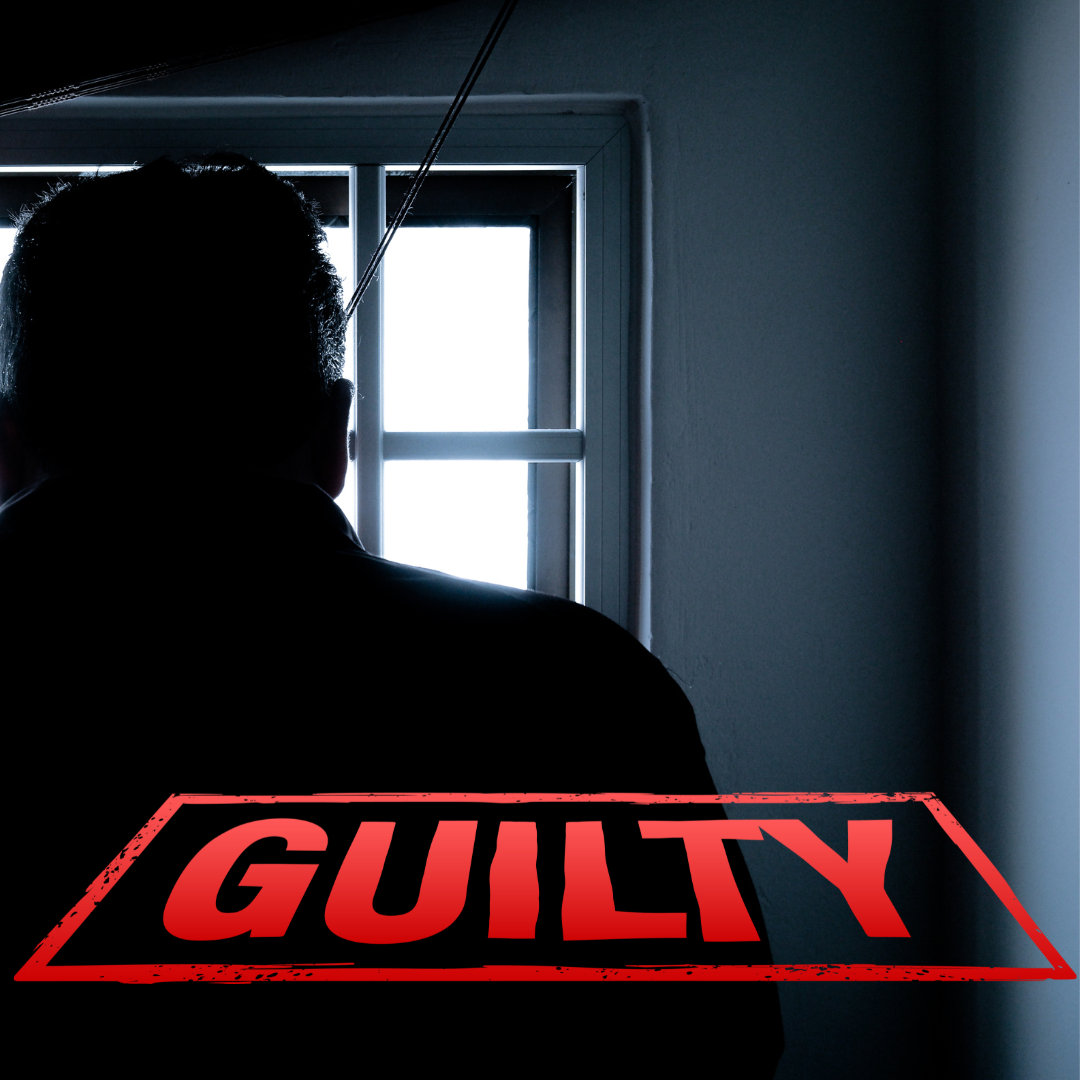
An updated list has been published of The ‘BIGGEST BIGGEST OFFENDERS’ in OHS Crimes . This list names and shames the companies which have been deemed worthy of the largest fines handed down by judges for offences under the Victorian Occupational Health and Safety Act 2004 . It makes an interesting, albeit sobering, read. The list (see below) has been compiled and published by the OHSIntros BLOG and has recently been updated with offenders from the last 2 years. In the last 35 years, according to OHSIntros ’ records, there have been 31 cases which have incurred a fine over $500,000. These companies have been collectively responsible for the deaths of 23 workers and a number of other serious incidents. 21 of these incidents involved plant, thus representing the majority of the cases. The incidents are all horrific, with many involving crushing, entrapment and falls – leading to violent deaths and horrendous injuries. The top fine was a penalty of $3 million, as a result of LH Holdings Management Pty Ltd being charged under Workplace Manslaughter Legislation and fined in 2024. A number of high-profile cases can be seen on this list. However, there are many well known cases which are not featured here, due to the fact that their sentences did not hit the $500K threshold. This perhaps raises concerns relating to The Sentencing of OHS Offences in Victoria . The list is a sobering one, listing a series of gruesome and tragic deaths – the result of safety crimes. In the words of OHSIntros’ – these are “the worst of crimes because [they] could have been prevented.” Image sourced from OHSIntros BLOG: https://www.facebook.com/100064446622188/posts/1127076076117269/?mibextid=rS40aB7S9Ucbxw6v *OHS Intros is a Workplace Safety page which provides ‘training, documentation and advice on Workplace Safety’: Facebook
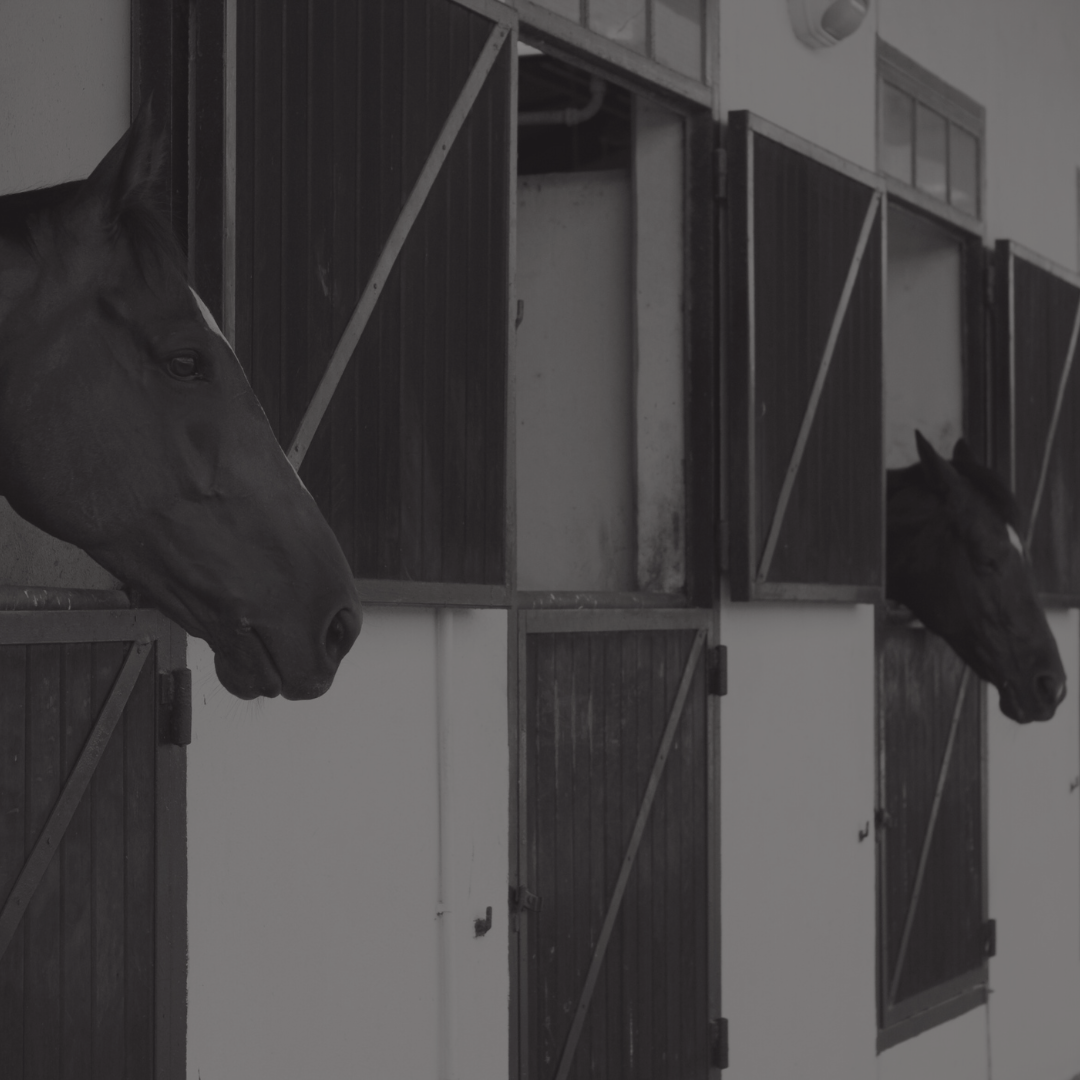
In recent times we have seen the tragic deaths of workers in the horse racing industry. In May 2025, Fiona Ralph tragically died following a head injury sustained while working at Bendigo Racecourse. Less than 2 months later, on the 3 rd July 2025, we heard news of Peta Tait, a 43-year-old worker who was killed at Cranbourne Racecourse. It is believed that she was kicked in the head by a horse while in the stable. She was attended to by medical personnel, who were unable to save her. Jockey Blake Shinn has reportedly paid tribute, stating that “This is a painful reminder of the dangers that come with working in such a demanding and unpredictable environment.” (7 news) As the jockey highlights the dangers – we turn our minds to the unique hazards presented by the industry, many of which are covered in the WorkSafe Victoria Guidebook – Horse Stable and track riding safety: Horse stables and track riding safety | WorkSafe Victoria . The guide is intended to provide information for those working in the industry and outlines how to identify hazards and implement risk control measures. As in all industries, the employer is responsible for providing a safe workplace, and the usual obligations to consult with the workforce and to control hazards in line with the hierarchy of control all apply. There is a section which specifically covers the safety of stables. Of course, horses are strong and unpredictable, and they pose a specific hazard in this industry - and one which cannot be eliminated as part of this particular workplace. The document discusses the need for training and supervision, which is required in all workplaces. Also, the use of PPE as a control measure, indicating that the use of appropriate footwear, helmets and body protection may be required to ensure the safety of those riding, training, feeding and working with horses and cleaning stables. Working alone can also increase the risks of working around horses. According to SafeWork NSW ‘One worker is hospitalised each day in Australia due to a horse related injury’ . Not all of these are workers; however, it does highlight how dangerous working around horses can be. WorkSafe Victoria reports injury claims attributable to horse racing at: Injury hotspots - Horse racing | WorkSafe Victoria . While the racing community must, of course, grieve the recent loss of two of its’ workers, there will concurrently be a WorkSafe investigation and a Victoria Police investigation for the Coroner. No matter the outcome of these investigations, it is an opportunity to look to industry work practices and identify any improvements which could be made to improve safety in the future. The gravity of such an event cannot be underestimated in its’ impact to family, friends and workmates. One can only hope that an improvement in future safety may be one of those impacts. Our sincere condolences to the families of Fiona and Peta.
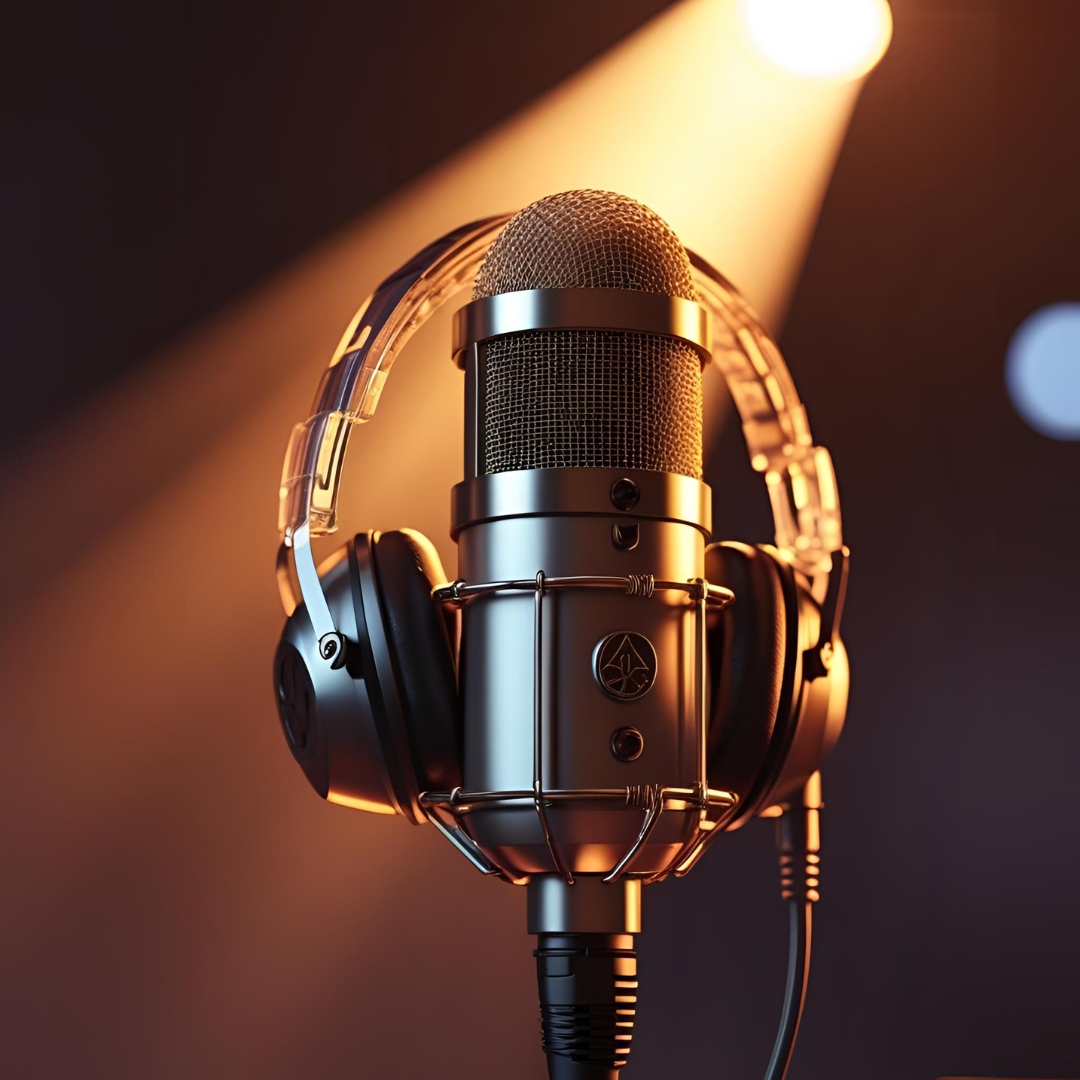
The rise of podcasts has made learning and information so accessible and learning about OHS is no different. We came across the WorkSafe Act podcast ‘The Safety Spotlight’ episode on ‘Small Business’. In this podcast, Jacqui Argius, the WorkSafe ACT Commissioner talks about safety in small business . She is joined by Michelle Boundy in a podcast led by Lish Fejer. They discuss a number of matters relating to safety in the small business environment, which are summarised below. Small businesses are required to be compliant with safety legislation, no matter how small they are. It is often the case that small businesses have less OHS expertise. Sometimes they may think that a serious incident ‘won’t happen here’. They may not have a good understanding of what their legal obligations are. Sometimes there may be a ‘fear factor’ about their lack of understanding of how to meet their legal obligations. They may think that they are too small to need proper systems. But – just because they are small, this doesn’t mean that they don’t need to meet the same requirements as the larger businesses when it comes to safety, and this includes both physical and psychosocial safety. Small businesses must also have WorkCover insurance. Like in all businesses, consultation is key. ‘Talking to your workers’ is so important to ensuring a safe workplace. This includes ensuring that young workers and those from culturally and linguistically diverse backgrounds can understand. Guidance material regarding how to communicate safety information is available. The importance of training is also covered. Small businesses must have an induction process and ongoing training for their workers. Employees must also be trained in how to report hazards. The application of risk management systems and the hierarchy of controls is the same in small business as in any workplace, as is the concept of ‘ reasonably practicable ’. The commissioner highlights that the cost of implementing a control will not be considered to be important if a matter goes to court. The employer must eliminate or implement controls to all risks to health and safety. The podcasters acknowledge that there are a myriad of pressures on small businesses – but highlight that this does not reduce their obligations in relation to safety. Nor does it exempt the business from enforcement by the regulator: ‘we will be regulating them the same as anyone else’. Overall, the podcast highlights the need for small business owners to be pro-active and build a safety-first culture. To listen to the WorkSafe ACT Small Business Podcast, check out: Ep. 2 - Small Business There are many resources available to small business to ensure that they are providing and safe and healthy workplace. In Victoria these include: Getting some help from WorkSafe through the OHS Essentials program, which is free to small business and a great place to start. Accessing health and safety checklists as a way to begin a self-assessment. Reading about your obligations and legal requirements. Take a look at the WorkSafe website to access these resources here: Small business | WorkSafe Victoria
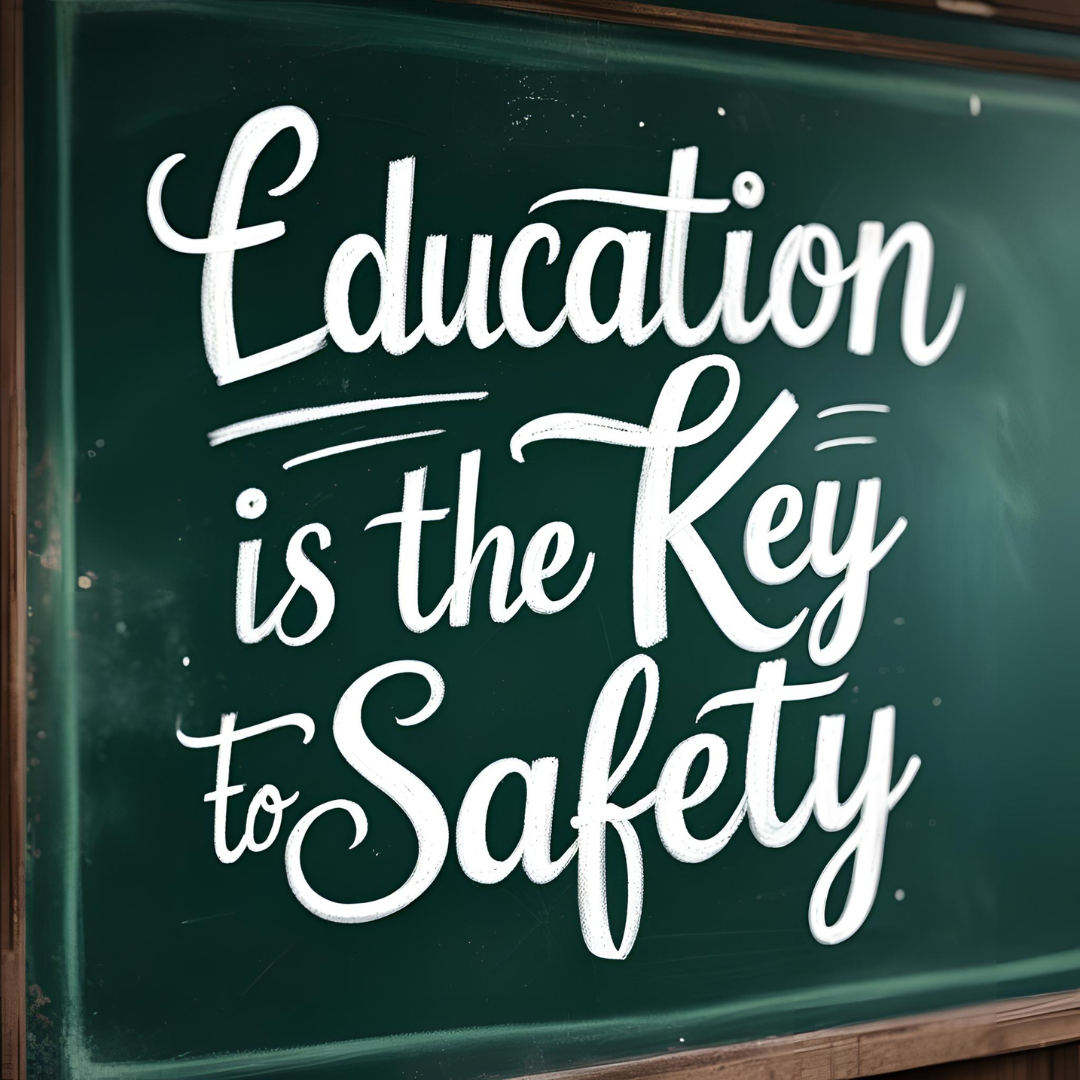
At BeSafe Victoria, we live, eat and breathe safety education. Why? Because we believe it is the key to workplace safety. We see and hear the on-the-ground OHS stories from our participants on a daily basis, both during training and while providing follow-up support. It is remarkable to see the transformation that occurs during a training course, as participants grow their safety knowledge and become empowered to influence their own safety and that of their workplace. In regional Victoria, it is not uncommon for OHS Literacy to be very low. This is not in all workplaces, but certainly our experience shows that many workers have received very little or no training in OHS. By gaining an understanding of OHS, we can empower individuals to keep themselves safe. This includes in understanding their rights, recognising hazards, mitigating risks and knowing when to say no to unsafe work. Training an individual also means that they can bring this new knowledge to their workplace, leading to positive improvements in safety outcomes for their colleagues. Safety training has broader implications too – it can inspire conversations with family and friends, creating a ‘ripple effect’ of improved safety awareness in the community. We often see participants who deeply care about safety and have put their hand up to become a Health and Safety Representative (HSR) in their workplace. These participants come in with the drive and walk out with the tools and the passion they need to make a really tangible difference in their workplace. We know of many stories of trained HSR’s who go on to transform the safety of their workplaces. Whether we are duty holders, supervisors, HSR’s, or employees – we all have a role to play in the safety of our workplace – and with the right knowledge, we can make a positive contribution. What truly underpins a safe work environment? The answer lies in education .
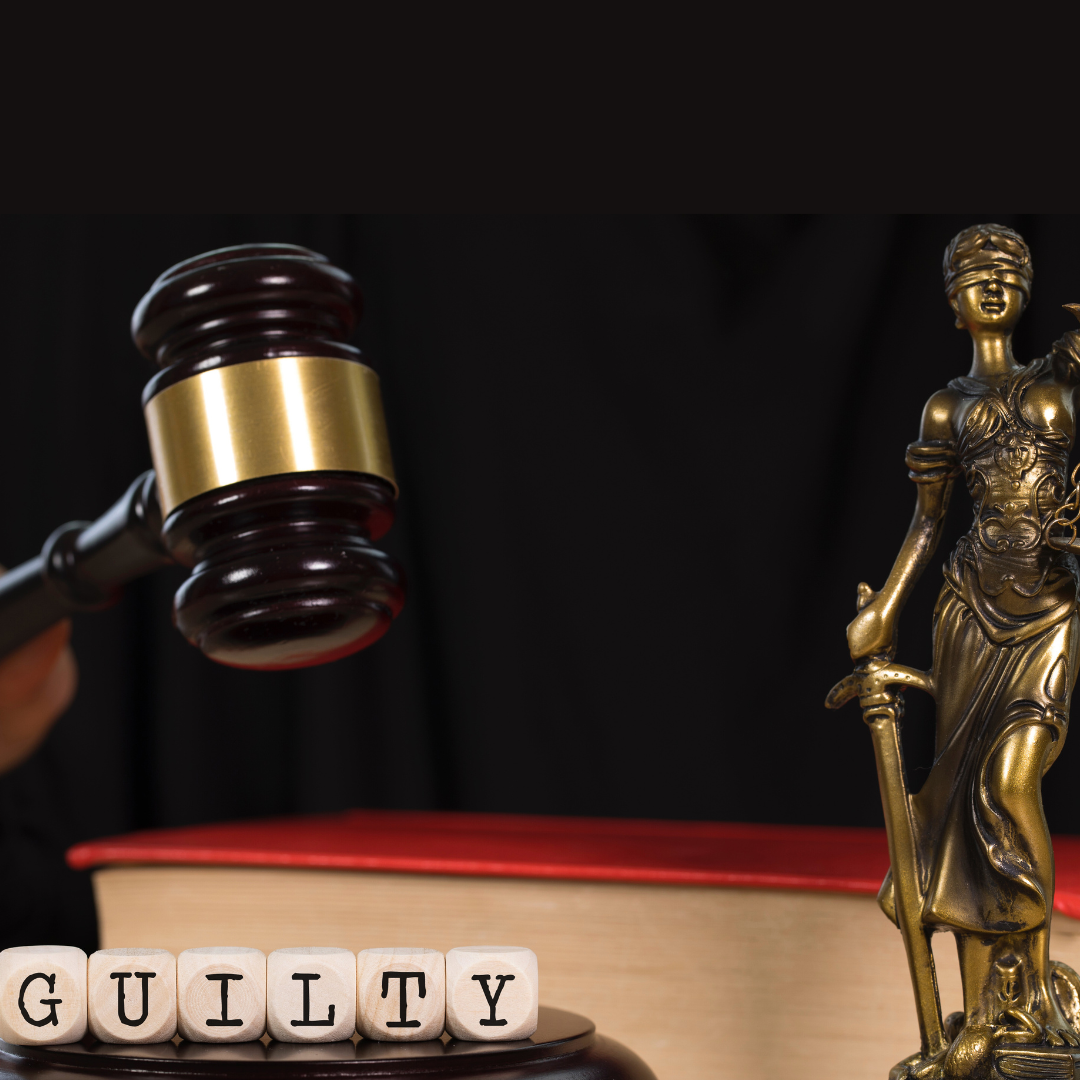
The Victorian Occupational Health and Safety Act 2004 is primarily a risk-based law. That is, it requires the prevention of harm. The objects of the Act require that health and safety be secured and that risks to health and safety be eliminated at the source, with the highest level of protection against risks being provided. The employer is legally required to eliminate (as far as reasonably practicable) any risk to health and safety. It follows that the majority of offences under the Act are indeed risk-based offences. This means that a prosecution can occur whether or not the risk has resulted in death or injury. It is enough to have simply exposed a person to the risk of harm. The argument for this is that the OHS Act aims to prevent injury, disease and death at work. So why do we see many prosecutions occurring after the harm has in fact materialised into an injury or death? Perhaps it is due to a public expectation that these horrific incidents should result in some punishment of those responsible? Perhaps it is that the ultimate evidence of the safety failure is now present – providing a compelling argument as to the egregious nature of the risk that was posed by the breach? Perhaps there is motivation to provide general deterrence as a result of these tragic events? It is important to note that the death or injury does not form part of the offence in these prosecutions, rather it forms part of the evidence. But, we do see pure risk prosecutions. The regulator can and does charge on the basis of risk only, before the safety failure has resulted in harm to anyone. This is the ultimate outcome – to prevent . Prosecuting on the basis of risk may be for the purpose of primary prevention, or as the ultimate escalation in a hierarchy of sanctions. It may serve as specific deterrence, to effect change in an individual’s or company’s behaviour. General deterrence is often seen as very important – reinforcing to all duty holders that they are required by law to take a pro-active approach to safety. Here are a few examples of cases of pure-risk prosecutions: $7.5K FINE IN PURE RISK FALLS CASE - OHS Reps $25K FINE IN AHWAZ ROOFING PURE RISK CASE - OHS Reps CONSTRUCTION COMPANY FINED $12K IN ‘PURE RISK’ PROSECUTION - OHS Reps The following Melbourne Law School presentation also makes for some interesting reading on this topic: CELRL-Seminar-21-May.pdf Proceeding to prosecution on the basis of risk represents an alignment between prosecution strategies and the principles of the OHS Act . Certainly, it serves as a reminder that duty holders have a legal requirement to provide the highest level of protection and to prevent harm in the workplace.
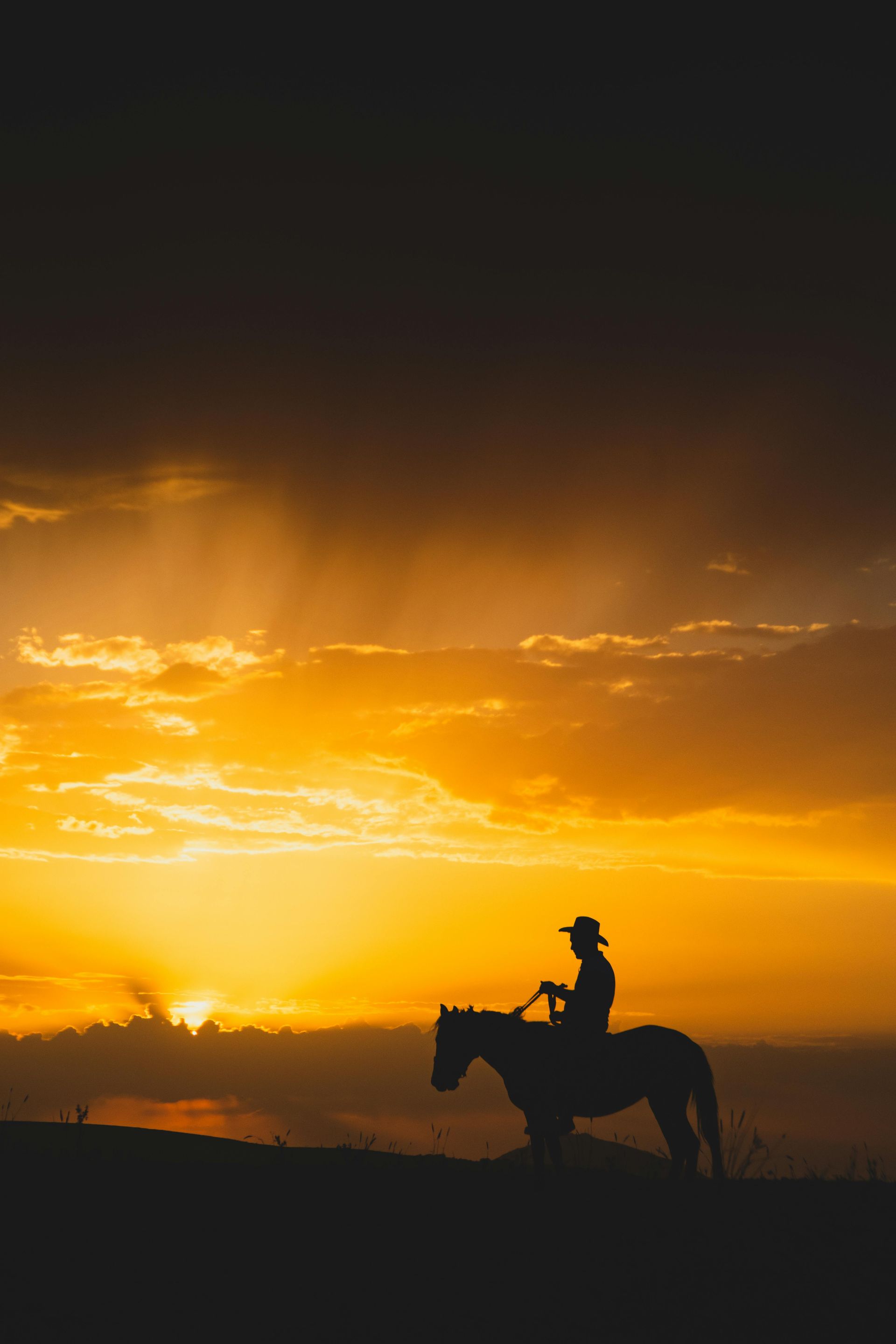
Farm workers are often working alone and in an isolated location where there is no assistance from others and often limited or no communication. Remote or isolated work often includes working alone and outdoors and it may be difficult to get help in an emergency. Access can be long and difficult and there may be limited access to resources. On top of this, there is less access to support networks and communication and technology may be unreliable or absent. All these factors can add to the risk of the work. These unique challenges should all form part of the thinking when working to create a safer workplace for those working on farms. The duty to provide a safe workplace sits with the employer, who has a legal requirement to provide a safe workplace for the workers on the farm. Often the employer may also work on the farm themselves, and the same hazards will pose a risk to them too. Implementing some controls to help reduce the risk of working alone on farms can help ensure that everyone gets home alive and well, including the employer/ farm owner. The control measures will depend on the exact type of work being conducted on the farm, but things to think about may include: Monitoring weather conditions and emergency warnings Ensuring some form of communication is available Providing personal distress beacons Ensuring all personnel have a first aid kit and are trained in how to use it Implementing a buddy system to reduce the time spent working alone Additional training provided to reduce the impact of isolated work Mental health support Farming will usually involve work which is dangerous, including machinery, powerlines, heights, animals, chemicals, and the list goes on. All these risks need to be controlled to a level which is reasonably practicable, but they become more dangerous when the worker is working alone or in an isolated location. Often even the most basic issue is not adequately dealt with – how to call for help? One of the most important issues is to consider is: Is there are reliable means of emergency communication? You must consider how you will know if something has gone wrong and how to locate the person in the case of an emergency. You may like to think about: Is there a check in procedure? Do you have a location system? Do you have a satellite communication or radio if there is no phone signal? Do you have an Emergency Locator Beacon with GPS for use in case of an emergency? If you have mobile coverage, have you considered using Emergency Phone Apps? For more information on this topic, including on how to develop emergency procedures, take a look at: Working alone on farms | WorkSafe Victoria and Working alone or in remote areas | Safe Work Australia It really is important to take the time to consider the risk of working on farms, especially when alone and in isolation. Not only do we need to do this to fulfil the legal duties under the OHS Act - but most of all, to make sure we all make it home at the end of the day.
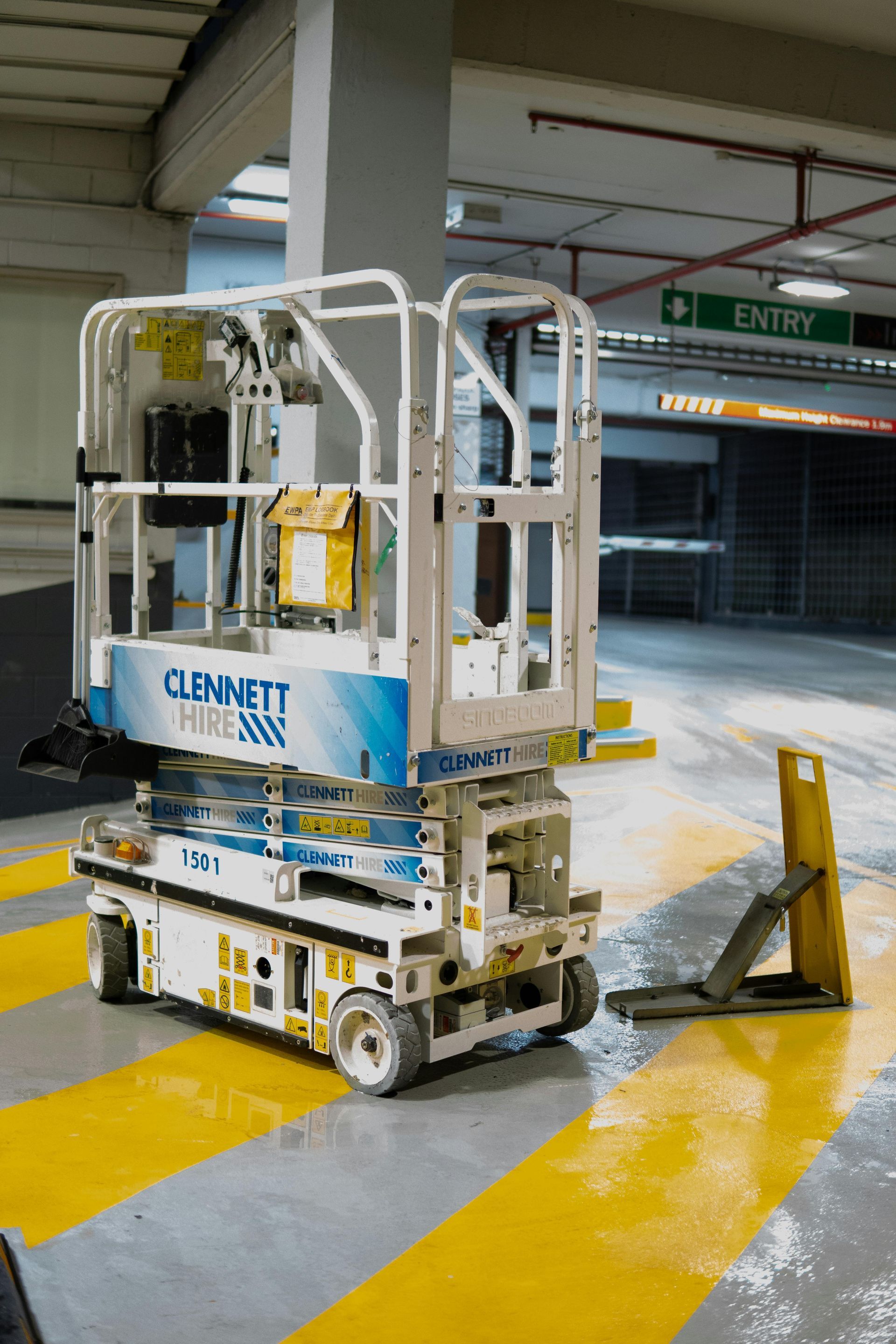
Elevated Work Platforms (EWP’s ) can take a number of forms including scissor lifts, vertical mast lifts and the various types of boom lifts/ cherry pickers. But no-matter which type, EWP’s are notorious - being responsible for deaths and injuries in the workplace. Recently in Victoria, there was a tragic incident which resulted in the death of an employee. The use of an EWP can expose an operator to multiple hazards, including: Electrical Crushing Falls Overturning Water Falling objects Collision Environmental hazards All people who are involved in the use of an EWP must be trained, competent and supervised. This includes the operator and the observer or spotter. For boom type EWP’s, a High Risk Work License (HRWL) is also required. Electrical Spotters training is also required if the EWP will be operated in an area where there are power lines. Use of EWP’s which classify as High Risk Construction Work will also require work to be conducted in accordance with a Safe Work Method Statement (SWMS). The use of harnesses may also be required and training in their use must be provided. Inspections and maintenance of the EWP must be undertaken, including pre-start checklists and procedures. There must be emergency procedures in place, including training in these procedures. Above all, a person operating an EWP must never work alone. When planning to use an EWP - The same principles apply as with all OHS matters – That is, that hazards must be identified and controlled, in line with the hierarchy of control. The employer has a duty to use the highest order control to protect their workers from harm. For more information on the use of Elevated Work Platforms, visit: Elevating-work-platforms-edition-4-2023-06.pdf or contact BeSafe Victoria HSR Training and support | BeSafe | Regional Victoria
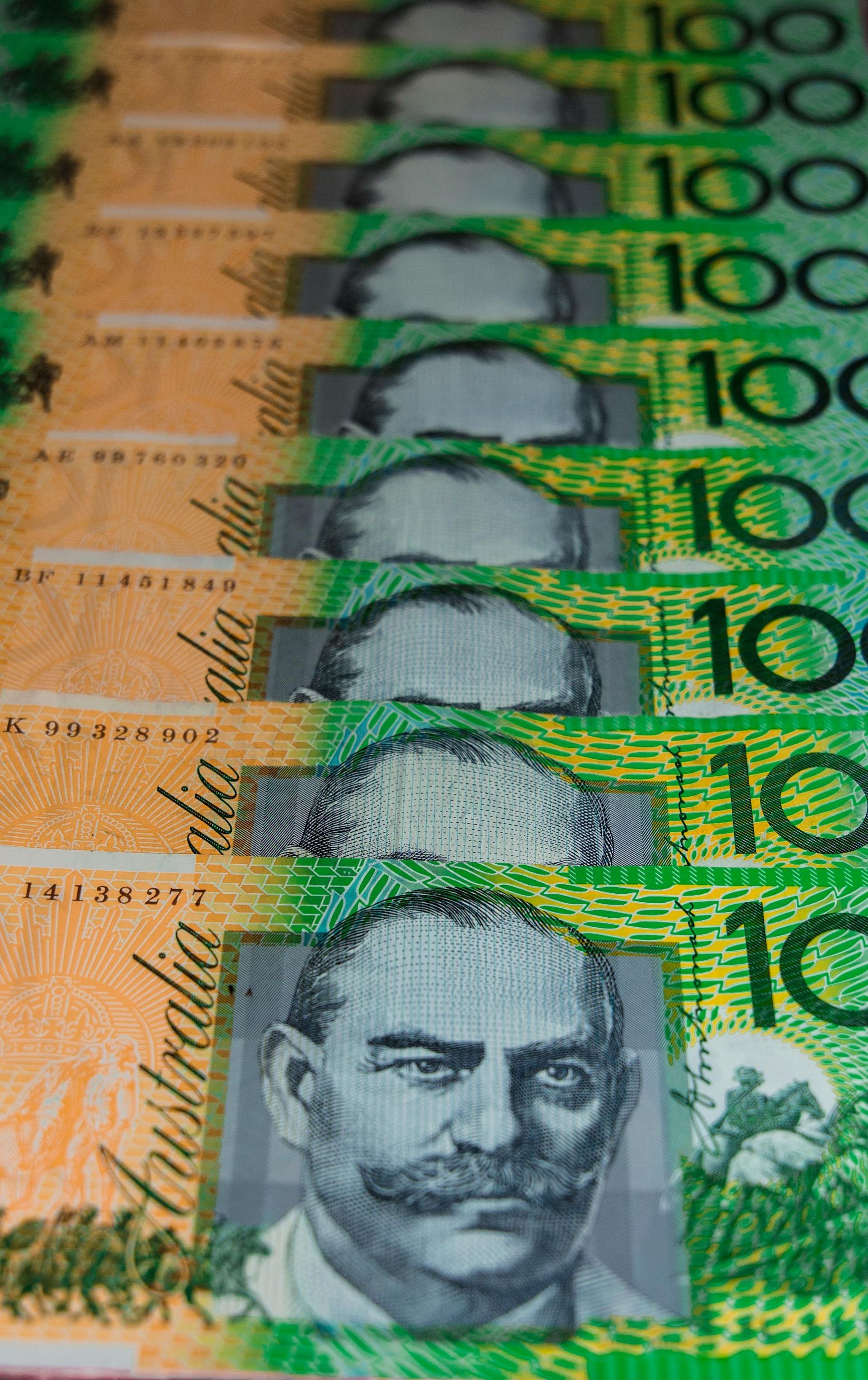
Since 2021, WorkSafe has been given the power to serve infringement notices for certain breaches under the OHS Act and its regulations. This means that WorkSafe Inspectors can issue on-the-spot fines in a similar way to a police officer who catches a person for speeding. The fines can be issued without the need to take the offender to court. The fines issued for offences are up to about $2000 (depending on the offence). Infringement notices are allowed to be used for certain offences, which broadly fall under 4 categories: undertaking work without a required licence, registration, qualification, experience or supervision using plant that is not licensed or registered as required failing to meet various duties relating to the removal and storage of asbestos failure to keep various required records A full list of infringement offences can be found at: Infringement offences | WorkSafe Victoria In 2021, there were also changes to ensure that the payment of penalties under the OHS Act cannot be covered by insurance. It is illegal to hold such insurance, and it is also illegal to provide insurance for penalties under the OHS Act. “The payment of a penalty cannot be covered by insurance. Any contract term or arrangement that claims to insure or indemnify a person for payment of a penalty under the OHS Act or regulations is void under section 148A of the OHS Act.” – WorkSafe Victoria This means that the offender must pay the fine – not their insurer.
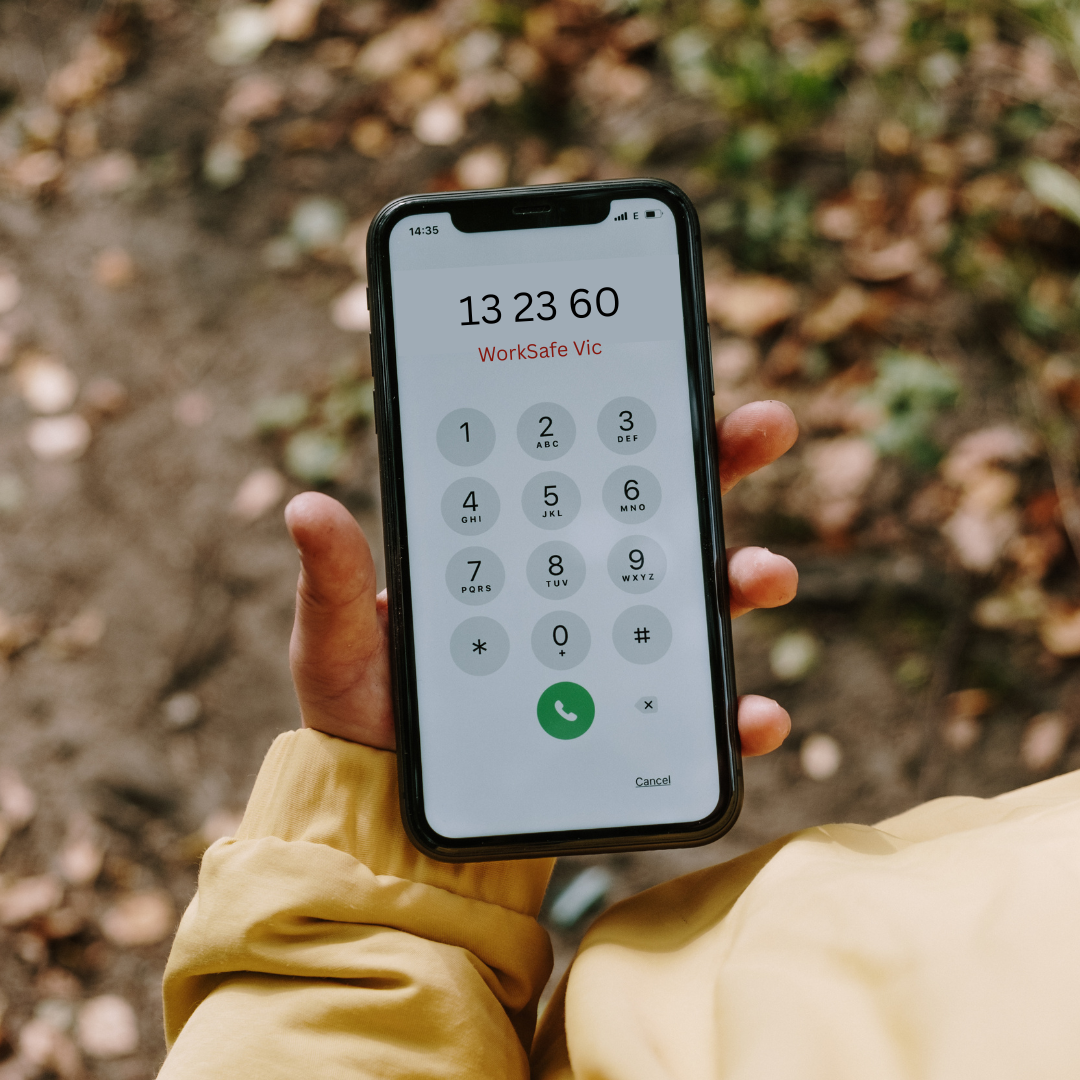
Section 38 of the Occupational Health and Safety Act 2004 imposes a legal duty on employers to notify of incidents: "An employer or self-employed person must not, without reasonable excuse, fail to notify the Authority immediately after becoming aware that an incident has occurred at a workplace under the management and control of the employer or self-employed person. s38(1) The employer must notify immediately by calling WorkSafe by calling 13 23 60, at which time they will be given a reference number. Thie reference number serves as proof that the employer did immediately notify the regulator." s38 The employer must fill out an incident notification form (found at Incident notification form | WorkSafe Victoria ) and this form must be submitted within 48 hours of the incident occurring. Failure to notify is a breach of legal duty and the offence can result in prosecution. It is also a legal duty for the employer to preserve the site of the incident. Failure to preserve the scene is an indictable offence under section 39 of the OHS Act. So, what classifies as a notifiable incident? Any of the following: 1. Death 2. Exposure to a substance resulting in a need for medical treatment within 48 hours 3. Any incident resulting in the need for immediate in-patient hospital treatment 4. Any incident result in the need for immediate medical treatment for any of the injuries listed: a. Amputation b. Serious head injury c. Serious eye injury d. Removal of skin (eg: scalping, degloving) e. Electric shock f. Spinal injury g. Loss of bodily function h. Serious lacerations (ie: requiring stitching or other medical treatment) 5. Any incident through which a person is at serious risk as a result of exposure to an: a. Uncontrolled escape, spillage, or leakage of a substance b. Implosion, explosion or fire c. Electric shock d. Fall or release from height of any plant, substance or thing e. Incident involving plant (collapse, overturning, failure or malfunction) as per OHS Regulations f. Collapse or failure of an excavation or mine (or of any shoring support) g. In-rush of water, mud or gas into an excavation, tunnel or mine h. Interruption of ventilation in a mine, excavation or tunnel i. Any incident involving dangerous goods or explosives WorkSafe has a straightforward guide on the process here: Report an incident | WorkSafe Victoria Don’t forget that as Health and Safety representative, you have the right to access information in relation to incidents which affect your DWG. For more information on this topic, take a look at previous articles relating to relating to HSR’s entitlements to access information: HSR Training & Workplace Safety | BeSafe | Reg. Vic. For more detail on this, visit Obligations of an employer to health and safety representatives | WorkSafe Victoria As always, you are welcome to get in touch with us for a chat HSR Training and support | BeSafe | Regional Victoria
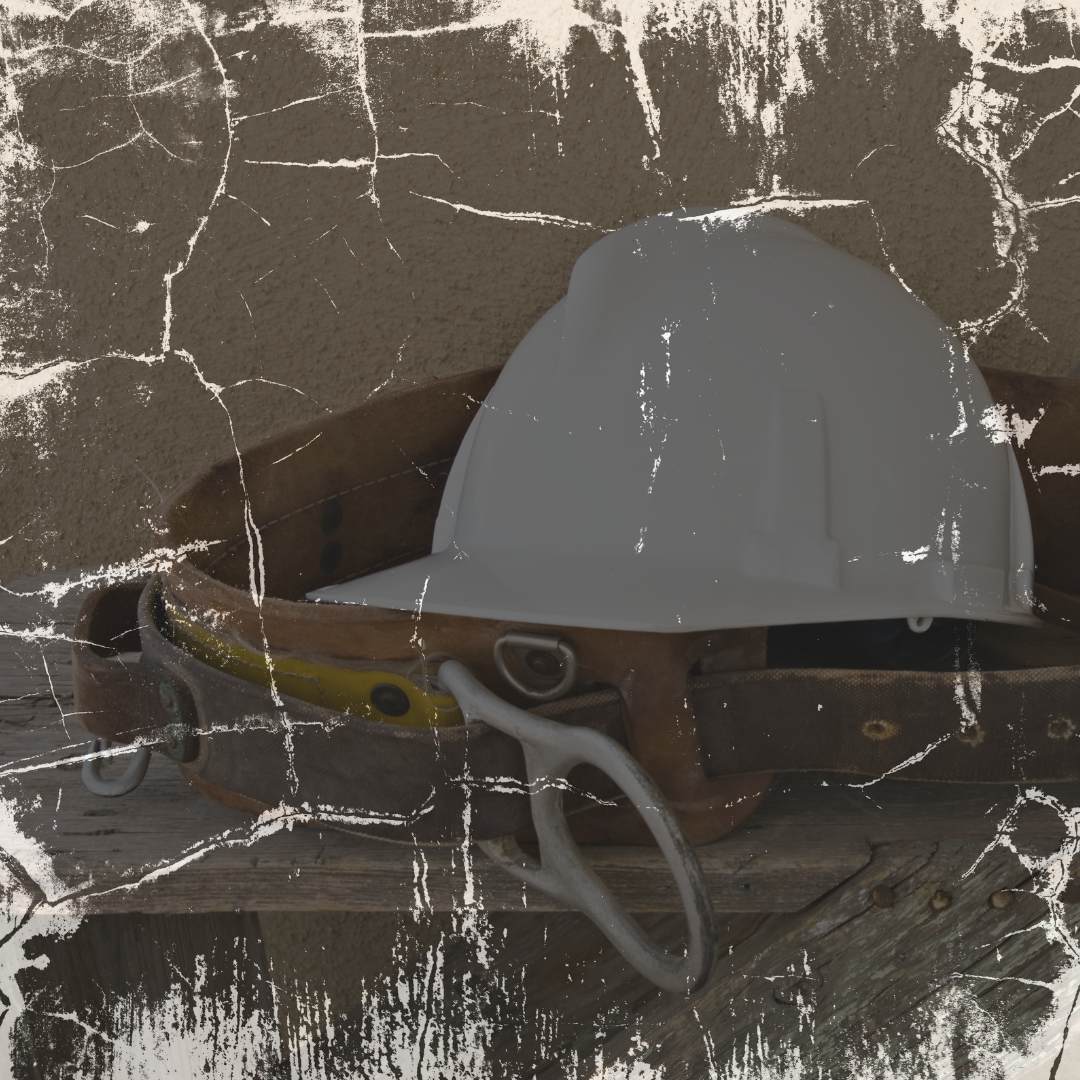
Young workers are at among the most vulnerable in the workplace. They are at an increased risk of injury or death at work. There are a number of factors which contribute to this, including: Being new to their job or industry Not knowing what their OHS rights are Not having OHS training Not being supervised sufficiently Have less experience in their role Feeling afraid to speak up about safety issues Not knowing how to report safety issues Being under pressure by other workers or their employer Insecure work Employers have a duty to provide a safe workplace to their employees, and particular care should be taken to ensure the safety of the young and vulnerable workers. Read more about this at Young workers: Safety basics | WorkSafe Victoria . When a young worker is killed at work, the ramifications are devastating. In these videos, two brave fathers describe what happened when their sons went to work and never came home: Workplace Incidents Consultative Committee: David Brownlee's story | dtf.vic.gov.au Workplace Incidents Consultative Committee: Brett Struhs' story | dtf.vic.gov.au Both companies were charged following the deaths of these young men, but nothing will bring them back to their families. Both stories highlight the importance of protecting young workers from hazards in the workplace, as is the duty of the employer.
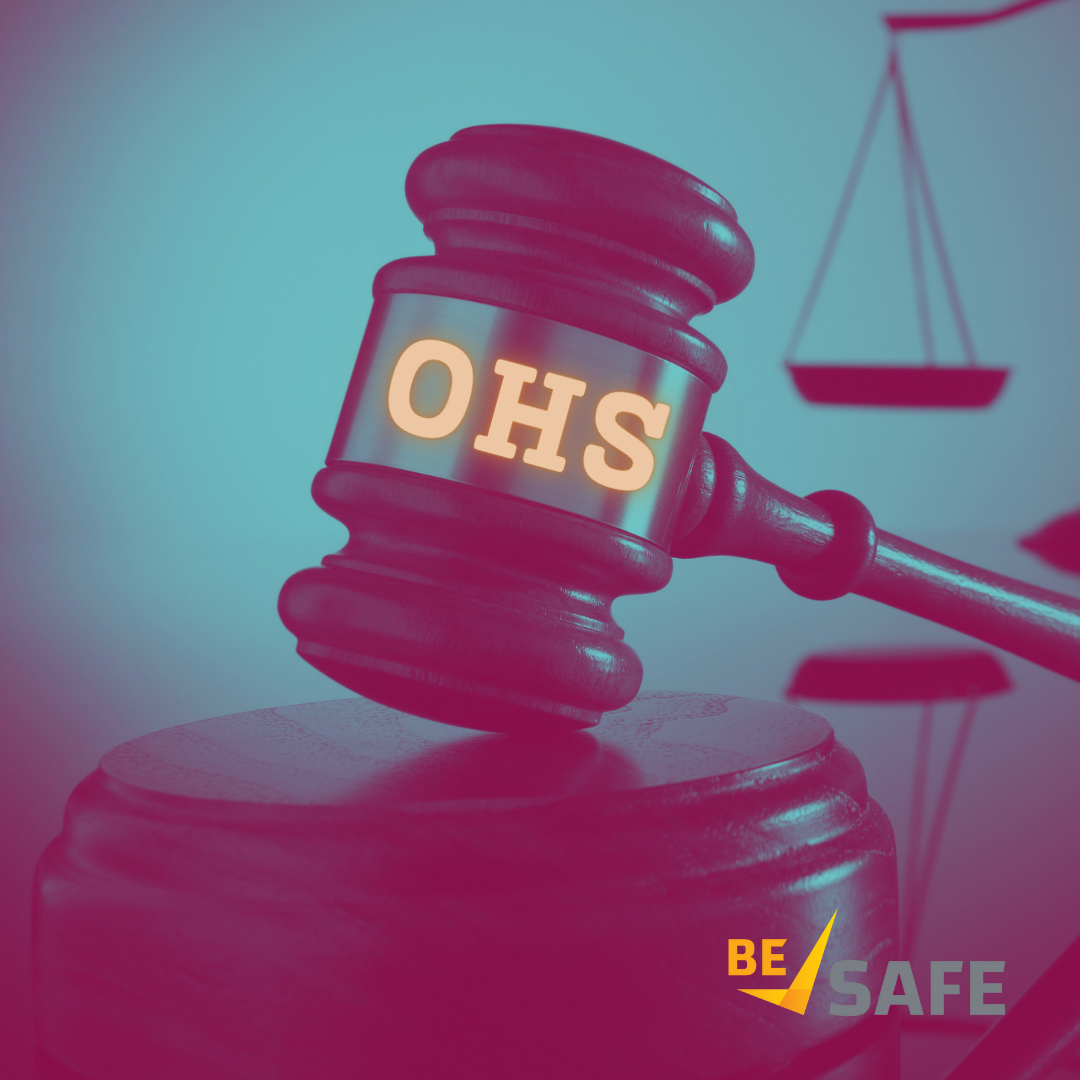
Judge Peter Rozen is currently a Judge in the County Court of Victoria where he was appointed in 2022. His name is well known, due to his long history as an expert in Occupational Health and Safety law. Judge Rozen has been involved in a number of high-profile reviews and inquiries, and he co-authored a textbook on the subject: ‘Health and Safety Law in Victoria’. Recently, Judge Rozen presided over the case of DPP vs Energy Australia Yallourn Pty Ltd , where he gave his sentencing remarks on 27 th March 2025. This case was a pure risk prosecution relating to a fire at the power plant, which resulted in the conviction of Energy Australia for breaching section 21 of the OHS Act. The County Court broadcast the sentencing remarks on YouTube: Sentence of DPP v Energy Australia Yallourn Pty Ltd before Judge Rozen – 27 March 2025 in what was a helpful move to make access to his commentary more accessible to those wanting to learn from OHS rulings. Judge Rozen took the opportunity to explain the way in which employers must engage in risk assessment including the consideration of the likelihood of the event occurring and its’ potential consequence. He also took the time to explain that employers must provide the highest level of protection against risks to health and safety and that they must be proactive in their duty to provide a safe workplace, as well as to monitor conditions and to engage suitably qualified persons in relation to OHS. Notably, he highlighted the need for meaningful consultation and the fact that employees are entitled to be represented (by and HSR). Rozen went on to delve into the concept to ‘ reasonably practicable ’ and described how the ‘more ‘reasonably practicable’ an identified risk control measure was, all else being equal, the more egregious will be the failure to have implemented it’. Judge Rozen’s closing remarks were a strong reminder to duty holders as to their legislated responsibilities under the Law: ‘It has been stated by the Court of Appeal on more than one occasion that employers are required by the Act to take an active, imaginative and flexible approach to the safety of those who may be affected by their undertakings. An employer must actively identify risks to health and safety and take all steps that are reasonably practicable to obviate those risks. Employers are not allowed under the law to take a passive approach to safety only improving safety procedures after an incident... fines in OHS cases must draw attention to the importance of workplace safety, and send a message to employers that failure to eliminate or mitigate safety risks will attract significant punishment.' The full transcript is available at: sentencing-remarks-dpp-v-energy-australia-yallourn.pdf And the video can be viewed at: Sentence of DPP v Energy Australia Yallourn Pty Ltd before Judge Rozen – 27 March 2025 Any HSR, employer or person interested in OHS would benefit from listening to the comments of Judge Rozen. In particular, his educational comments which I have summarised are found at around the 11.30 mark.
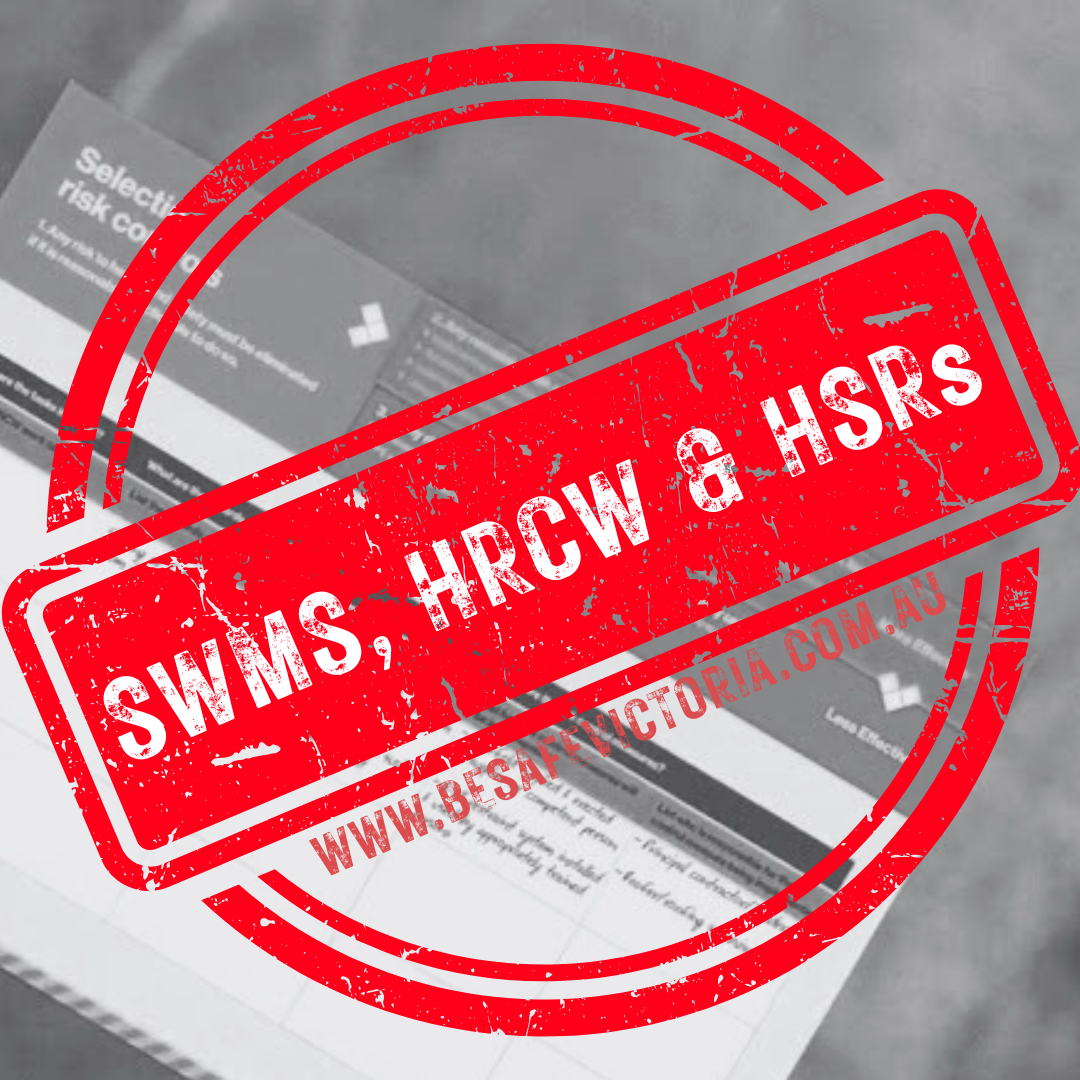
HSRs should be involved when a SWMS is prepared for HRCW. Who doesn’t love an acronym? Let’s start with some definitions... SWMS stands for Safe Work Method Statement. This is a document which must be prepared before any HRCW commences. It sets out how the HRCW is going to be carried out at the workplace. It includes an outline of the hazards involved and what control measures are to be put in place to control the risks. HRCW stands for High Risk Construction Work. It is defined in Regulation 322 of the Occupational Health and Safety Regulations 2017 : In this Part, "high risk construction work" means any of the following construction work— (a) where there is a risk of a person falling more than 2 metres; (b) on telecommunications towers; (c) involving demolition; (d) involving the removal or likely disturbance of asbestos; (e) involving structural alterations that require temporary support to prevent collapse; (f) involving a confined space; (g) involving a trench or shaft if the excavated depth is more than 1·5 metres; (h) involving a tunnel; (i) involving the use of explosives; (j) on or near pressurised gas distribution mains or piping; (k) on or near chemical, fuel or refrigerant lines; (l) on or near energised electrical installations or services; (m) in an area that may have a contaminated or flammable atmosphere; (n) involving tilt-up or precast concrete; (o) on or adjacent to roadways or railways used by road or rail traffic; (p) at workplaces where there is any movement of powered mobile plant; (q) in an area where there are artificial extremes of temperature; (r) in, over or adjacent to water or other liquids where there is a risk of drowning; (s) involving diving. “Construction Work” means "any work performed in connection with the construction , alteration, conversion, fitting out, commissioning, renovation, refurbishment, decommissioning, or demolition of any building or structure , or any similar activity." So, what role can HSRs play when it comes to SWMS? Health and safety representatives play a key role in the safety of their workplaces, including in relation to SWMS: As with all Health and Safety matters, the HSRs can and should be involved if the work affects their designated work group (DWG). As part of their legislated duties, the employer must consult with the employees and their HSRs. The HSR can play and important role in reviewing the SWMS and raising any concerns from their DWG. If conditions change, or if risks are not adequately controlled, then a SWMS must be reviewed. HSR’s are well placed to detect when this is the case and therefore bring this to the attention of their employer. HSRs and their workmates in their DWG are the best people to help in designing and reviewing SWMS, as they are the ones actually doing the work. They will have hands-on knowledge of how the job is done, any relevant site-specific factors, what hazards and risks are present, how best to control them and know if conditions change on-site (eg: weather). HSRs may also be able to help ensure that their co-workers fully understand the SWMS and are ready to go and do their work safely. After all, the purpose of the SWMS is to ensure that they are safe while they do their work! For further reading, there is some great material on this topic at: Safe Work Method Statements (SWMS) | WorkSafe Victoria
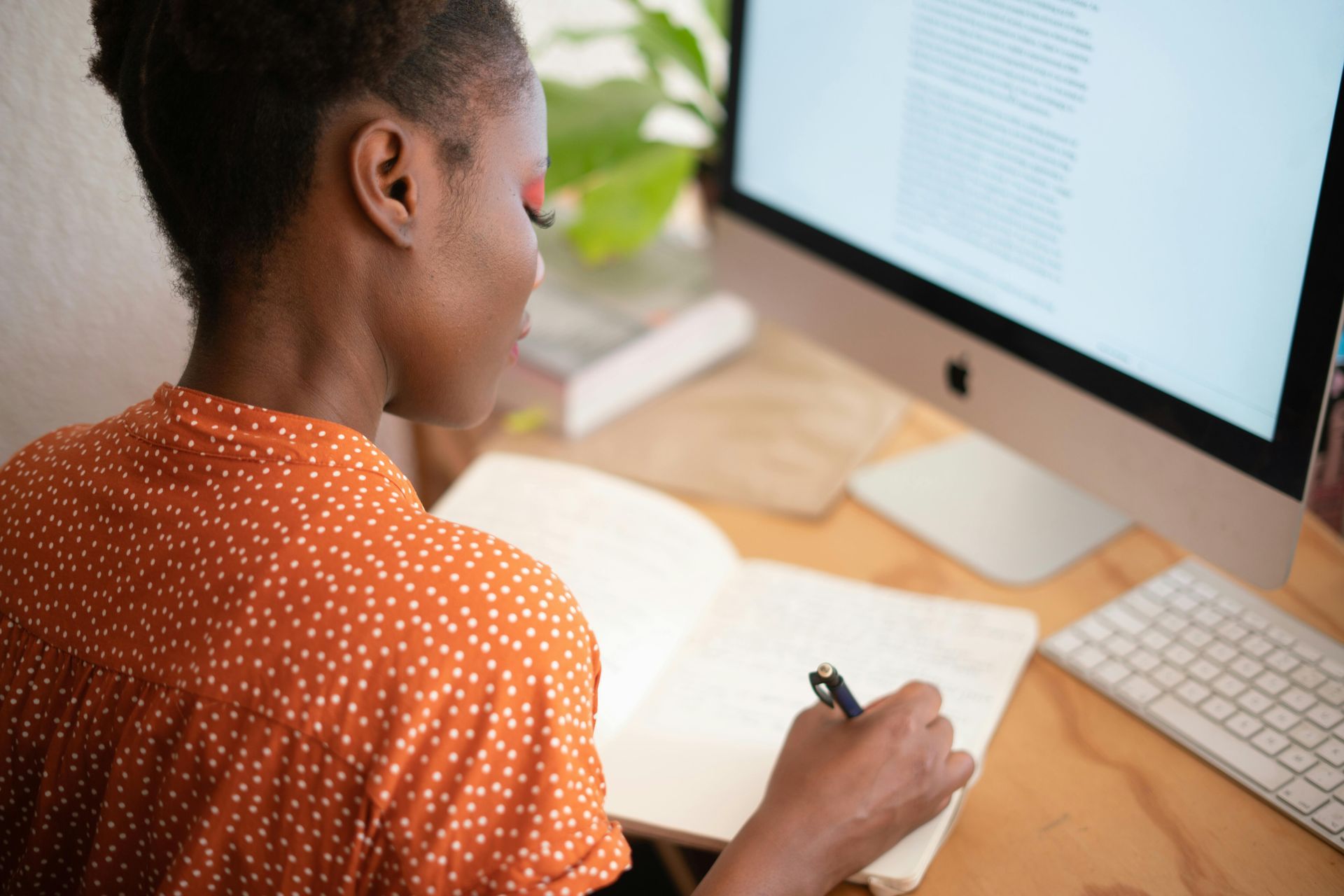
Working from home has become very common. Sometimes we can be permanently working from home, temporarily or as part of a hybrid arrangement. Even though we are not physically in our usually workplace, our home has now become our workplace and so this means that OHS Laws still apply, and all the legislated duty holders still have the same duties under The Act. The employer still has duties, including to ensure a safe workplace, mitigate OHS risks and to consult with their employees. The employee has a duty to take reasonable care for their own safety and to co-operate with safety measure put in place by their employer. The risk management process should still take place, even though you are working in your home environment, and we must seek to identify hazards as a starting point. Common hazards which you may find when you assess your own home work environment could include: Poor lighting Noise Poor temperature control Electrical hazards Psychosocial hazards (eg: job demands, poor role clarity, lack of support, online abuse, bullying, etc) Fatigue Domestic violence Trip and slip hazards Poor ergonomics The individual worker is particularly important in the hazard identification and risk management process in the work from home context. This is because they are often the only person who will be aware of the risks associated with their individual home environment. For more information on this topic, take a look at: https://www.safeworkaustralia.gov.au/safety-topic/managing-health-and-safety/working-home https://www.worksafe.vic.gov.au/officewise-working-home
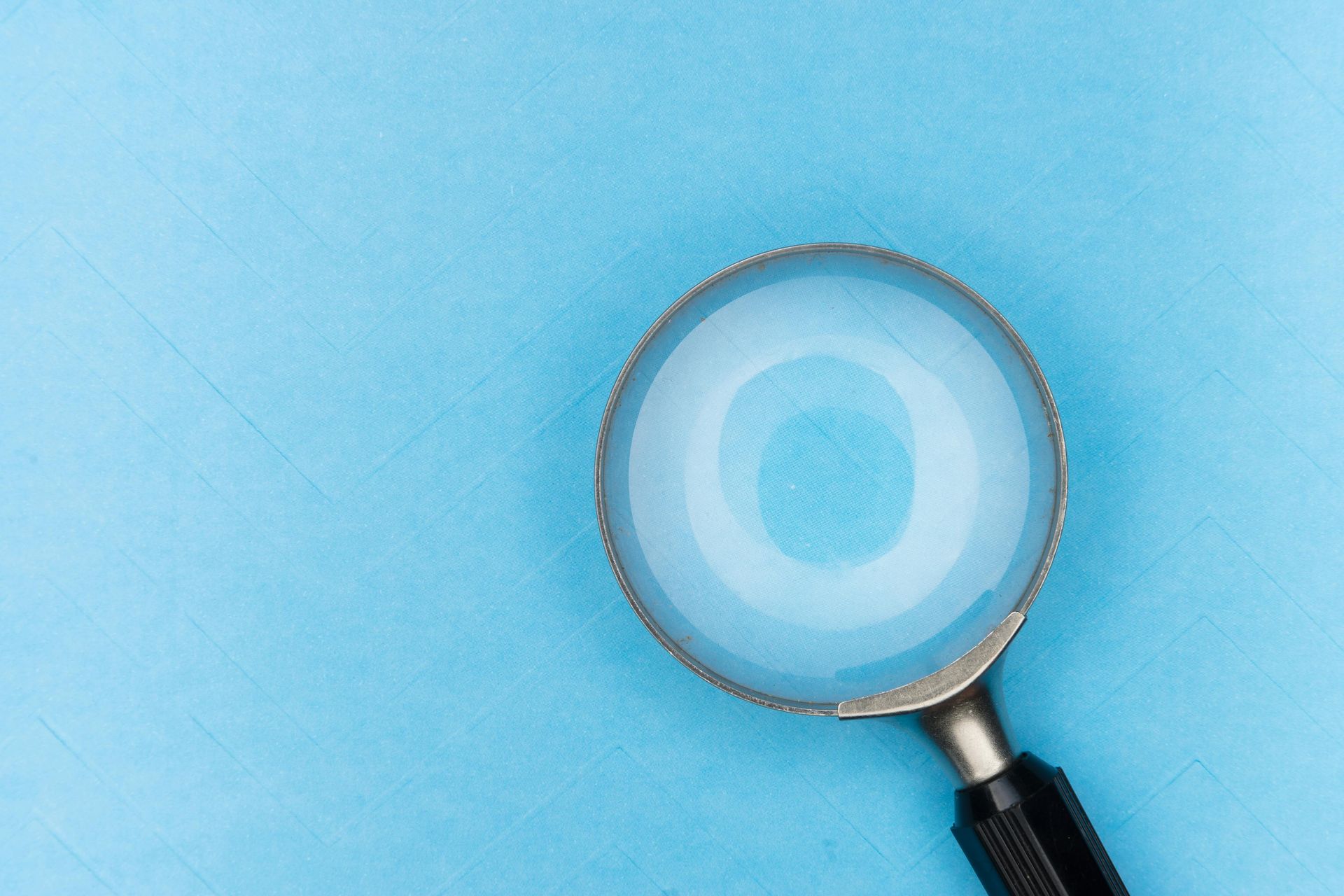
Hazard Hunts can be a great tool to use in workplace safety programs. They're a proactive strategy to identify and mitigate potential risks before incidents or injuries occur. But what exactly is a Hazard Hunt, and why is it so valuable? Hazard Hunts are regular, structured inspections aimed at identifying and eliminating potential risks in the workplace. Advantages: · Prevent Harm: proactively identification of potential hazards before they caused harm. Hazard hunts can prompt us to focus on specific risks that may have been overlooked. · Engagement of Employees: Talk to employees in the area. They often have valuable insights into hazards that may take time to be evident to outsiders. · Empowers Individuals: Creates an opportunity for individual employees to make a tangible difference to the safety of their workplace. This can really empower the individual and turn their mind to safety. · Collect information: Hazard hunts can prompt us to focus on specific risks that may have been overlooked · Increases awareness: The engagement of the workforce in this way can turn the mind to hazard identification in a way which can sharpens our ability to identify potential dangers and enhances our overall safety. · Positive influences safety culture: The involvement of the whole workforce, from management to the shop-floor, can foster an environment where safety becomes a shared responsibility. It can encourage a culture of vigilance and care. What next? It is integral that there is thorough follow-up after a hazard hunt takes place. This means utilising the risk matrix and hierarchy of control to prioritise the hazards which are dealt with first. Then you must move forward with mitigating the risk of the hazards coming to fruition. As always, this process must take place with meaningful consultation. If you don’t do this, then the benefits of the Hazard Hunt will be lost. The effort put into the hazard identification exercise must be matched by the dedication of the employer to make meaningful safety improvements. The Role of HSR’s: The people who are doing the work are the best placed to identify hazards in their work. They are also often the best people to come up with successful OHS solutions. HSR’s can encourage the use of hazard hunts and encourage their co-workers to actively participate. As always, HSR’s act as a conduit between the workers and the employer – working to improve safety in their role as employee representatives.
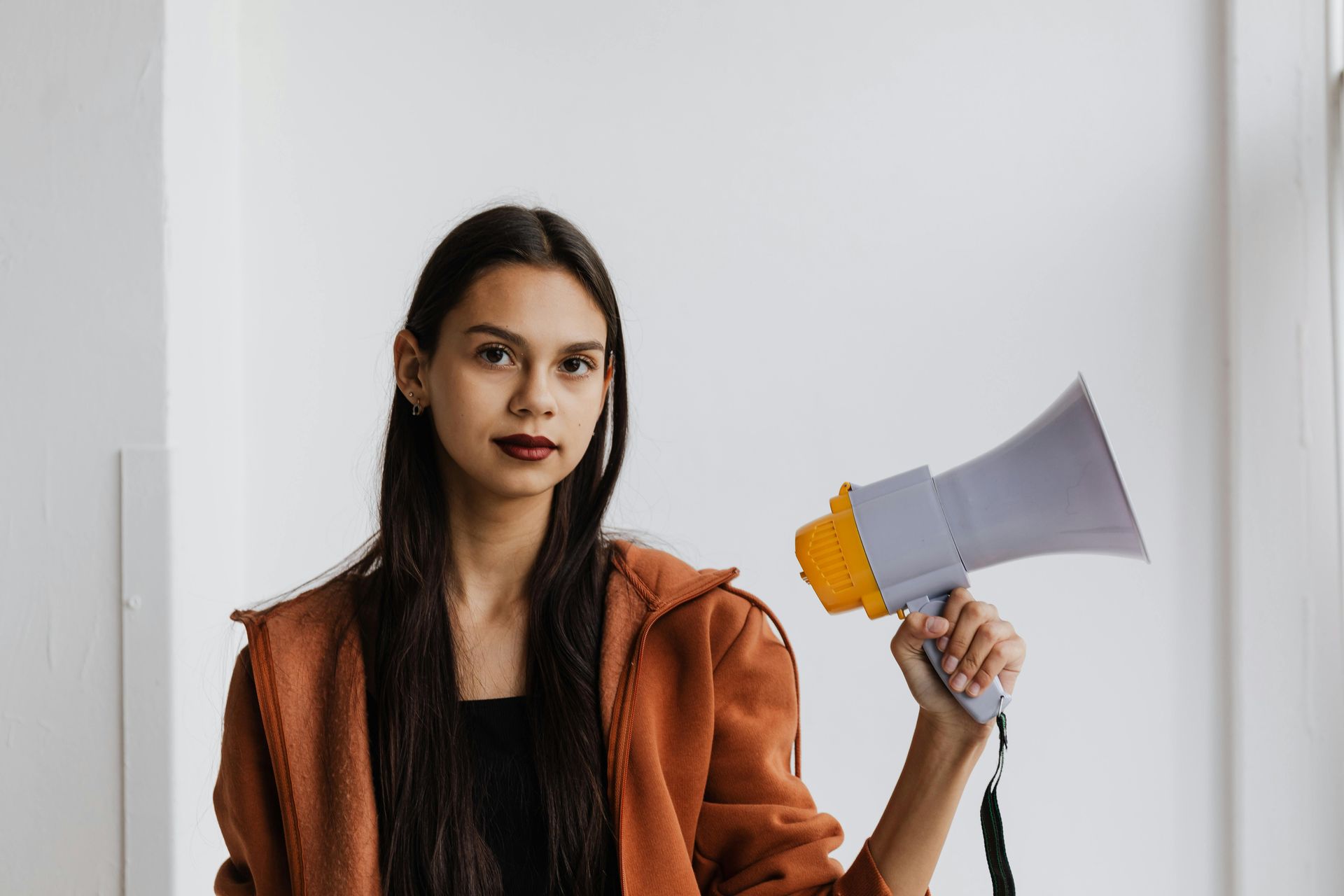
It is illegal to dismiss in employee or to discriminate against an employee if they have raised an OHS issue or concern . This is covered under Section 76 of The Occupational Health and Safety Act 2004 (The Act). This means that employees can and should raise concerns about both within and, if necessary, outside their organisation. What does discrimination mean this context? Discrimination against a person for raising an OHS issue can include: Dismissal Injury Alteration of an employee’s position, to their detriment Refusal of employment of a prospective employee or less favourable treatment of them Noting that the discrimination must have arisen due to the raising of an OHS concern as the dominant factor. The Act says that employees cannot be dismissed from employment or discriminated against if they: Are an HSR or deputy HSR (dHSR) Are a member of a Health and Safe Committee If, as an HSR, dHSR or HSC member, they exercise their powers If they are an employee who has assisted or given information to an Inspector, to WorkSafe, to a registered employee organisation (ARREO), to an HSR/ dHSR or an HSC member If they are a prospective employee who raises or has raised an issue or concern about health and safety to an Inspector, to WorkSafe, to a registered employee organisation (ARREO), to an HSR/ dHSR or an HSC member In short, any employee or prospective employee is protected under this part of The Act. Further strengthening the law is the fact that the accused bears the onus of proof (Section 77 of the OHS Act) . This means that the employer is considered to have broken the law unless they can prove that they did not dismiss or discriminate on the basis of the person raising a health and safety issue - with this being the dominant issue. If found guilty, the offence carries significant penalties under The Act . The intent of the legislation is to ensure that employees can SPEAK UP about health and safety issues, without fear of retribution. Remember, The Law states that you can speak up and protects you against discrimination. For more information on this topic: Discrimination for OHS reasons - OHS Reps Discrimination on health and safety grounds | WorkSafe Victoria If you need help, don’t hesitate to call BeSafe on 0467 002 060 or email us on admin@besafevictoria.com.au
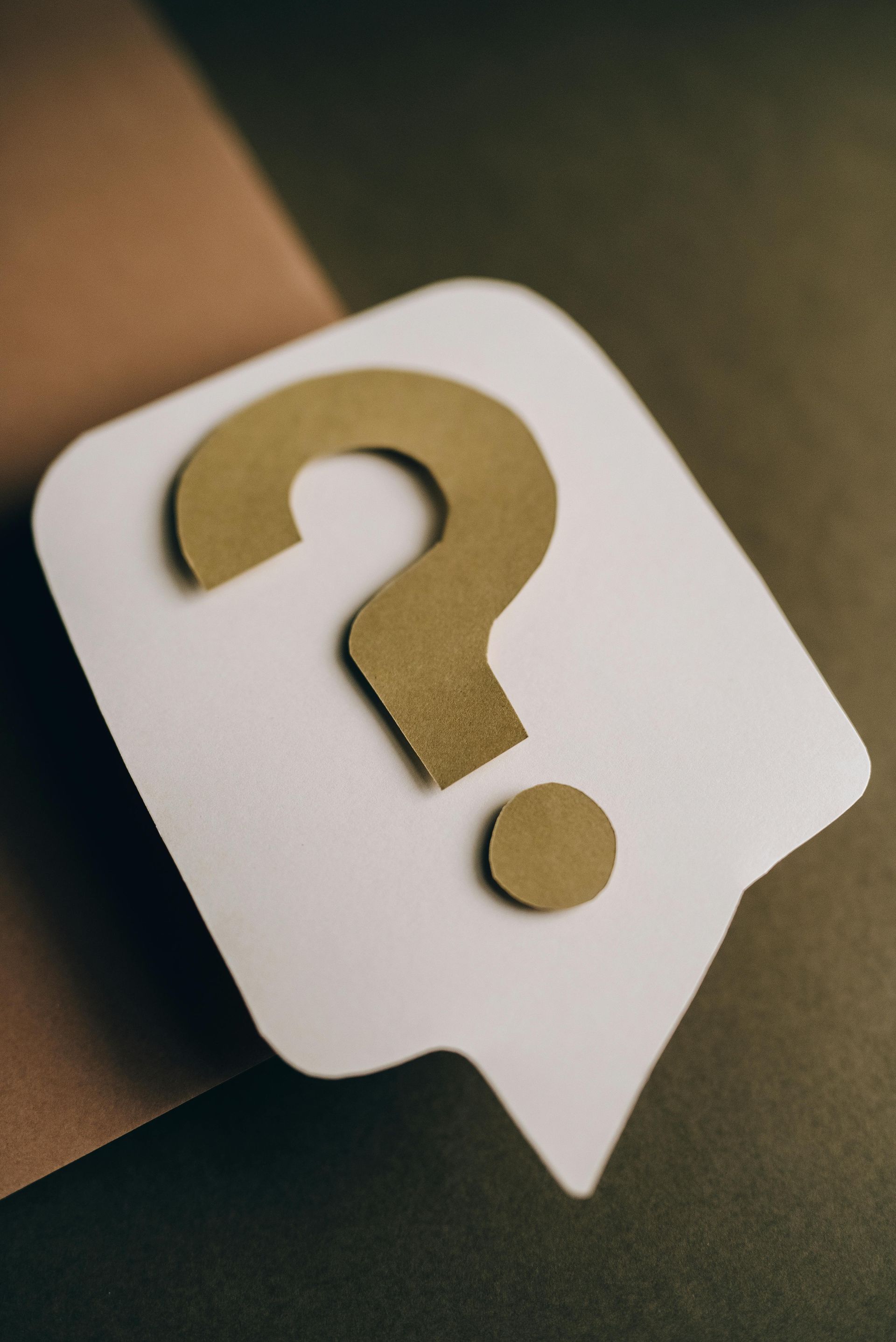
The Victorian Occupational Health and Safety Act 2004 requires that the employer has a duty to ensure a healthy and safe workplace. This duty must be met as far as reasonably practicable. But what does this actually mean? The following must be considered when determining what is reasonably practicable: (according to section 20(2) of The Act): (a) The likelihood the hazard or risk concerned eventuating; (b) The degree of harm that would result if the hazard eventuated; (c) What the person concerned knows, or ought to reasonably know, about the hazard or risk; (d) The availability and suitability of ways to eliminate or reduce the hazard or risk; (e) The cost of eliminating or reducing the hazard or risk. This is often an area of confusion – primarily because the test for what is ‘reasonably practicable’ is in fact objective. When we consider this, it is best to look to WorkSafe for guidance. WorkSafe Victoria provides some clarification in their Position Statement on the matter: ‘a person is to be judged by the standard of behaviour expected of a reasonable person in the duty-holder’s position who is required to comply with the same duty and is: • Committed to providing the highest level of protection for people against risks to their health and safety. • Proactive in taking measures to protect the health and safety of people.’ - WorkSafe position statement - reasonably practicable There must be a weighing up of each of the 5 points listed under section 20(2) of The Act (above), but with a clear presumption in favour of safety. This means that the likelihood of harm occurring, and the seriousness of the potential outcome, must be the most important factor. The cost must be considered to be the least important factor when deciding what is reasonably practicable. ‘If the degree of harm is significant, e.g. death or serious injury is highly likely, then it is extremely unlikely that the cost of eliminating or reducing the risk would ever be so disproportionate to the risk to justify a decision not to implement an available and suitable control measure.’ - WorkSafe position statement - reasonably practicable When considering what the person concerned should reasonably know about eliminating the hazard, the state of knowledge regarding hazards and controls must be considered and this must be applied in line with the ranking under the hierarchy of control. The definition of what is ‘reasonably practicable’ is often one which causes some contention. It is important to go back to the WorkSafe position statement to make sure that you are making decisions in line with the intentions of The Act . Of course, it is always required that the highest level of protection from a hazard is provided in order to ensure a safe workplace. To read more about this: How WorkSafe applies the law in relation to Reasonably Practicable | WorkSafe Victoria
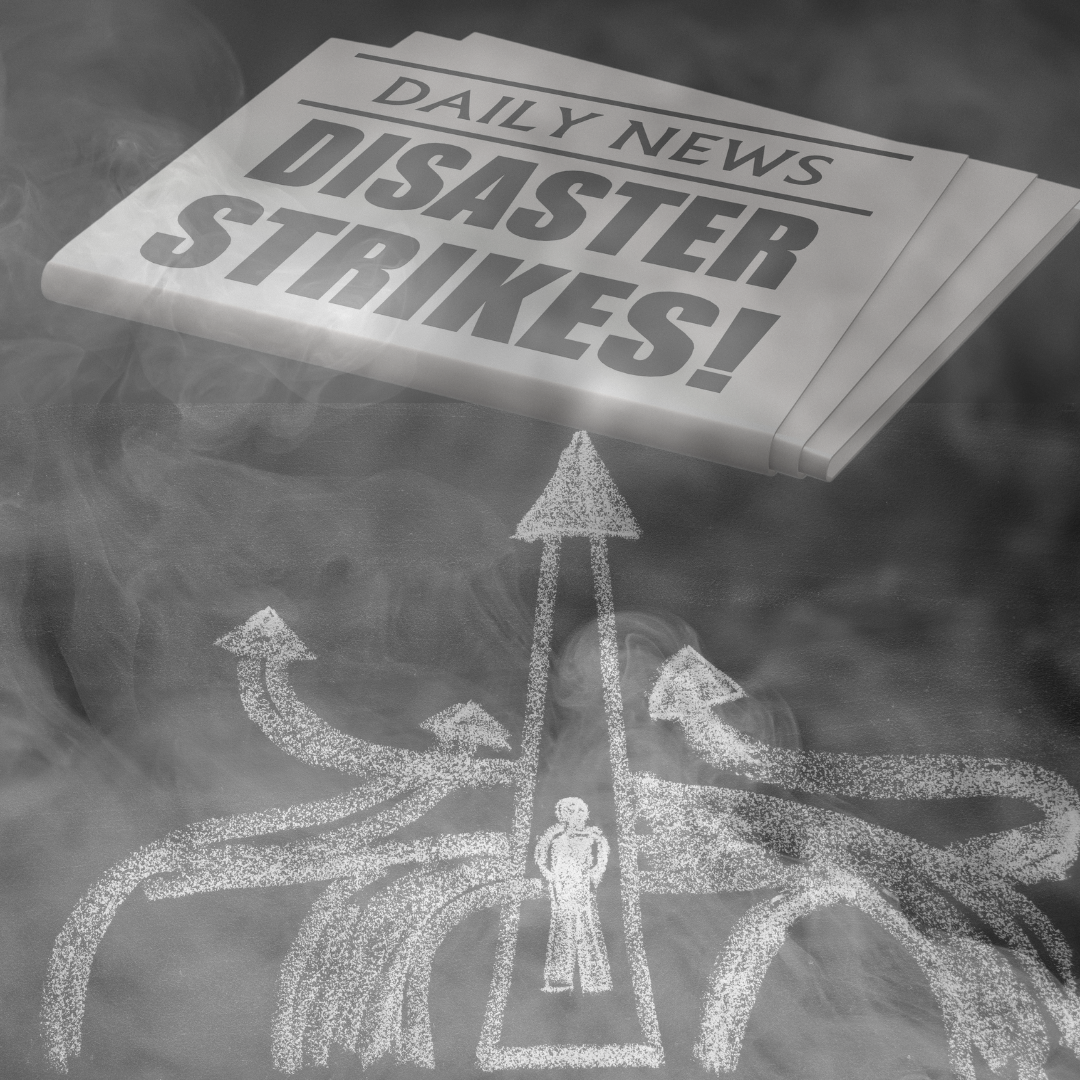
Michael Quinlan’s book ‘Ten Pathways to Death and Disaster’ includes a review of fatal mine incidents. What he found was that the each disaster was preceded by common causes. There are 10 recurring reasons why disasters happen in the workplace. He describes 10 pathways: Pathway 1: engineering, design and maintenance flaws Pathway 2: failure to heed warning signs Pathway 3: flaws in risk assessment Pathway 4: flaws in management systems Pathway 5: flaws in system auditing Pathway 6: economic or reward pressures compromising safety Pathway 7: failures in regulatory oversight Pathway 8: worker or supervisor concerns that were ignored Pathway 9: poor worker or management communication and trust Pathway 10: flaws in emergency and rescue procedures In most cases, at least 3 of these pathways will be present. However, some cases will have features of all 10. The 10 pathways don’t just apply to mine incidents – they have been applied across other high hazard workplaces and have found to be equally relevant across industries. Ultimately, this shows that death and disaster in the workplace is predictable and preventable – so why do major industries continue to kill in the same old ways? If the 10 Pathways approach defines the issues which lead to major incidents, then why aren’t these being used to prevent such events? In other jurisdictions, the 10 Pathways Theory has been used to inform prevention. Perhaps it is something which regulators, employers, and also HSR’s could consider when thinking about how to prevent death and injury in Victorian Workplaces. Ten Pathways to Death and Disaster eBook - The Federation Press
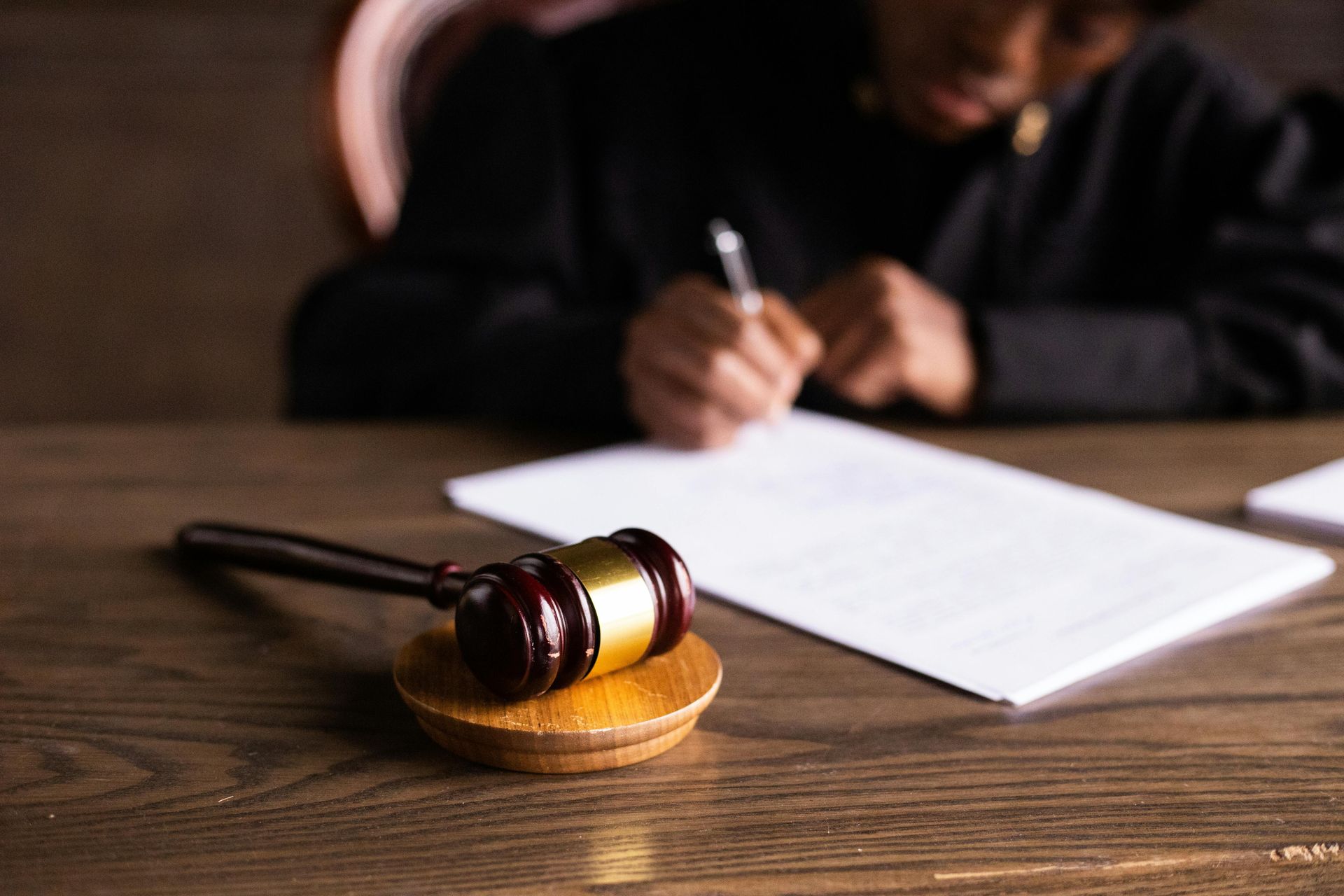
The Sentencing Advisory Council (SAC) has recently reviewed the sentencing of breaches of the Victorian Occupational Health and Safety Act 2004. Through their review, they discovered that there is a need to change sentencing practices in Victoria. They found that punishments were often not appropriate and not in line with community expectations, and that sentencing orders such as adverse publicity orders and health and safety orders are being underutilised. In addition, many fines are going unpaid. Following a period of review and consultation, the SAC has recently published its’ report into the sentencing of OHS offences in Victoria. The SAC have made 12 recommendations, divided into 3 categories: 1. Victim related recommendations – relating to victim impact statements and restorative justice. 2. Sentencing Practices – relating to enforceable undertakings/ health and safety orders, adverse publicity orders, increasing penalties for OHS breaches and the inclusion of Sentencing Guidelines in the OHS Act. 3. Fine Payment – relating to fines being paid to WorkSafe, reviews of fines outstanding, declared director notices and successor liability. The recommendation to introduce Sentencing Guidelines would follow the example of the UK, where they already exist. However, Victoria will represent a world first if these guidelines are introduced as recommended – in legislation. If implemented, this suite of changes could lead to much improved Occupational Health and Safety outcomes for Victorian workplaces. Interested in finding out more? Take a look at: Sentencing Advisory Council Recommends Major Changes to Sentencing of Workplace Safety Offences | Sentencing Council
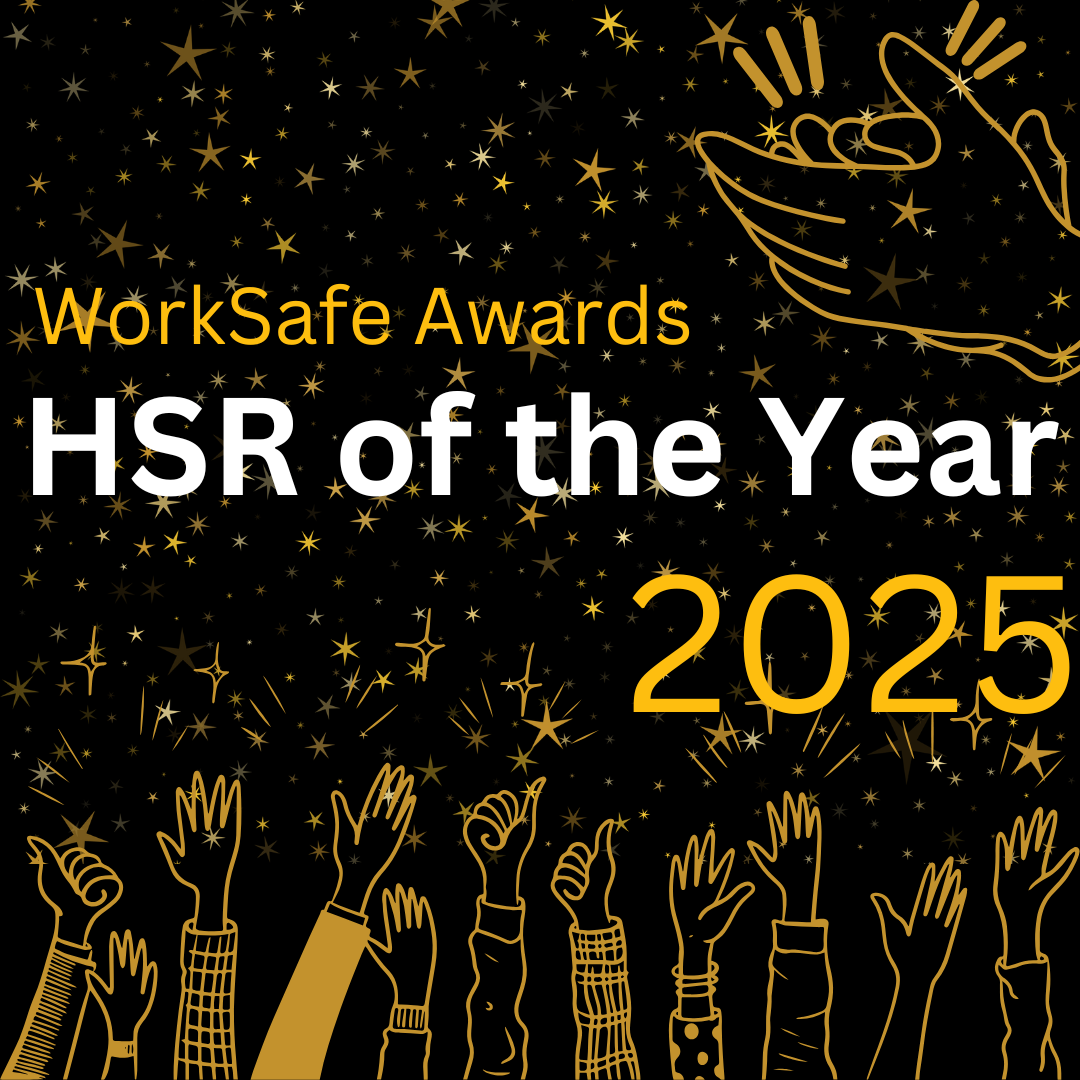
The Annual WorkSafe Awards night was held last week. As always, the highlight was the Health and Safety Representative of The Year Category. We all know what amazing work HSR’s do every day across Victoria to keep workplaces safe and it was great to see a handful of them called out for their great work. The finalists for 2025 were: Barry McKenna – from United Petroleum Hastings Terminal Cameron Barber – from Delcon Civil Cameron Middleton-Else – from Wodonga Middle Years College Danny Humphrey – from Qenos Mick Puche – from Glenelg Shire Council Sue Healey & Melissa Courts – form Echuca Regional Health Each of these HSRs was nominated for the award by someone who had seen their outstanding commitment to health and safety. They each had a particular challenge to deal with at work and had persevered until they got the right safety outcomes for their co-workers. This year, the winner of the award was Mick Puche. As a plant operator and with a previous workplace injury where he lost a finger at work, he is a dedicated advocate for health and safety. Find out more about Mick here: HSR of the Year - Mick Puche | Glenelg Shire Council Another award on the night was the Worker Return to Work Achievement. The finalists were: Matthew Manley – from Kinross Farms Nicholas Johansen – from Mainstream Aquaculture Steel Anderson – Steel Anderson Carpentry The award went to Matthew Manley. Find out more about Matthew here: Worker Return to Work - Matthew Manley | Kinross Farms All three of these workers had suffered severe injuries in their workplace. It was such an important reminder of how important safety is. This award focused on their return to work, but we all know that there are many workers who are so severely injured, physically and mentally, that they will never make it back to work. The work of all HSRs is targeted at preventing such terrible incidents – so that no one has to endure what these three workers, and countless others, experience. HSR’s, as the workers' representatives, are integral to genuine and meaningful consultation in the workplace. Every workplace should have legally elected and trained HSR’s, with safety structures in place. One can’t help but wonder how much safer the workers of Victoria would be if every workplace had HSR’s! If you need help with setting up safety structures in your workplace, running HSR elections, or HSR training and support – don’t hesitate to get in touch: HSR Training and support | BeSafe | Regional Victoria
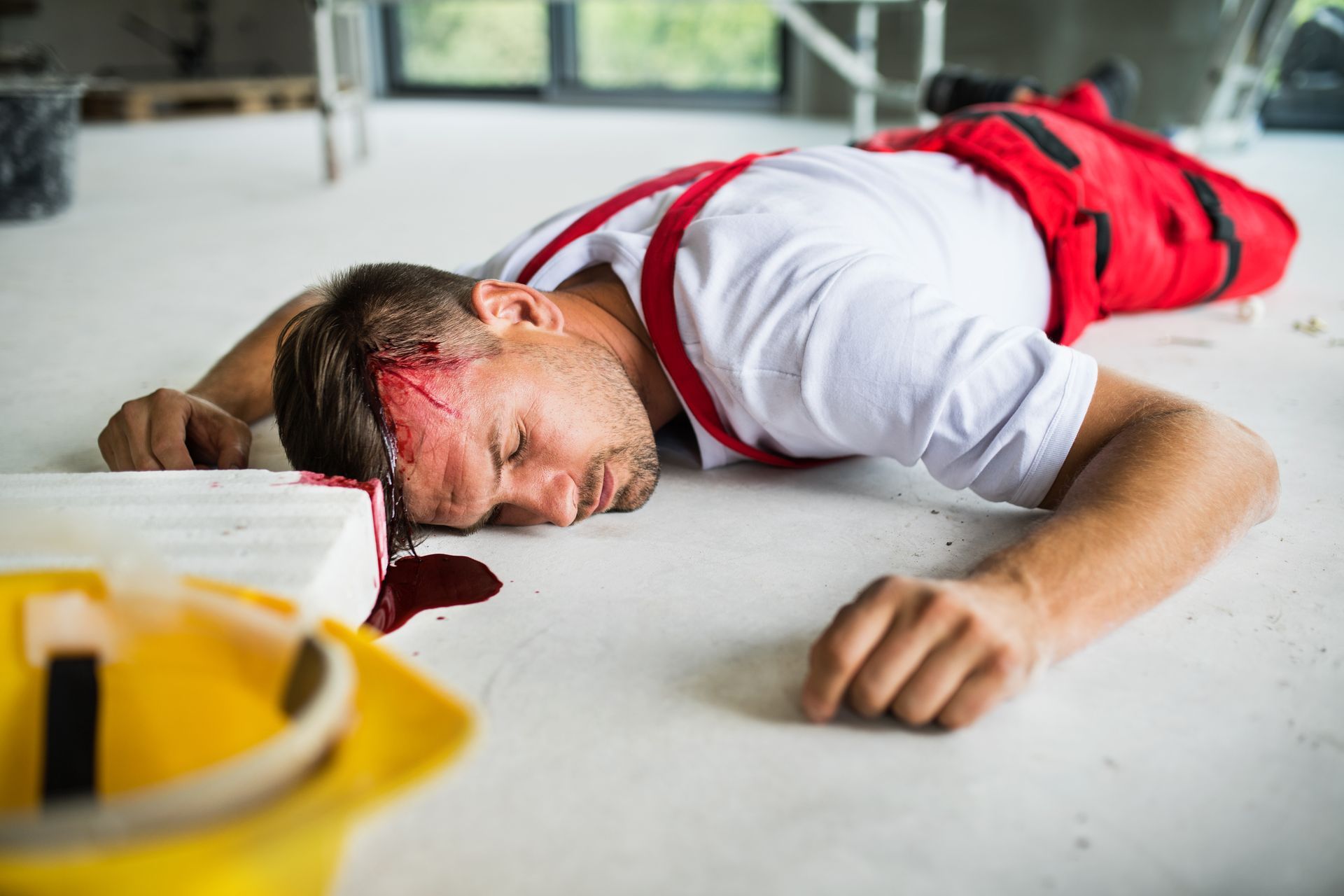
Falls are still a leading cause of injury and death, and they have been for a very long time. So why aren't we better at eliminating the risk of falls in the workplace? Falls from heights can occur due to various hazards. These includes scaffolds, ladders, roofs, trucks, holes, pits, shafts, trenches, and mezzanines. in addition, we can at a risk of fall when working on machinery, on slippery or unstable surfaces, on sloping surfaces, or near an unprotected edge. Don’t forget that falls risks can include a fall from an elevated position or a fall into a pit. Even a fall from a relatively low height can cause very serious injuries, if not death. As per the requirements of the Occupational Health and Safety Act 2004 - all fall related hazards must be controlled in the workplace. In addition, when there is the risk of a fall of 2 metres or more, then Part 3.3 of the OHS Regulations comes into play. Employers must control the risk for falls: 1. You must ELIMINATE the risk if at all possible – by working on the ground or on a solid construction If this can’t be done, then you could use the following control measures in order of priority: 2. Passive fall prevention device – guarding, railing or scaffolding 3. A work positioning system – so that workers are within a safe area 4. Fa l l arrest systems – safety harness, safety net or catch platform 5. Use of ladders, or administrative controls – safe work procedures and signage In addition – you must establish emergency procedures , which includes how you will rescue a fallen worker and provide first aid. Employers must also provide training and supervision of workers. As always, you must review the controls that are put in place: if things change if the HSR requests it as part of your obligations to monitor health and safety Don’t forget there is also a duty to consult with employees and HSR’s when identifying hazards and deciding what control measures to use. For more information, take a look at: A guide to falls prevention | WorkSafe Victoria As always, BeSafe is available for help and support HSR Training and support | BeSafe | Regional Victoria
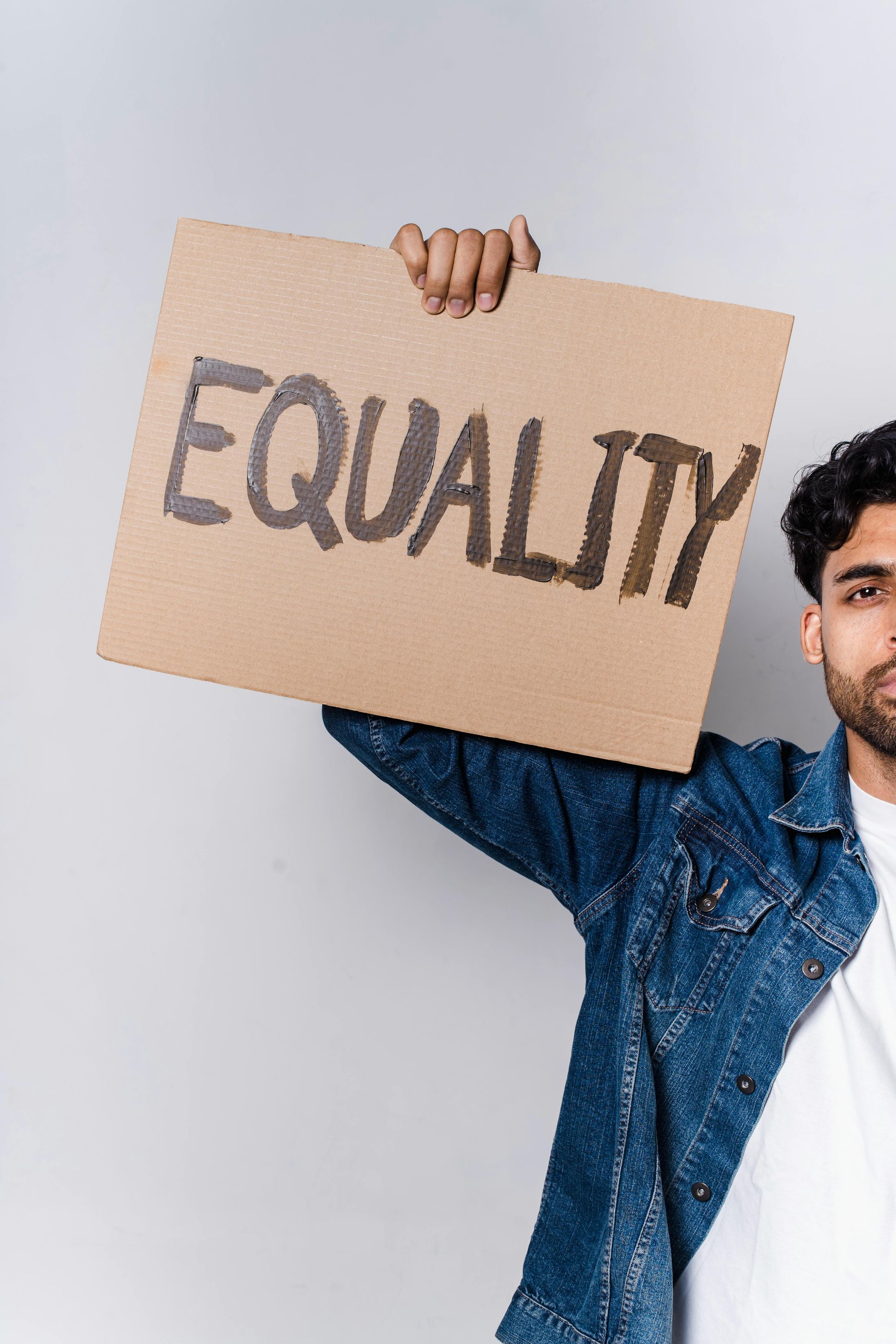
Is Work Safety a Social Justice Issue? The 20 th February has been named The World Day for Social Justice. But is Work Safety a Social Justice Issue? When certain groups face disproportionate risks due to factors like systemic inequalities, unsafe working conditions become a social justice concern. For example, certain demographics (such as racial minorities or low-income workers) often experience higher rates of workplace injuries and illnesses due to systemic disadvantages. Poor work safety practices can lead to significant health disparities, further emphasizing the social justice aspect. Unequal power dynamics between employers and employees can prevent workers from raising concerns about safety issues, perpetuating unsafe conditions. The right to a safe workplace is a fundamental human right – but not all workers are treated equitably in the protection of their health and wellbeing. To read more about the World Day For Social Justice, visit World Day of Social Justice | United Nations
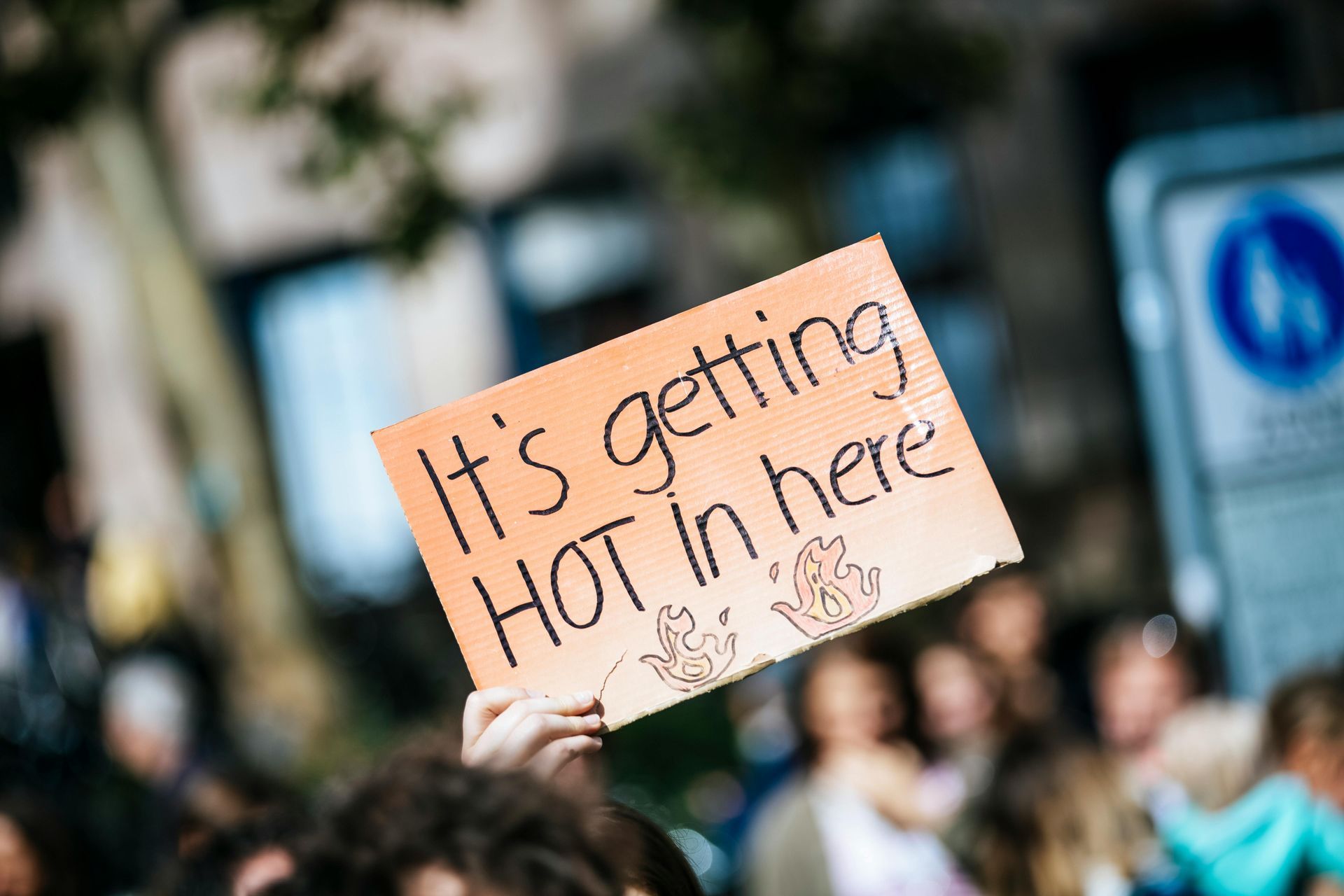
When there is a heatwave, it can introduce temperatures which are a new hazard not normally experienced in a workplace. As always, the employer must eliminate or minimise risks as far as reasonably practicable. That means that when conditions change, it’s time to do a risk assessment and put new controls in place. There is no single ‘stop work’ temperature. Various factors need to be taken into account which include humidity, air flow and the type of work being performed. Heatwave conditions create a work-related risk in the form of heat stress and fatigue. But there are various ways to control the risk. Things to consider may include: working in the cooler part of the day moving work to a different location limiting tasks which require higher physical effort during the hotter period changing work expectations and allowing workers to self-pace their work ensuring access to cool water - and rehydration electrolytes if required providing shade air conditioning or fans if possible ensuring workers are not working in isolation ensuring supervision is in place taking into account more vulnerable workers - for example those who may be young, pregnant, suffer an illness, etc training workers to ensure they understand the risk and how to recognise symptoms ensure first aid and medical assistance is available Remember that the risk posed by heat is not just limited to outdoor workers. Indoor workers can be exposed to unsafe working conditions too - including high temperatures, thermal radiation and humidity. As with all hazards - when considering what control to put in place, the usual hierarchy of control should be used – with elimination being considered first. If this can’t be done, then consider substitution, followed by isolation/ engineering controls, then administrative controls and finally PPE as the last option. As always, the effectiveness of the controls should be monitored and reviewed. Health and Safety Representatives (HSRs)s can be proactive in this area by consulting with the employer and attempting to resolve the risk. If there is an immediate risk to health and safety, then they can direct a cease work. HSRs play an important role in ensuring a safe workplace – and this includes during heatwave conditions.
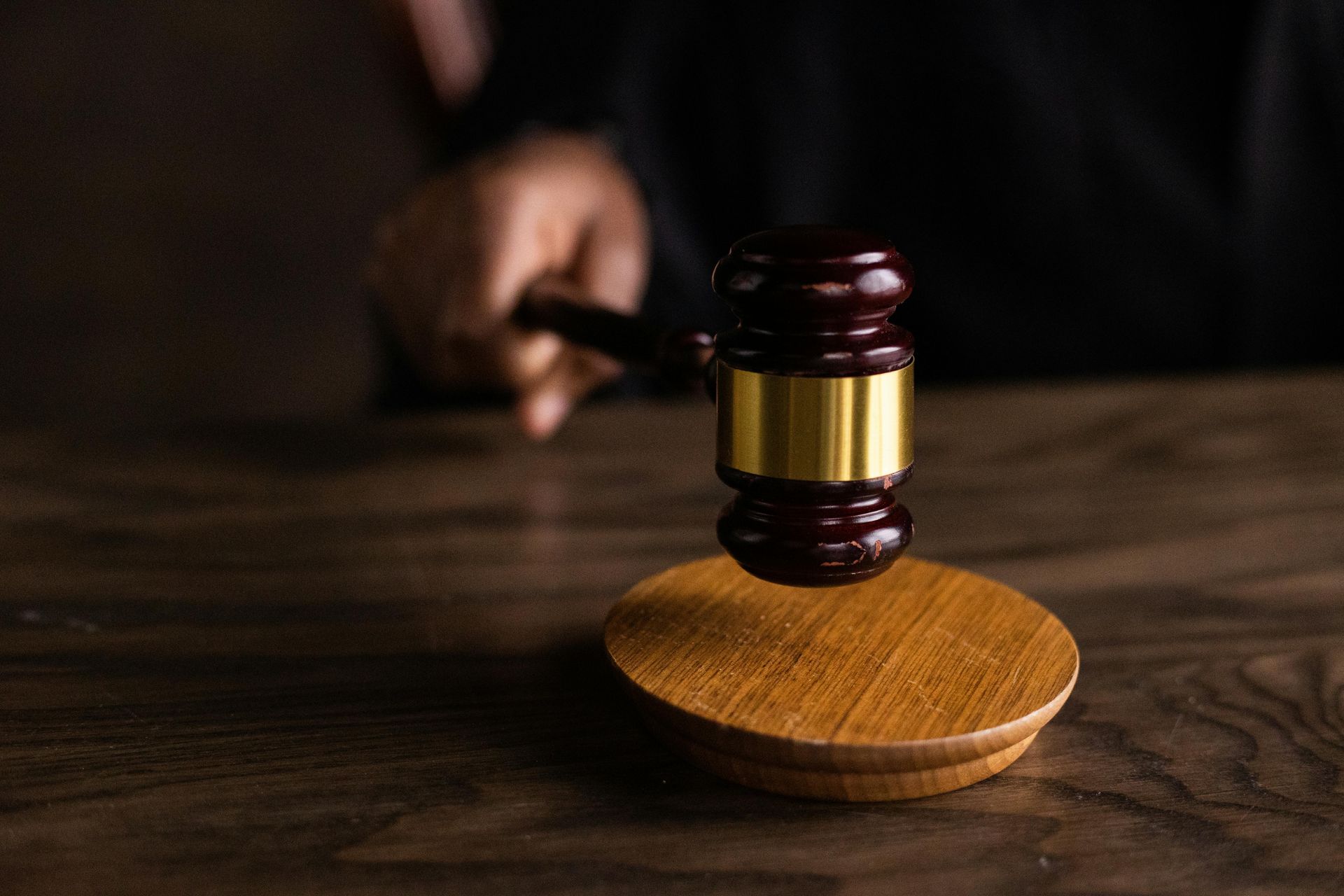
Section 21 of the Victorian Occupational Health and Safety Act 2004 - Duties of employers to employees dictates that employers must provide ‘supervision to employees as is necessary to enable those persons to perform their work in a way that is safe and without risks to health’. Failure to do so is an indictable offence. Who must be supervised? It is the legal responsibility of the employer to provide supervision in order to ensure workers are following safety instructions and working safely – but who does this include? The legal obligation to supervise extends to any person to which the employer has a duty to provide a safe workplace. This includes: - Direct workers – full time, part time, or casual - Labour hire workers - Independent contractors - Employees of independent contractors Who can be a supervisor? In order to effectively supervise workers, the designated supervisor must be competent and trained to carry out this role. Before undertaking a supervisory role, the person should: - Be trained in OHS legislation - Be trained in workplace policies and procedures - Understand all the obligations under OHS laws - Understand what the workers’ experience and skills are - Understand the tasks being carried out and what safety requirements apply to these tasks - Understand the level of training required for workers to safely undertake these tasks - Have authority to make decisions and act on OHS issues immediately - Be resourced to carry out their OHS supervisor obligations effectively and meaningfully The supervisor should not only receive training before becoming a supervisor but should also attend regular refresher training. Do you want to know more about supervision and whether your workplace is meeting its’ legal obligations? Take a look at Safety supervision: Creating an environment for effective supervision | WorkSafe Victoria
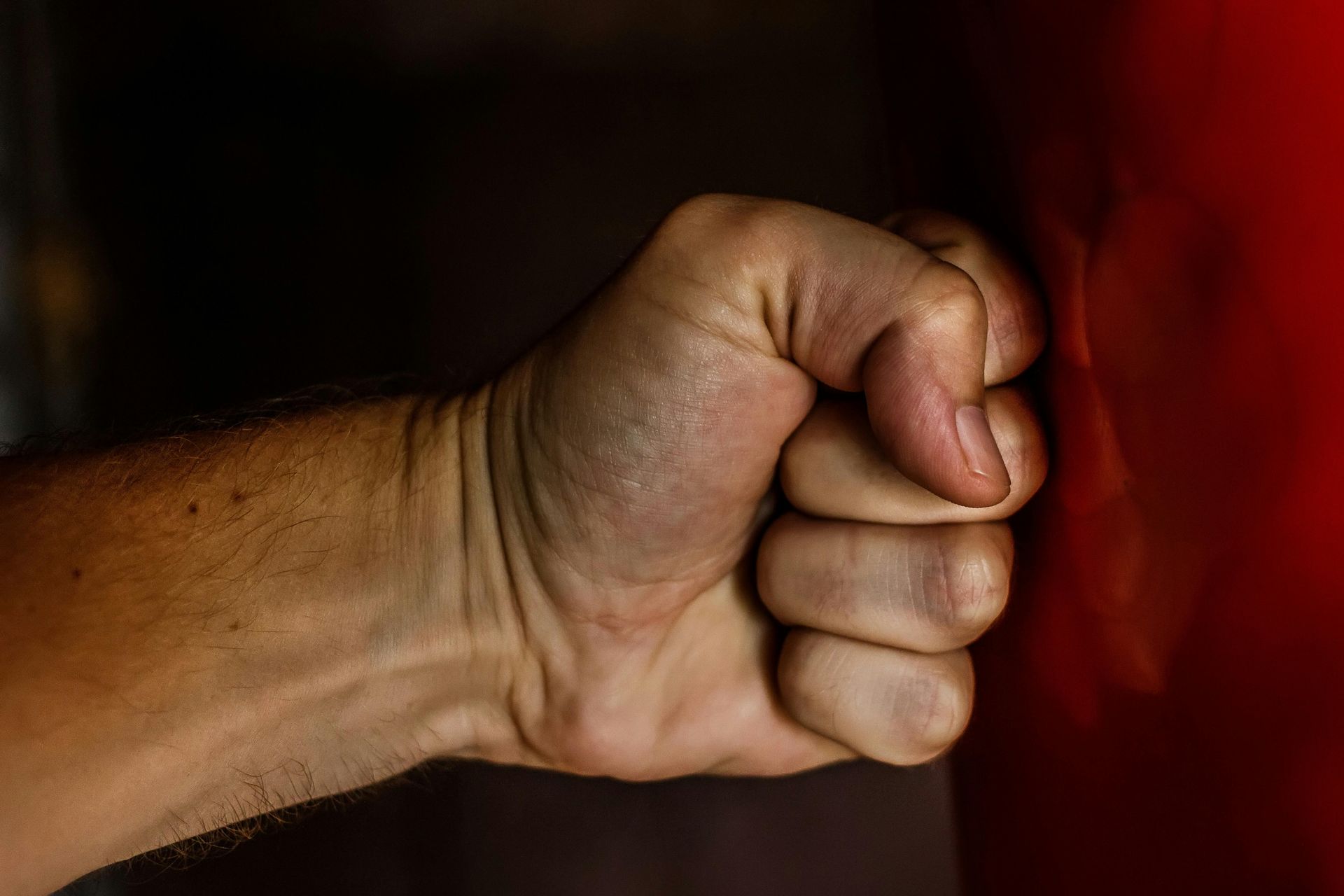
Occupational Violence and Aggression. Occupational violence and aggression (OVA) is when a person is abused, threatened or assaulted in a situation which is related to their work. It may come from internally (co-workers) or externally (clients, patients, customers or the public). It may include verbal abuse, physical intimidation, physical violence, or threats of violence. It can occur in person, over the phone or even online. There is a broad spectrum of severity, but all can impact the workers mental and physical safety. Violence at work is a major health and safety issue and is particularly prevalent in some industries but can occur in any industry. What do you do about it? Like with any other hazard, the employer has a duty und the Victorian Occupational Health and Safety Act (2004) to provide and maintain for employees, as far as is practicable, a working environment that is safe and without risks to health. OVA should be treated like any other OHS hazard and includes looking at and addressing root causes and contributing factors. It can be prevented in many cases and can be minimised in others. The principles of risk management apply to OVA too: Identify the hazards Assess the risks Implement controls Review the effectiveness of the controls Consultation must occur throughout the process Make sure that all incidents are being reported. If an incident does occur, then the worker must be supported, but we must not stop here. We must learn from the failure by investigating the incident and working to prevent it from happening again. When addressing the risk of OVA in a workplace, think about systems and controls which may be effective in the context of your industry and workplace. These might include: Security – this may include security guards, CCTV and duress alarms. Hazard identification and risk assessment procedures specifically for OV risks – this may involve assessing any OV risk posed by a patient, client, customer, etc. For example in historical records, or by observing their behaviour on entry to the workplace. Systems of record-keeping which include a process for recording around the risk of OV. Reporting processes for incidents of OV. Processes for following up on incident reports – including investigations to explore the root cause, with actions taken to prevent recurrence. Workplace design – for example screens, eliminating blind corners and isolated locations, lighting, etc. Protocols to eliminate known high-risk situations eg: sole charge, night-time, isolation, etc. Education and training – eg: de-escalation technique training, processes for calling for back-up, etc. Ensure that the workers know what the safety protocols are and how to use them. Policies and procedures which are practical and apply to the context of the workplace. Provide post-incident support – immediate follow up and support tailored to the individual’s needs. Actively promote a culture which empowers staff to expect a safe workplace. When working towards tackling violence and aggression as an OHS issue, it is integral that the employer and the employees believe that they have the right to expect a physically and mentally safe workplace. This means promoting a culture in the workplace that does not accept violence and aggression. Violence and aggression are never just ‘just part of the job’.
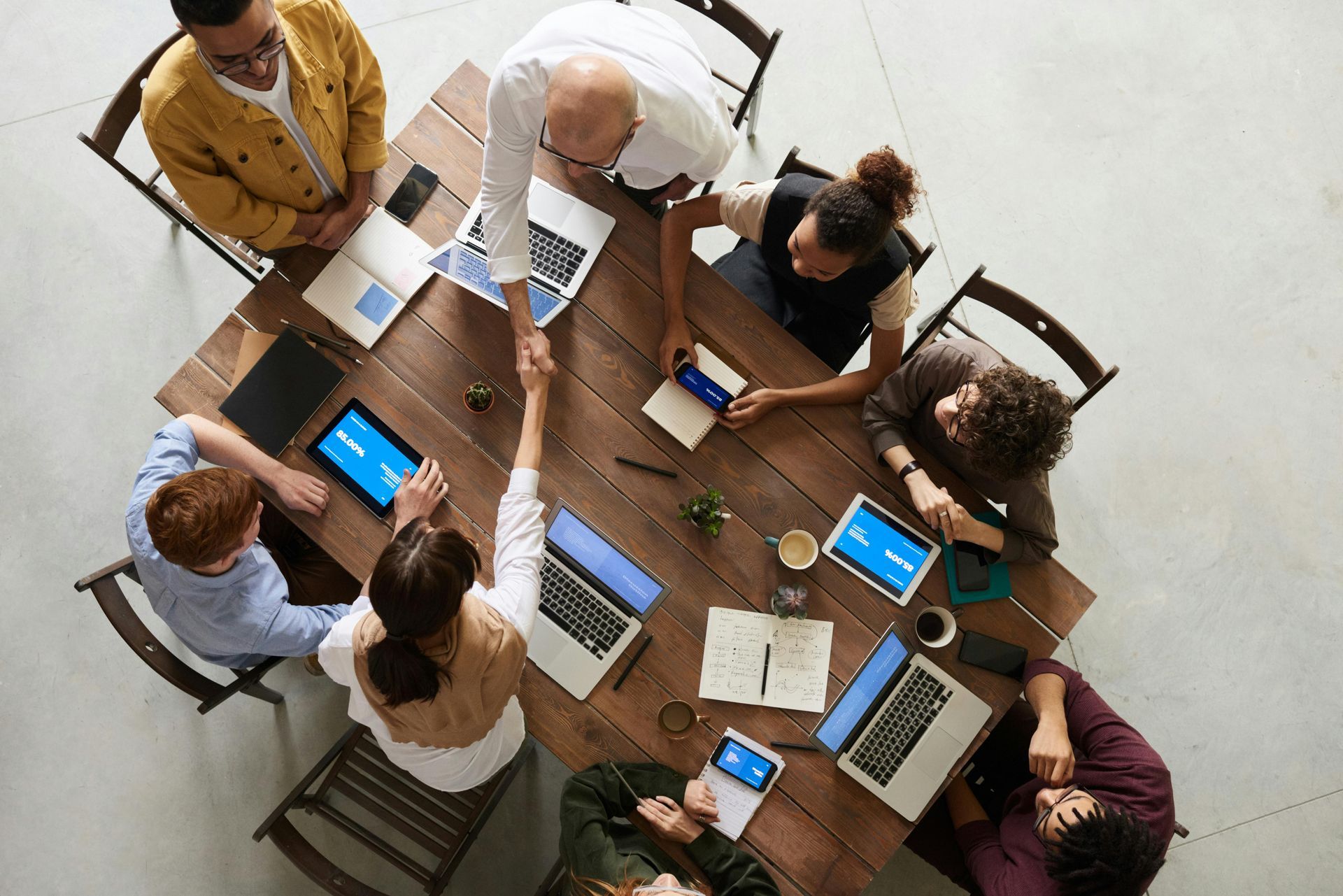
Workplace consultation is a critical aspect of maintaining a healthy, safe, and productive work environment. The principles of consultation are enshrined in legislation, ensuring that both employers and employees engage in meaningful dialogue about workplace safety. Workers have the right to be consulted on any matters which could impact their health and safety. In addition, those completing the work, have extremely important input and valuable insight to share. Not only must the employer consult with the workers, but the employer can really benefit from help and input from those doing the work themselves. When? The workers and/or the HSRs in a workplace must be consulted: During hazard and risk identification processes When making decisions around risk control, facilities and procedures When forming Health and Safety Committees When changes are being made in the workplace, including to plant, substances or conditions When changes are proposed which would alter the way in which work is done Who? You must be consulted if you are a worker and your health and safety is affected or may be affected. This may be via the HSR who represents your work group. How? Consultation must include providing information about the matter, allowing time to review the information, then having the opportunity to respond with your views. Your employer must then consider your views before making a decision. Communication in relation to this must be carried out in a way which is accessible. This may mean communicating both verbally and in written form, as well as in languages other than English, depending on the needs of the workers. Why Consultation Matters. Consultation in the workplace involves seeking and considering employees' views when making decisions that affect them. This process is not just a legal requirement but also a best practice that can lead to numerous benefits: Improved decision-making and better outcomes Greater employee engagement More successful implementation of changes Better health and safety! Consultation is crucial for identifying and mitigating workplace hazards. Employees are often the first to notice potential risks, and their input helps build safer work environments. Workplace consultation is more than a legal obligation; it is a pathway to a more collaborative, safe, and productive work environment.
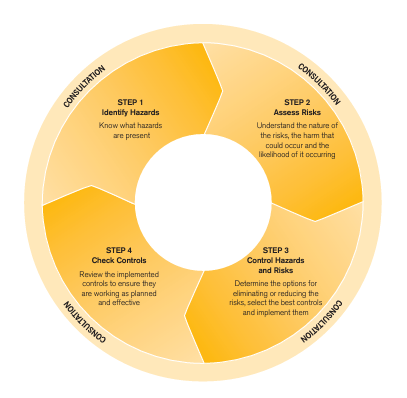
In any workplace, ensuring the safety and well-being of employees is paramount. One of the most effective ways to achieve this is through a comprehensive risk assessment process. This process helps identify potential hazards, evaluate the risks associated with them, and implement measures to control or eliminate these risks. This is a continuous and ongoing process, as shown in the diagram above. Step 1: Identify Hazards The first step in the risk assessment process is to identify potential hazards in the workplace. Hazards can be anything that may cause harm, such as: Mechanical Hazards : Machinery, equipment or other items that could cause physical or impact harm. Chemical and Biological Hazards : Harmful substances or chemicals, including pathogens. Source of Energy : Such as electricity, heat, noise, light and radiation. Body Stressing or Impact Hazards : Activities which cause stress to the body. For example poor workstation design, repetitive movements, manual handling tasks and slip and trip hazards. Gravity: Activities where a person can fall or an object can fall on people. Psychosocial Hazards : Events, circumstances or systems of work which can lead to psychological illness, including stress, harassment, workplace violence and fatigue. Step 2: Assess the Risks Once hazards are identified, the next step is to assess the risks associated with each hazard. This involves evaluating the likelihood of the hazard causing harm and the severity of the potential consequences. Consider the following factors: Frequency of Exposure : How often employees are exposed to the hazard. Duration of Exposure : How long employees are exposed to the hazard. Severity of Potential Harm : The potential impact on health and safety. It can be useful to use the Likelihood Consequence Table to help with assessing the risks (see below). Step 2: Implement Control Measures After assessing the risks, it’s crucial to implement control measures to mitigate or eliminate the risks. Control measures can be categorized into: Elimination : Removing the hazard entirely from the workplace. Substitution : Replacing the hazard with a less dangerous one. Engineering Controls : Isolating people from the hazard through physical changes to the workplace. Administrative Controls : Changing work procedures or policies to reduce exposure to the hazard. Personal Protective Equipment (PPE) : Providing employees with protective gear to minimize exposure. It can be useful to use the Hierarchy of Control diagram to help you during this process (see below). Remember that you must always use the highest possible level of control possible. Step 4: Monitor and Review Risk assessment is not a one-time activity. It’s essential to continuously monitor and review the effectiveness of the control measures. Regularly update the risk assessment to reflect any changes in the workplace, such as new equipment, processes, or personnel. Encourage employees to report new hazards and participate in the risk assessment process. It is also important to make sure that your new control measure have not inadvertently introduced a new risk or hazard into your work environment. Documentation Documenting the risk assessment process is crucial for accountability and compliance. Keep detailed records of identified hazards, risk assessments, and implemented control measures. Communicate the findings and safety measures to all employees to ensure they are aware of the risks and how to protect themselves. Consultation Don't forget that at every stage of the risk assessment process, you must consult with the workforce. This is a legal obligation, but it is also extremely useful to the employer, as the workers who are doing the job are in the best position to identify risks and hazards in their own work environment and to find ways to control them too. By following these steps and principles - organisations can create a safer work environment, reduce the likelihood of incidents and injuries, and promote a culture of safety. Remember, a proactive approach to risk assessment not only protects employees but also enhances productivity and morale.
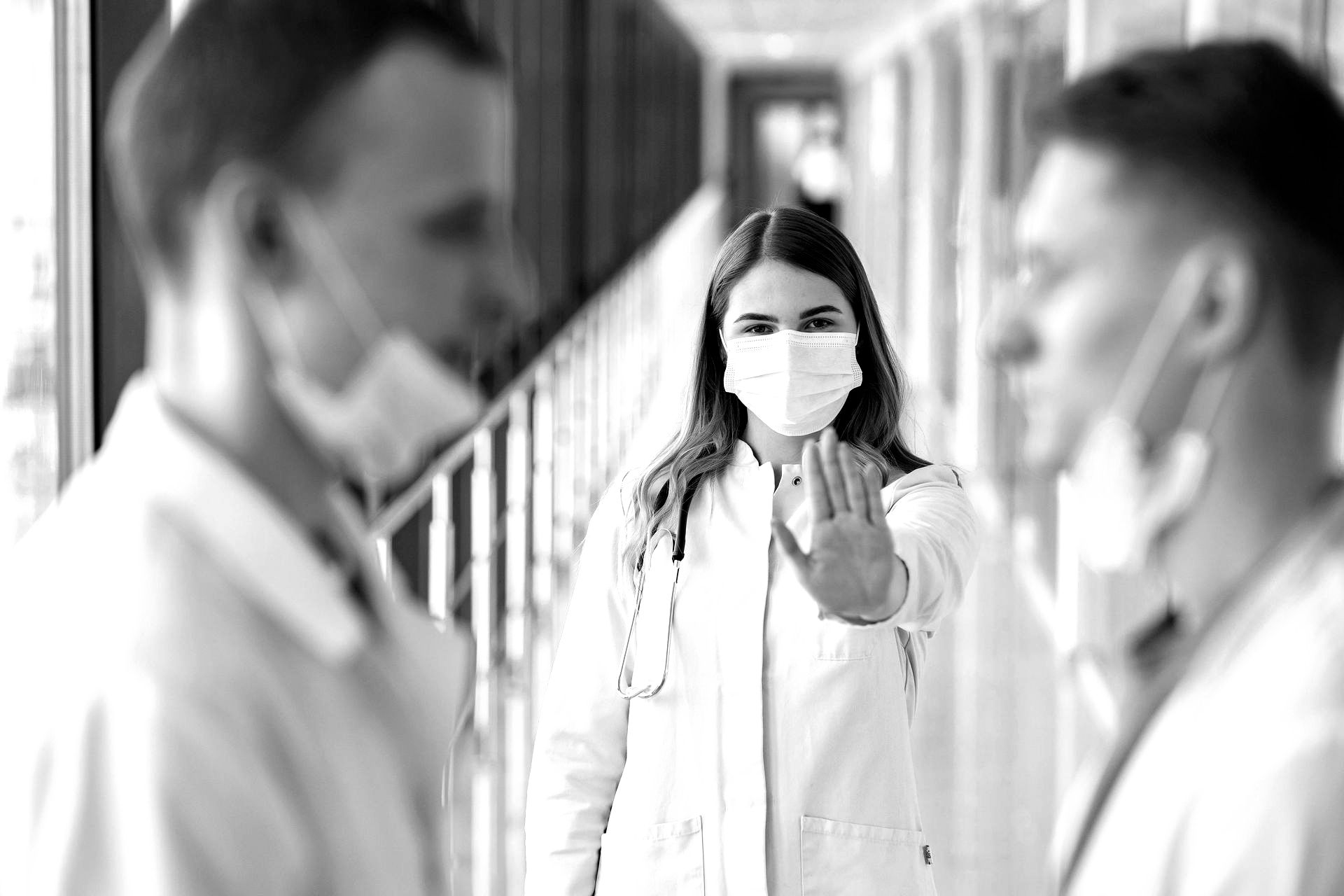
Work-related gendered violence is any behaviour, directed at any person, or that affects a person, because of their sex, gender or sexual orientation, or because they do not adhere to socially prescribed gender roles, that creates a risk to health and safety. But what does it actually look like? Work-related gendered violence can range in severity. It might include things like: · Indecent phone calls · Offensive language or images · Sexually explicit social media, text messages or emails · Repeated or inappropriate advances · Rude gestures, staring or intimidation · Put downs, ostracism or exclusion · Sexually suggestive comments or jokes · Unwelcome touching, hugging or cornering · Intrusive questions · Physical assault including sexual assault and rape · Sexual harassment · Verbal abuse · Stalking · Being undermined in your work or position Work-related violence and sexual harassment can cause physical and/or mental injury – this is an Occupational Health and Safety Issue. Like all OHS issues, we need to prevent them by: 1. Identifying the hazards and assessing the risks 2. Implementing measures to eliminate or control the risks 3. Review the effectiveness of control measures For more information on work-related gendered violence and how to control this hazard, take a look at the guidance material at: Gendered violence | WorkSafe Victoria . If you require additional assistance or information on accessing information please contact BeSafe .
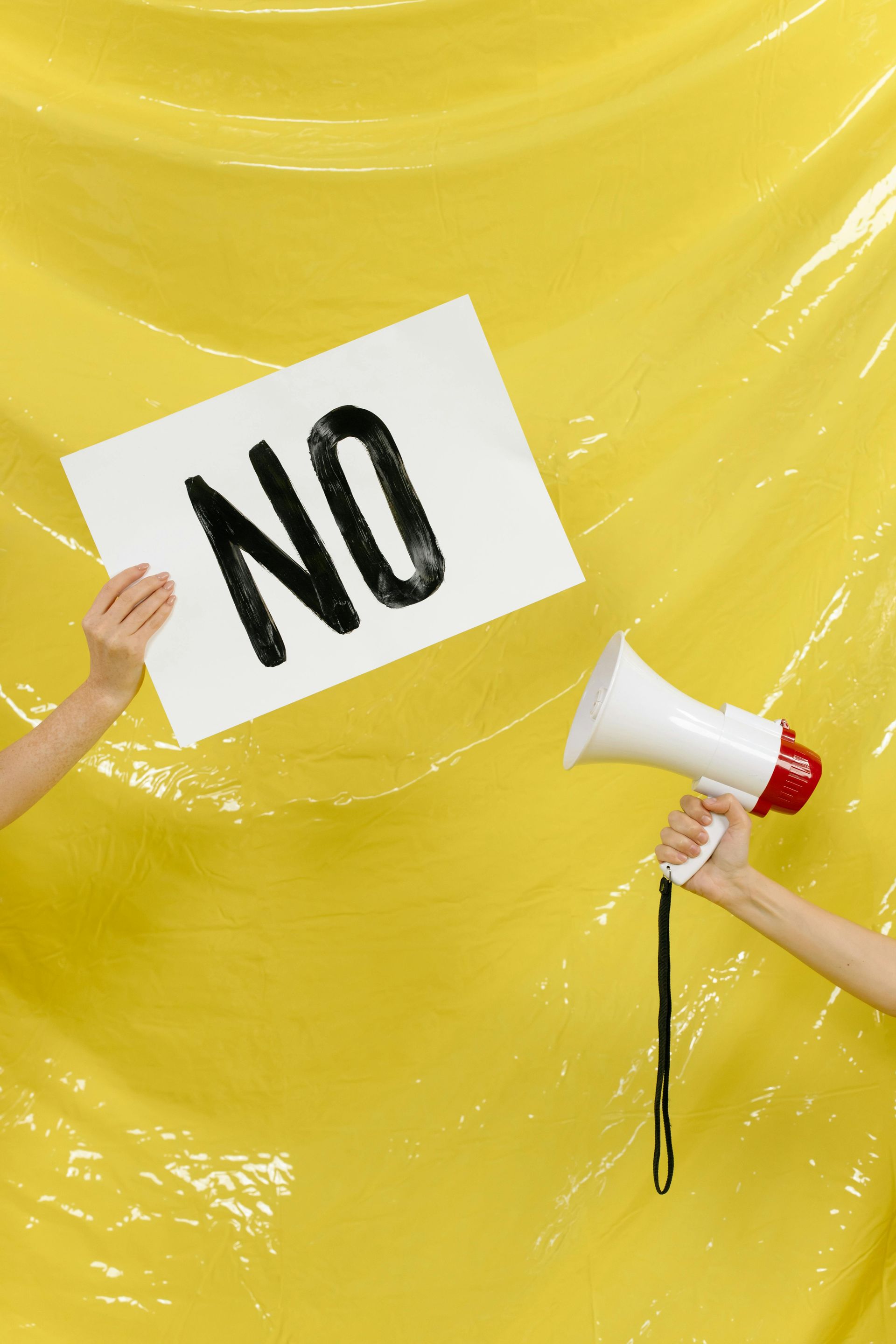
While the entitlement to information is clear and a legal requirement, there are often challenges that HSRs face in exercising this right: 1. Information Overload: With vast amounts of safety-related data available in larger organizations, HSRs may feel overwhelmed by the volume of information they need to digest. To address this, organizations should provide: clear, organized, and accessible safety reports rather than overwhelming HSRs with excessive detail. 2. Resistance from Employers : Sometimes, employers may be hesitant to provide information due to concerns about confidentiality or legal liability. However, under the OHS Act, there are clear guidelines on the types of information that must be disclosed. HSRs should be well-informed about their rights and, if necessary, seek support from regulatory bodies or unions. 3. Access to Real-Time Data In fast-paced workplaces, it can be challenging for HSRs to stay updated with real-time health and safety data. Regular meetings or briefings between management and HSRs can ensure that everyone is on the same page when it comes to ongoing risks or emerging hazards. Conclusion An HSR’s entitlement to information is a cornerstone of workplace health and safety. It empowers representatives to make informed decisions, foster a culture of safety, and protect workers from potential harm. Employers, for their part, have a legal and ethical responsibility to ensure that HSRs have timely, accurate, and relevant data at their disposal. When information flows freely between management and HSRs, it creates a safer, more collaborative work environment where everyone benefits. For HSRs, understanding the full extent of their right to information—and how to use it effectively—can make all the difference in maintaining a safe workplace. It's not just about compliance; it's about preventing accidents, promoting well-being, and building a culture of safety that benefits everyone in the workplace. If you require additional assistance or information on accessing information please contact BeSafe .
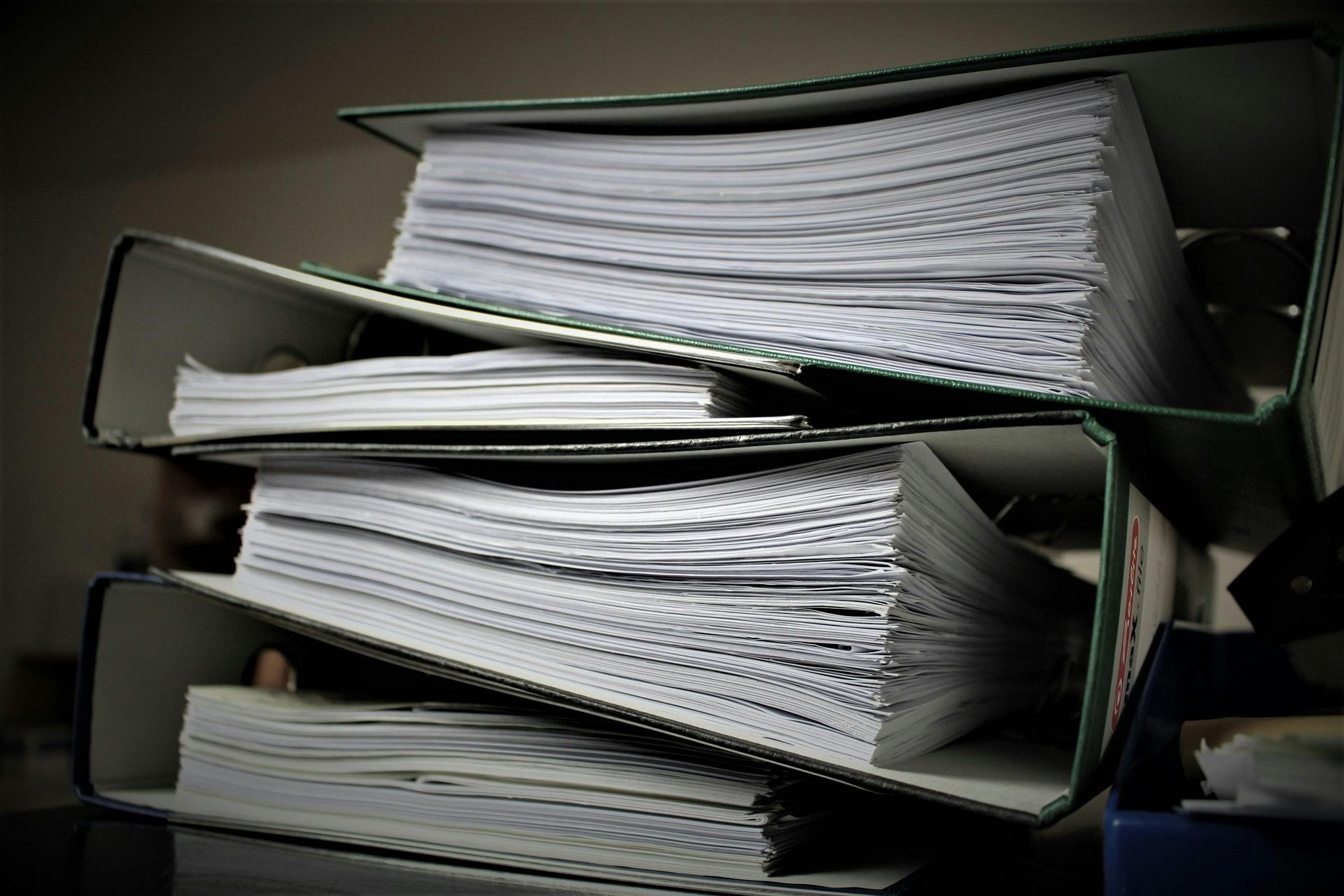
A Health and Safety Representative (HSR) plays a crucial role in ensuring workplace safety and compliance with health and safety regulations. The specific information a Health and Safety Representative can access vary as limitations do exist. However, generally, an HSR can access the following types of information: 1. Risk Assessments and Hazard Identification - Workplace Risk Assessments: Documentation and reports identifying potential risks or hazards in the workplace (e.g., chemical hazards, machinery, ergonomics, etc.). - Hazard Control Measures: Information about existing controls and measures in place to mitigate or eliminate identified risks. 2. Health and Safety Policies and Procedures - Workplace Safety Policies: Company-wide health and safety policies, guidelines, and protocols. - Emergency Procedures: Evacuation plans, first aid protocols, and procedures for responding to accidents or emergencies. 3. Workplace Injury and Incident Reports - Accident and Injury Reports: Documentation of workplace accidents, injuries, and near misses. This includes investigation reports and any follow-up actions taken to prevent recurrence. - Incident Logs: Records of any safety incidents, including time, place, cause, and impact on workers. 4. Workplace Safety Training Records - Training Records: Information on safety training and certifications for workers, including what training has been provided and whether employees are up to date on required courses. - Safety Inductions: Details of safety induction programs for new employees or contractors. 5. Workplace Inspections and Audit Results - Inspection Reports: Results from routine or special safety inspections of the workplace. - Audit Results: Internal or external audits that evaluate safety systems, compliance, and performance. 6. Exposure Records - Workplace Exposure Monitoring: Records detailing employee exposure to potentially hazardous substances, including chemicals, noise, and physical agents. - Personal Protective Equipment (PPE) Use: Information about PPE requirements and employee compliance with PPE protocols. 7. Health Surveillance Data - Medical Records: In Victoria, HSRs may have access to workers' health surveillance records, particularly if the worker is exposed to harmful substances or physical conditions. However, there are limitations and requirements. (see below). - Workplace Health Monitoring: Data on health monitoring initiatives like hearing tests, lung function tests, etc. 8. Compliance and Regulatory Documents - Compliance Records: Documents related to compliance with national or regional health and safety laws and regulations, such as safety permits and certifications. - Regulatory Inspections : Reports and recommendations from inspections conducted by regulatory agencies (e.g., OSHA in the U.S., HSE in the UK). 9. Corrective Actions and Safety Committees - Corrective Action Plans: Information about actions taken or planned in response to identified hazards, incidents, or safety deficiencies. - Safety Committee Minutes: Minutes from health and safety meetings or committees, where safety issues and concerns are discussed. 10. Workplace Safety Reports and Statistics - Health and Safety Performance Data**: Statistics related to workplace accidents, injuries, and safety performance (e.g., incident rates, lost time injury frequency rates). - Occupational Health Data: Data on the health of employees, including common workplace illnesses or injuries. 11. Consultation with Workers - Feedback and Concerns: Input from workers about safety concerns or potential hazards they have observed or experienced. Access Rights and Limitations While an HSR has broad access to health and safety information, the exact level of access may depend on: - Confidentiality and Privacy: Sensitive personal information (e.g., medical records) may be restricted, but HSRs typically have access to aggregate data rather than individual health records. HSRs can obtain permission from the individual or individuals involved or have sensitive information redacted. In Victoria, employers are required to consult with and provide relevant safety information to HSRs to enable them to perform their duties effectively. This helps ensure that the workplace is as safe as possible and that health risks are minimized. If you require additional information or clarification, please contact BeSafe .
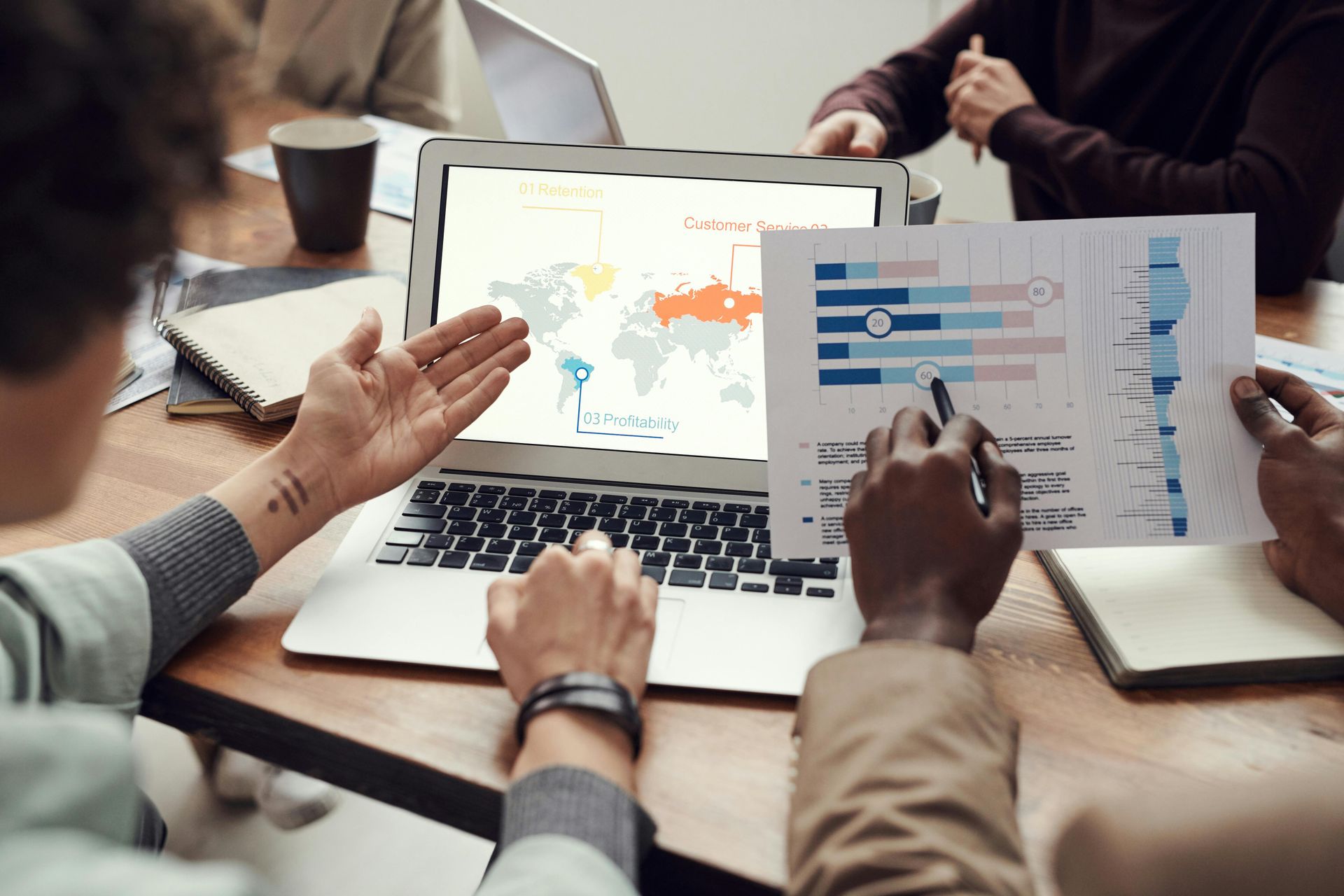
The entitlement of HSRs to access information is not just a legal right but a practical necessity for several reasons: Informed Decision-Making: To represent workers effectively, HSRs need to have comprehensive, up-to-date information on health and safety risks. Without access to this data, they would be ill-equipped to identify hazards, make safety recommendations, or engage in meaningful consultations with employers and management. Proactive Risk Management: Timely access to information helps HSRs identify potential hazards before they cause harm. If HSRs can analyse incident reports, safety audits, and risk assessments, they can recommend changes to prevent future accidents, rather than just reacting to problems as they arise. Promoting a Safe Work Culture: Transparency in safety matters fosters a culture of openness and accountability in the workplace. When employees see that their HSRs are well-informed and have the authority to act on safety matters, it builds trust in the safety system. Workers are more likely to report hazards or concerns if they know there is a system in place that takes them seriously. Legal Compliance: In Victoria, failure to provide HSRs with relevant information can result in legal repercussions for employers. By ensuring that HSRs have the information they need, employers not only comply with legal requirements but also demonstrate their commitment to creating a safe work environment. Conclusion An HSR’s entitlement to information is a cornerstone of workplace health and safety. It empowers representatives to make informed decisions, foster a culture of safety, and protect workers from potential harm. Employers, for their part, have a legal and ethical responsibility to ensure that HSRs have timely, accurate, and relevant data at their disposal. When information flows freely between management and HSRs, it creates a safer, more collaborative work environment where everyone benefits. For HSRs, understanding the full extent of their right to information—and how to use it effectively—can make all the difference in maintaining a safe workplace. It's not just about compliance; it's about preventing incidents, promoting well-being, and building a culture of safety that benefits everyone in the workplace. If you require more information or guidance on your right to information please contact BeSafe
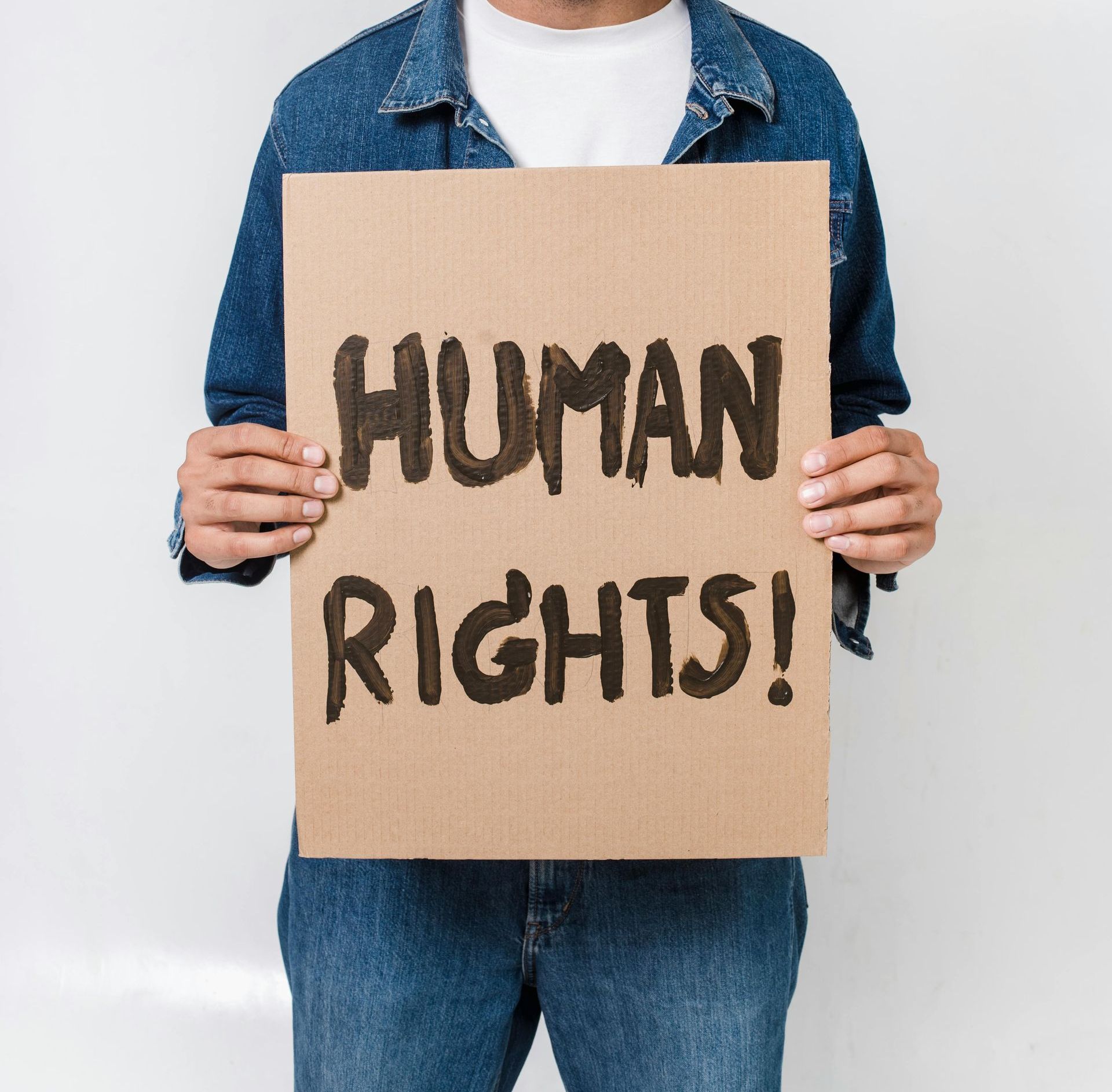
Last week, on 30th October 2024, the Australian Government ratified the International Labour Organisation (ILO) Conventions relating to Workplace Health and Safety. This follows a landmark event in 2022, when the ILO recognised a safe and healthy work environment as a fundamental right at work. It became the 5th Workplace Human Right: freedom of association and the effective recognition of the right to collective bargaining; the elimination of all forms of forced or compulsory labour; the effective abolition of child labour; the elimination of discrimination in respect of employment and occupation; and a safe and healthy working environment. Find out more about the ILO declaration and the latest changes at: ILO Declaration on Fundamental Principles and Rights at Work | International Labour Organization Australia becomes world leader in protecting workers’ rights and safety - Australian Council of Trade Unions
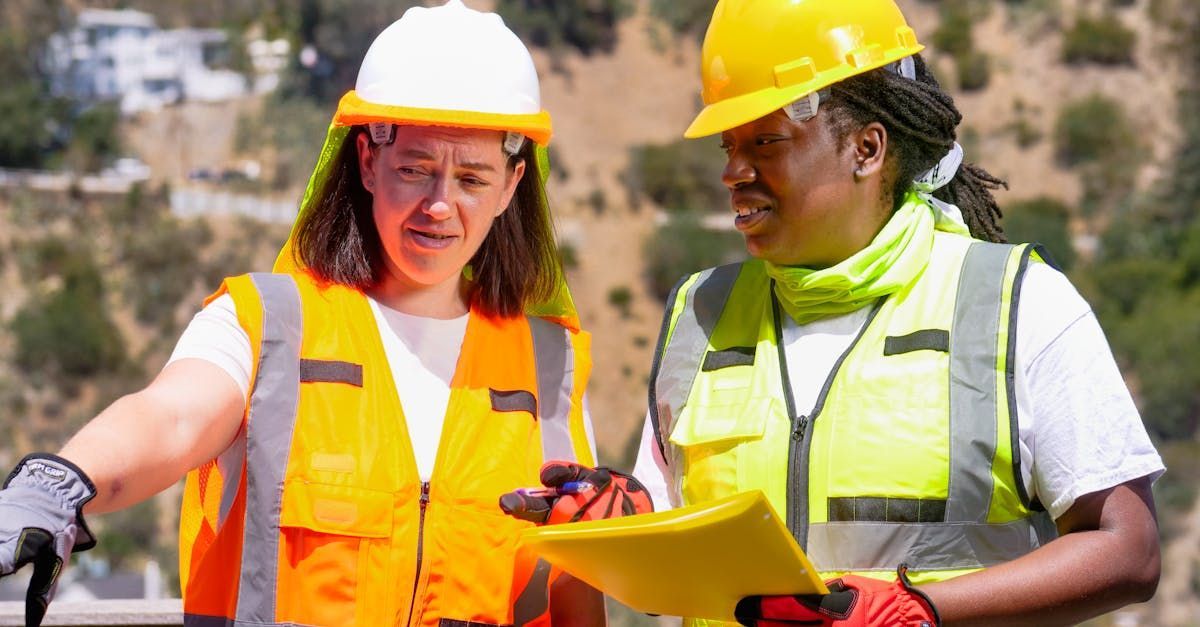
Prioritizing Workplace Safety: Essential Tips for a Safer Environment In today's fast-paced work environments, prioritizing safety is crucial for the well-being of employees and the success of businesses. A safe workplace not only protects employees from harm but also boosts morale, increases productivity, and reduces costs associated with accidents and injuries. In this post, we'll explore key workplace safety tips that every employee and employer should implement. 1. Understand the Safety Regulations and Policies Familiarize Yourself with the OHS Act, Regulations and Guidelines the provide and outline workplace safety standards. Knowing these guidelines is essential for compliance and safety. Every organization should have its own safety policies. Make sure to review these regularly and understand your responsibilities. 2. Maintain a Clean and Organized Workspace Clutter Control: Keep your workspace tidy to prevent tripping hazards. Regularly declutter and organize materials and tools. Proper Storage: Store items appropriately. Heavy items should be kept at waist level to minimize strain when lifting. 3. Ergonomics Matter Adjust Your Workspace: Ensure your desk, chair, and computer are set up ergonomically. Adjust your chair height and monitor position to reduce strain on your body. Take Breaks: Schedule regular breaks to stretch and move around, helping to reduce fatigue and improve focus. 4. Use Personal Protective Equipment (PPE) Know Your Gear: If your job requires PPE, such as gloves, goggles, or helmets, ensure you know how to use and maintain them properly. Report Damaged Equipment: Always report any damaged PPE to your supervisor immediately to ensure your safety. 5. Stay Aware of Your Surroundings Situational Awareness: Be mindful of your environment, including potential hazards like wet floors, moving machinery, or colleagues in your vicinity. Emergency Exits: Familiarize yourself with emergency exits and evacuation routes. Know where to go in case of an emergency. 6. Communicate Openly Report Hazards: If you notice unsafe conditions or practices, report them to your supervisor. Open communication can prevent accidents before they happen. Encourage Feedback: Foster a culture where employees feel comfortable sharing safety concerns or suggestions for improvement. 7. Emergency Preparedness Know the Plan: Ensure you are aware of the company’s emergency procedures for situations like fires, medical emergencies, or natural disasters. Training: Remain up to date with HSR and OHS for Leaders training. This knowledge is invaluable. Creating a safe workplace is a collective responsibility that requires the commitment of both employees and employers. By understanding safety regulations, maintaining an organized workspace, using the right protective equipment, and fostering open communication, we can create an environment where everyone feels secure. Remember, safety is not just a policy; it’s a culture. Call to Action Let’s make safety a priority! Share your workplace safety tips in the comments below, and don’t forget to update your training
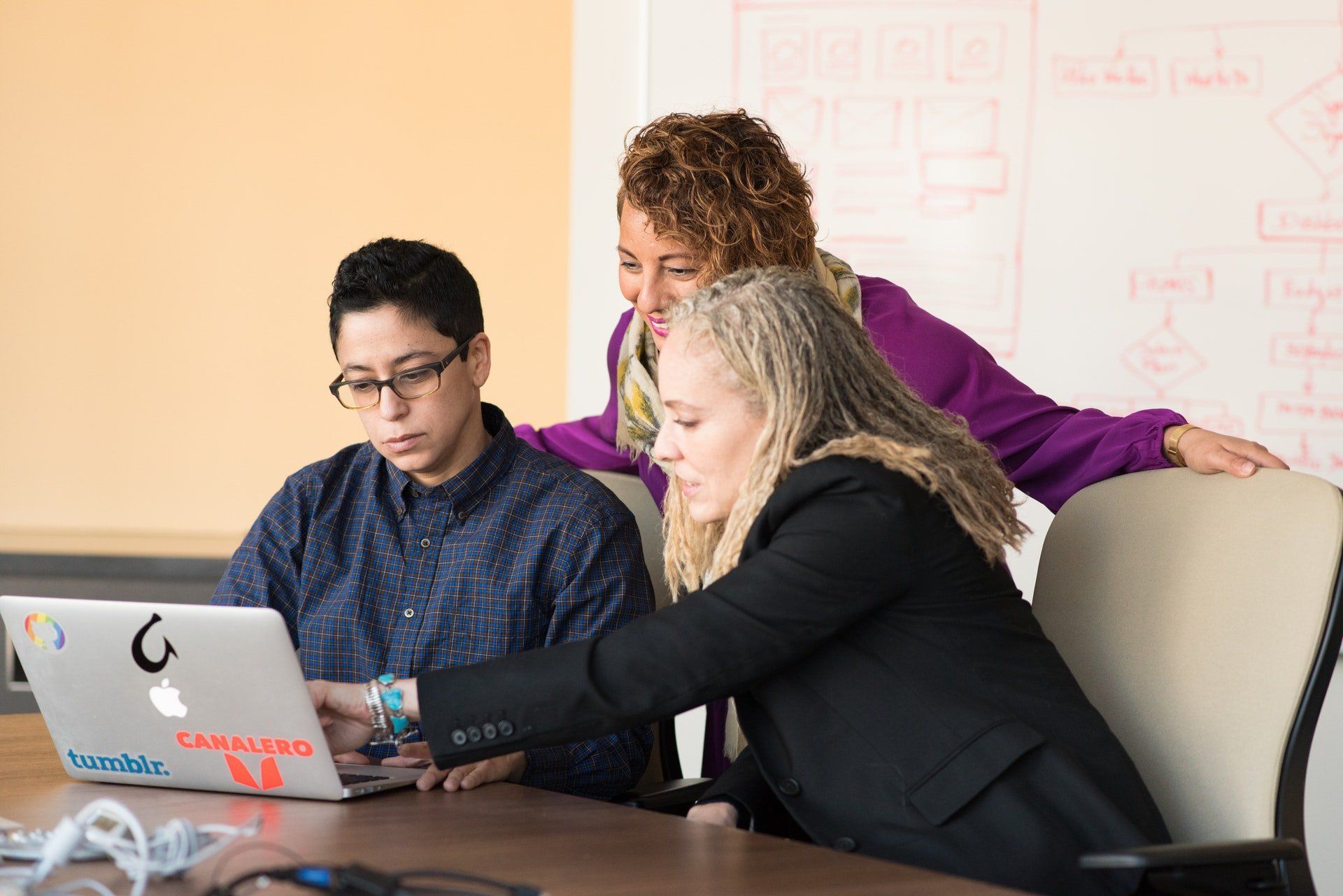
Health and Safety Representatives, or HSRs, play an essential role in tackling psychosocial hazards within the workplace. Here’s how they contribute: 1. **Awareness and Training**: HSRs can enhance awareness of psychosocial hazards, such as stress, bullying, and work-life imbalance, by organizing training sessions and providing informative resources. 2. **Identifying Hazards**: They can proactively identify potential psychosocial risks by interacting with employees, conducting surveys, and observing the dynamics of the workplace. 3. **Reporting and Communication**: HSRs promote open dialogue about mental health concerns, empowering employees to share issues without fear of retaliation. 4. **Collaboration with Management**: They work alongside management to create policies and practices that aim to mitigate psychosocial risks, ensuring that employee feedback is valued. 5. **Support and Resources**: HSRs can connect employees with mental health resources and support systems, including counseling services or employee assistance programs. 6. **Monitoring and Evaluation**: By assessing the effectiveness of implemented strategies, HSRs can ensure that interventions are effective and make necessary adjustments. 7. **Creating a Positive Culture**: They foster a workplace culture that prioritizes mental health, inclusivity, and respect, thereby reducing the stigma surrounding discussions of psychosocial issues. By actively participating in these aspects, HSRs contribute to cultivating a safer and healthier work environment, ultimately enhancing employee well-being.
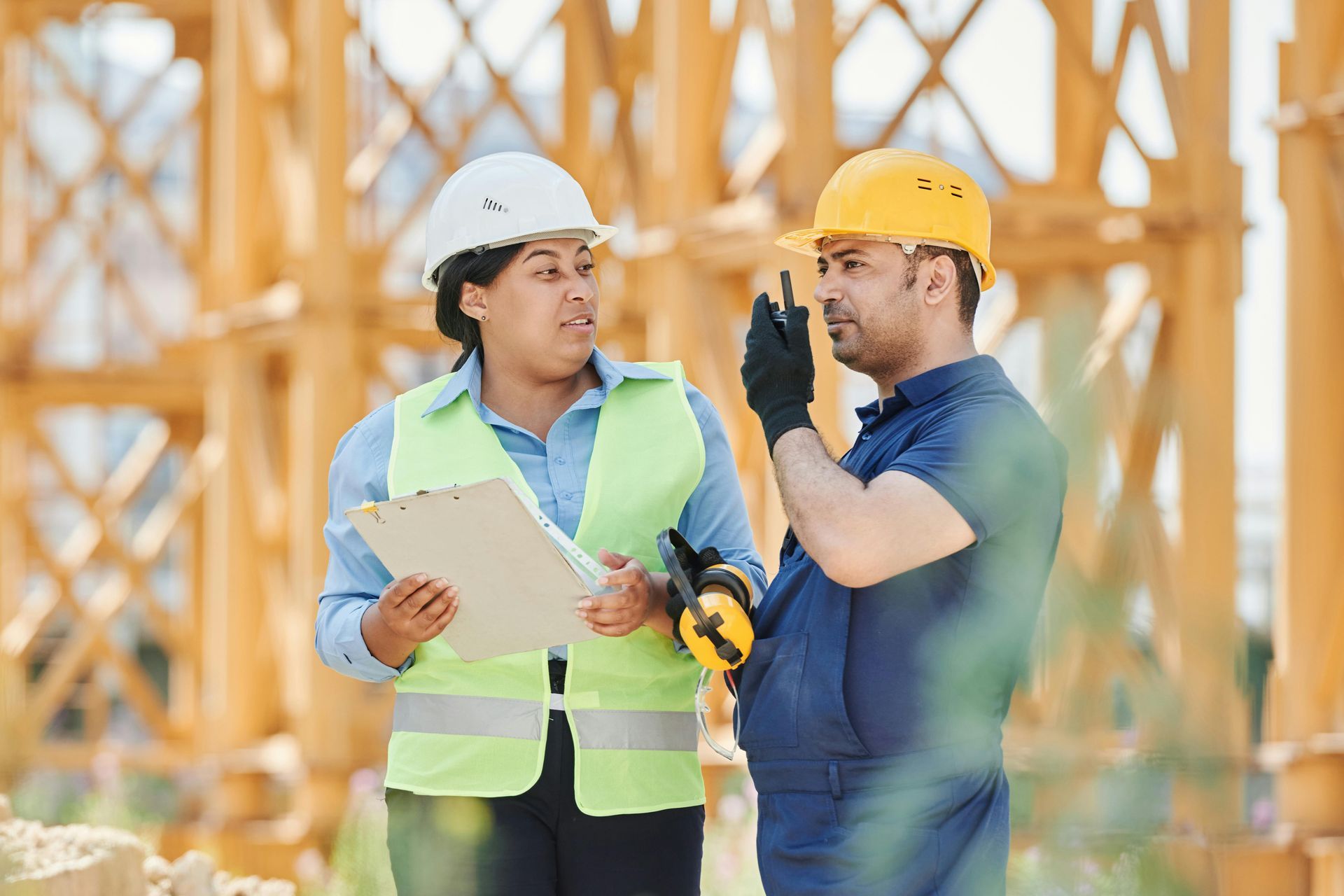
Health and Safety Representatives (HSRs) play an absolutely vital role in the effectiveness of safety committees for several compelling reasons: 1. **Direct Communication**: HSRs serve as a crucial bridge and link between employees and management, ensuring that any worker concerns, feedback, and insights about safety issues are effectively communicated and addressed in a timely manner. 2. **Representation**: They passionately represent the interests of employees, advocating not just for their safety and well-being, but also striving to ensure that all voices are heard in crucial safety discussions. This advocacy helps build trust and transparency within the workplace. 3. **Knowledge of Workplace Hazards**: HSRs often possess invaluable first-hand knowledge of specific workplace hazards, enabling them to provide essential insights into risk assessment and effective mitigation strategies. Their experience greatly contributes to identifying potential risks before they become significant issues. 4. **Training and Education**: They have the capability to facilitate comprehensive training sessions and actively promote awareness of best safety practices, helping to nurture and foster a robust culture of safety throughout the organization. 5. **Monitoring Compliance**: HSRs play a key role in monitoring adherence to safety regulations and company policies. By doing so, they ensure that safety standards are not only set but are consistently met, thereby reducing the likelihood of accidents and injuries. 6. **Encouraging Reporting**: By creating a supportive and open environment, HSRs encourage employees to report unsafe conditions and near misses. This practice is essential for proactive safety management and helps in identifying issues that may otherwise go unreported. 7. **Collaboration**: HSRs work collaboratively and effectively with safety committees to develop and implement comprehensive safety policies and programs, thereby enhancing the overall safety culture within the organization. In essence, HSRs are integral to promoting a safe work environment and ensuring that safety committees operate efficiently and inclusively. Their presence not only aids in compliance but also solidifies the foundational belief that safety is a shared responsibility among all employees. If you would like to know more information on how BeSafe can assist with your safety committee please contact us .
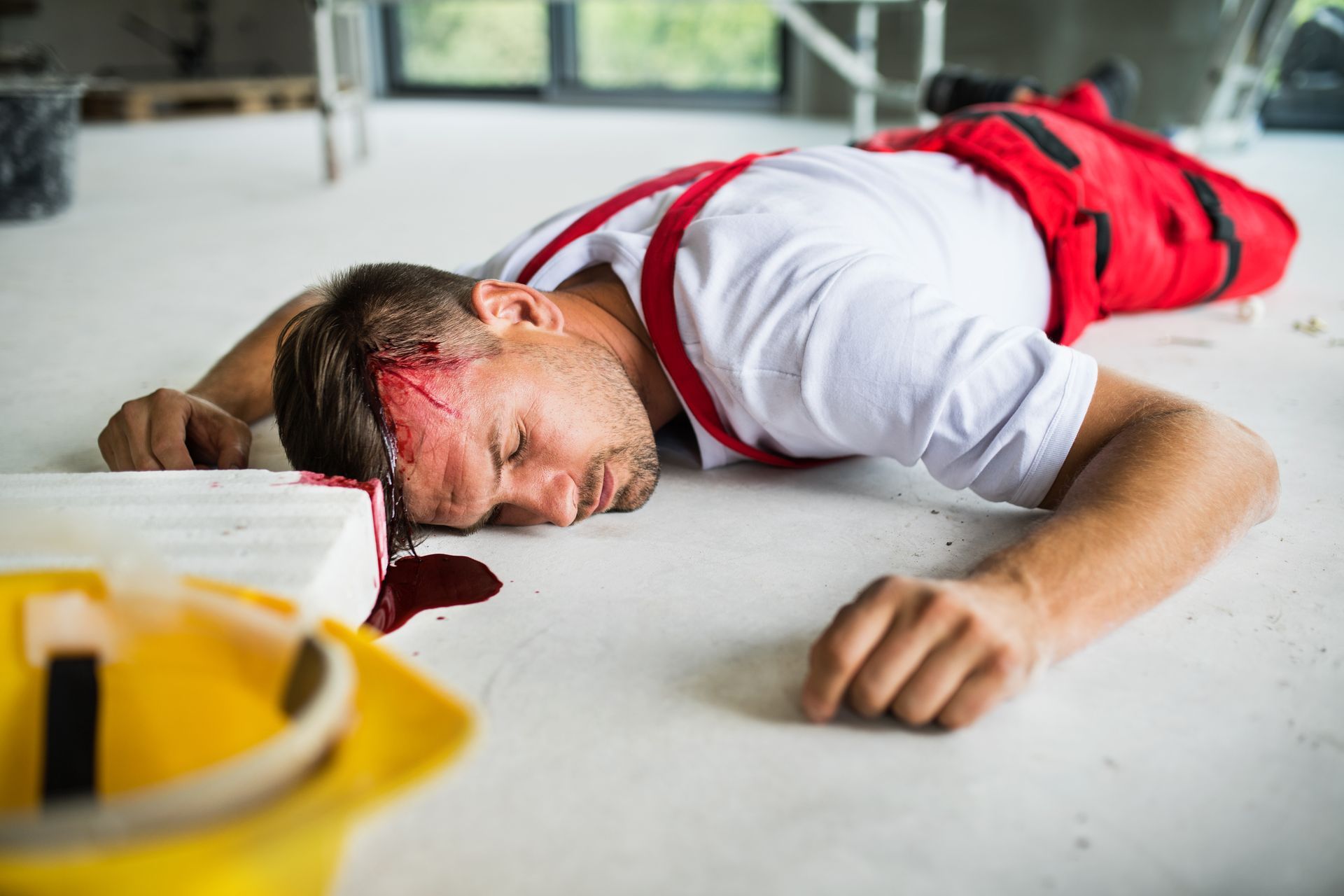
Valmont (Vic) Pty Ltd was sentenced in the Sunshine Magistrates' Court on Thursday 3 October after earlier being found guilty of one charge of failing to provide and maintain a safe system of work and one charge of failing to ensure a workplace under its management or control was safe and without risks to health. Valmont was fined without a conviction and mandated to pay $42,752 in costs. The company had been assigned to transform level two of a multistorey car park on Clarke Street in Sunshine into office space. The project entailed the removal of a car park ramp between levels one and two, the installation of structural steel and formwork, and the pouring of concrete into the void to finalize the office floor. In July 2019, a segment of the formwork collapsed when a steel beam connecting it to the existing slab detached as the concrete was being poured, resulting in three workers plummeting more than two metres to the level below. Two workers were hospitalized with serious injuries. A WorkSafe inquiry revealed that Valmont had failed to arrange for a building surveyor or engineer to inspect the formwork prior to the concrete pour. The court concluded that it would have been reasonably practicable for Valmont to have organized a pre-pour inspection and to have secured a written inspection report affirming that the formwork was structurally sound to bear the concrete pour. WorkSafe Executive Director of Health and Safety Sam Jenkin said working with formwork could be high risk and there was no excuse for omitting important safety processes. "Having a competent person inspect formwork before a concrete pour begins is a crucial step designed to avoid exactly this kind of disastrous scenario," Mr Jenkin said. "In this case two workers were injured and it could very easily have been much, much worse." To prevent falls when working with formwork employers should: Ensure a competent person produces a formwork design capable of supporting the expected dynamic and static loads. Have systems in place to formally sign off a formwork deck as structurally sound, complete and safe for other trade workers to use as a work platform. Provide employees undertaking construction work with site specific training, including the onsite risks associated with formwork decks. Ensure High Risk Construction Work is not performed unless a Safe Work Method Statement is prepared and followed. Use a fall arrest system, such as a catch platform or safety nets. For more information visit: https://www.worksafe.vic.gov.au/news/2024-10/125000-fine-after-workers-fall-concrete-formwork-collapse
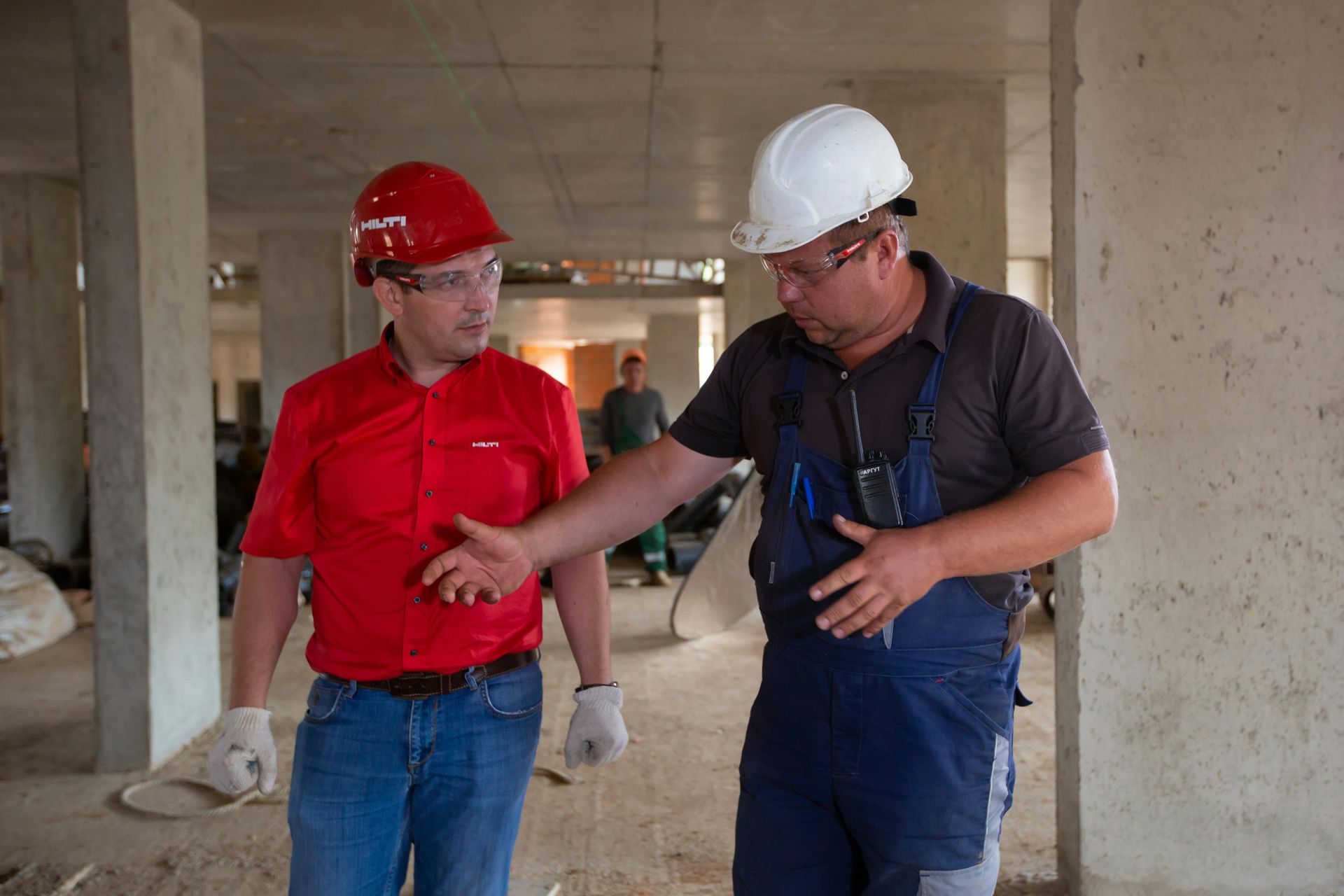
Health and Safety Representatives (HSRs) are essential for cultivating a safe work environment, offering numerous benefits to businesses: 1. **Risk Identification**: HSRs are instrumental in spotting potential hazards in the workplace, allowing for proactive steps to manage risks prior to accidents or injuries occurring. 2. **Employee Advocacy**: They voice employees' concerns regarding health and safety issues, promoting an atmosphere of open dialogue and trust. 3. **Training and Awareness**: HSRs can facilitate training sessions and safety awareness initiatives, ensuring that all employees are well-informed about best practices and protocols. 4. **Compliance Support**: HSRs assist in ensuring the organization adheres to health and safety regulations, minimizing the likelihood of legal complications and fines. 5. **Incident Reporting**: They streamline the process of reporting and investigating workplace incidents, which can lead to enhanced safety measures and policies. 6. **Improved Morale**: A strong commitment to health and safety can boost employee morale and job satisfaction, resulting in higher retention rates and productivity levels. 7. **Cost Savings**: By mitigating workplace accidents and related costs (such as medical expenses and productivity loss), HSRs contribute positively to the financial wellbeing of the organization. 8. **Crisis Management**: HSRs play a pivotal role in emergency preparedness, aiding businesses in developing and executing effective response strategies. In conclusion, HSRs are indispensable in establishing a safer workplace, ultimately contributing to improved business performance.
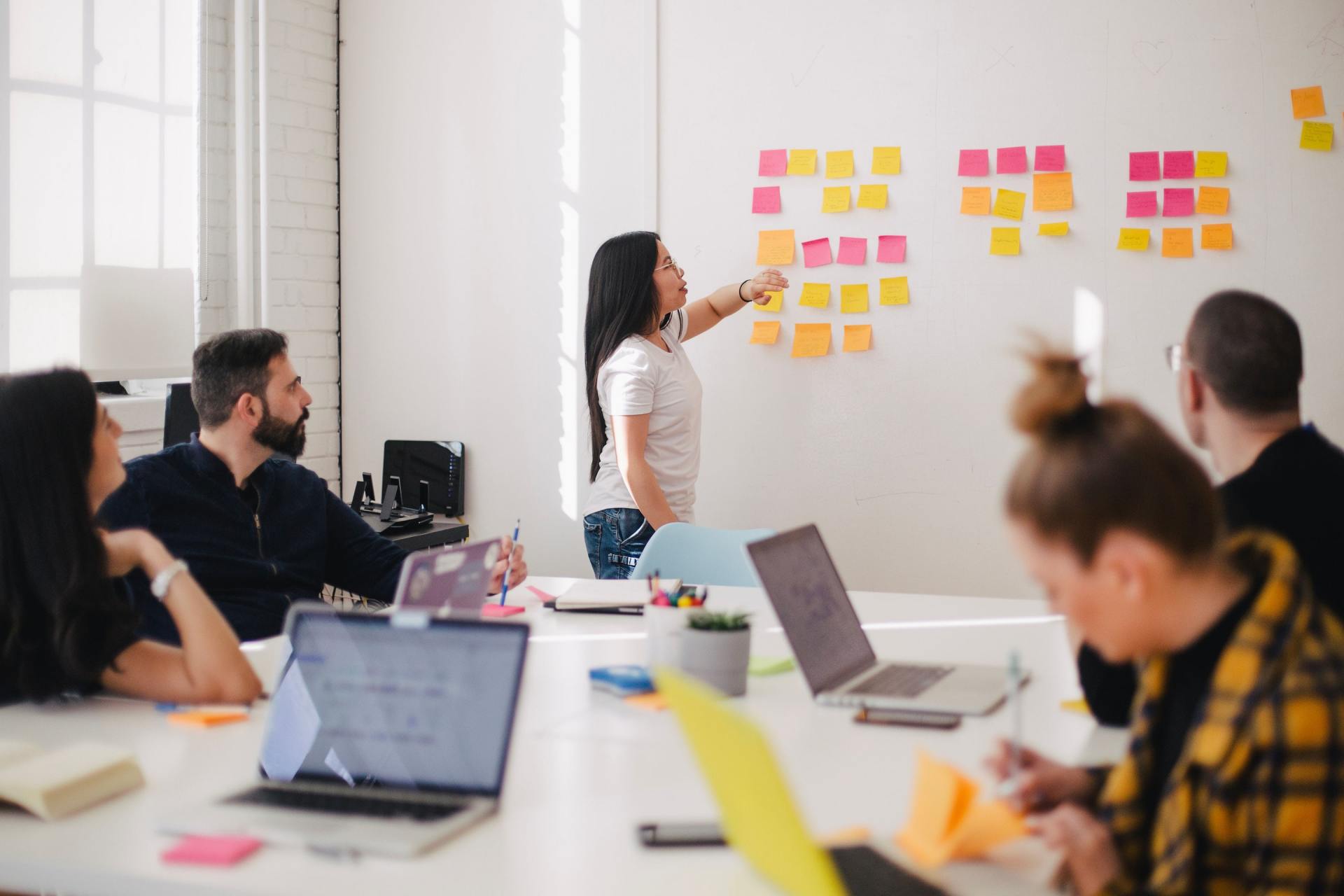
Health and Safety Representatives (HSRs) play a critical role in promoting workplace safety and health standards. HSR safety training is essential for several reasons, contributing to a safer and more productive work environment. Here’s why HSR safety training matters: 1. Empowers Representation HSRs serve as the voice of workers regarding health and safety issues. Training equips them with the knowledge and skills needed to represent their colleagues effectively, ensuring that concerns are raised and addressed promptly. 2. Enhances Awareness HSR training provides comprehensive knowledge about workplace hazards, safety regulations, and best practices. This awareness helps HSRs identify risks, implement preventative measures, and create a culture of safety within the organization. 3. Improves Communication Effective communication is crucial in conveying safety protocols and concerns. Training helps HSRs develop skills to communicate effectively with both employees and management, fostering collaboration and ensuring that safety messages are clear and understood. 4. Facilitates Risk Management HSRs trained in safety protocols can conduct risk assessments and identify potential hazards in the workplace. This proactive approach to risk management helps prevent accidents and injuries before they occur. 5. Promotes Compliance Understanding relevant health and safety legislation is a key component of HSR training. HSRs learn to ensure that the organization complies with legal requirements, reducing the risk of fines and legal issues while promoting a safe work environment. 6. Encourages Employee Engagement When HSRs are well-trained, they can engage employees in safety initiatives, encouraging a collective responsibility for workplace safety. This involvement can lead to increased awareness and adherence to safety practices among all employees. 7. Supports Continuous Improvement HSR training emphasizes the importance of continuous improvement in safety practices. Trained HSRs can monitor safety performance, provide feedback, and recommend changes to enhance overall workplace safety standards. 8. Boosts Morale and Productivity A safe workplace leads to increased employee morale and productivity. When employees feel safe, they are more likely to be engaged and motivated, leading to better performance and lower turnover rates. In conclusion HSR safety training is vital for fostering a culture of safety within the workplace. By empowering Health and Safety Representatives with the necessary knowledge and skills, organizations can enhance communication, improve risk management, and ultimately create a safer environment for all employees. Investing in HSR training is not just a legal obligation; it’s a commitment to the health and well-being of every worker. For more information on BeSafe's available training click here
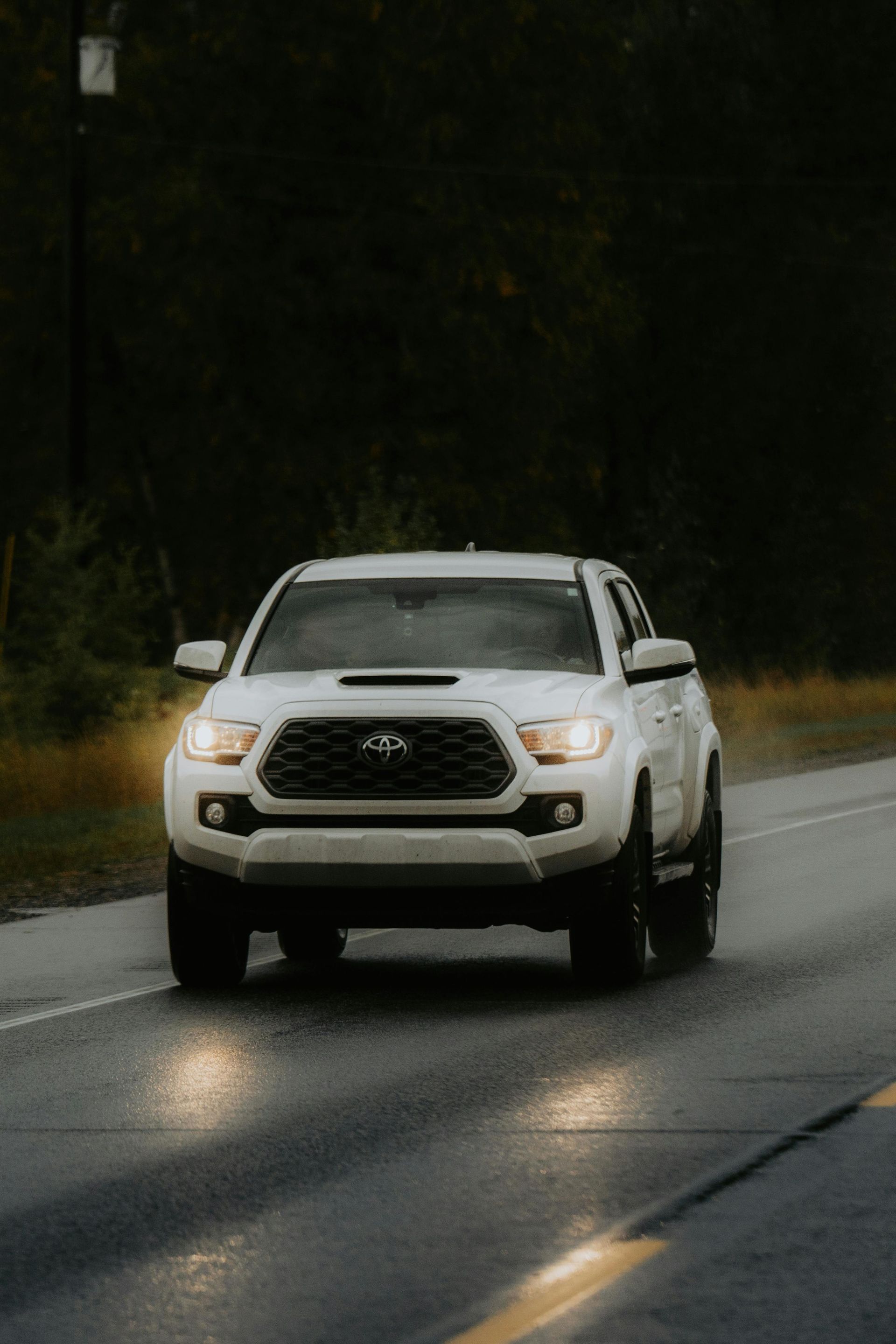
The director, 31, was sentenced in the Mansfield Magistrates' Court on Wednesday 2 October after pleading guilty to a single charge of failing to ensure that a workplace under their management or control was safe and without risks to health. He was fined without conviction and also ordered to pay costs of $4,249. In February 2022, the director and his 19-year-old apprentice had completed the installation of a hot water service at a property in Bridge Creek when it was decided that the client would join them on the return trip to Mansfield. The court heard that since the director's work ute had only two seats, there was a conversation about the apprentice being transported in the toolbox mounted on the rear tray. During the estimated 20-25 minute drive, the apprentice recorded a video expressing his discomfort and the heat he experienced in that cramped space. Upon reaching Mansfield, the apprentice's brother observed him being released from the toolbox, his face red and hunched over, while the director and client stood nearby, laughing and enjoying beers. The incident was reported several months later, after the apprentice confided in his mother, who then notified his support officer at Apprenticeships Victoria. WorkSafe's investigation revealed that certain tools had been left in the toolbox alongside the apprentice, posing a risk of severe injury or fatality should the ute be involved in an accident or come to an abrupt halt. It was reasonably practicable for the director to reduce the risk by not driving the ute, or not allowing it to be driven, when a person was in the toolbox. WorkSafe Executive Director Health and Safety Sam Jenkin said there was no excuse for putting a young apprentice in such a vulnerable position. "Illegally transporting this young apprentice in the back of a toolbox was extremely unsafe and could have had absolutely catastrophic consequences," Mr Jenkin said. "WorkSafe will continue to hold employers accountable when they fail to prioritise safety and wellbeing, particularly for young workers who won’t always have the confidence to speak up if something is wrong." For more information: https://www.worksafe.vic.gov.au/news/2024-10/plumber-fined-after-driving-ute-teen-toolbox
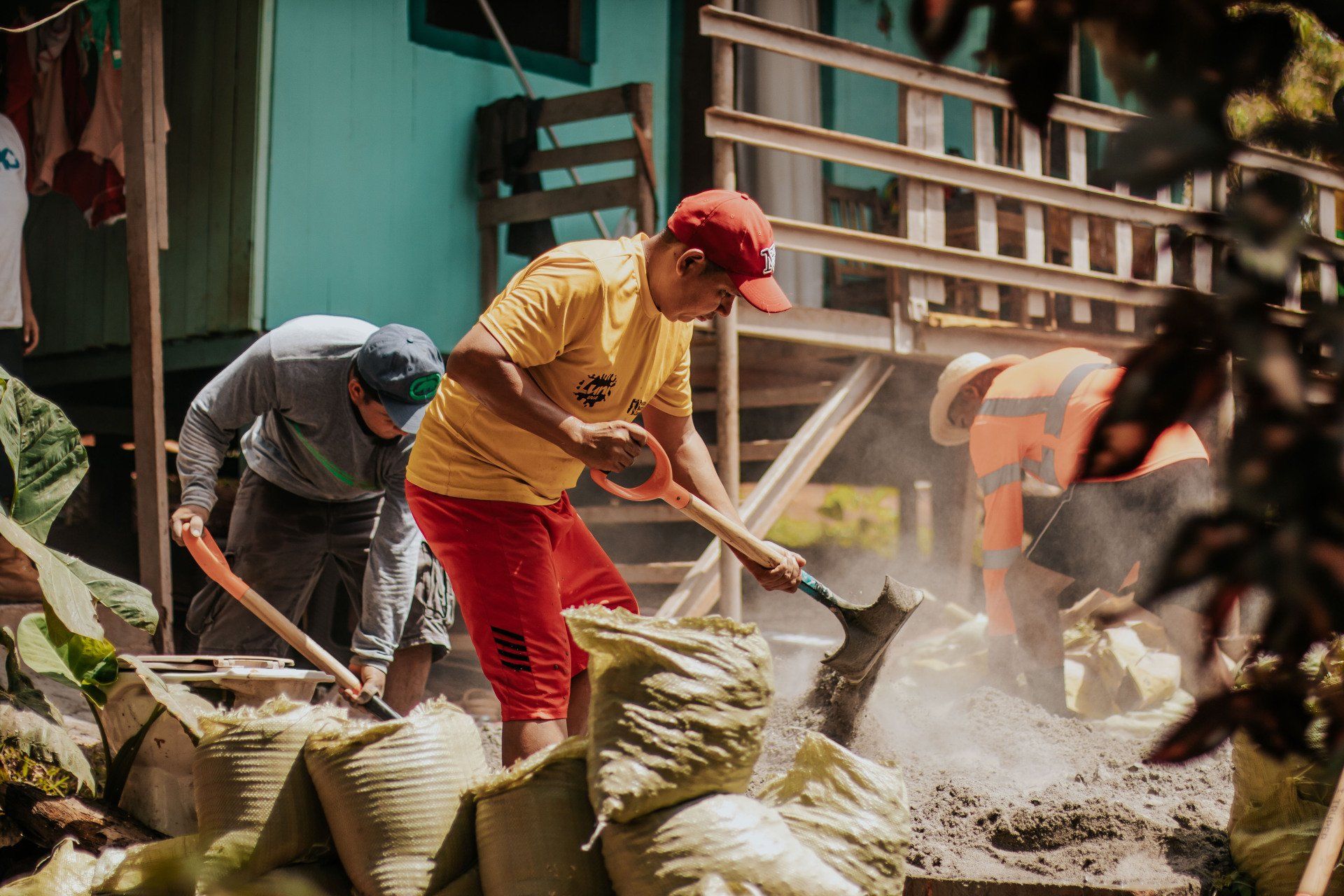
Safety should never rely on luck. It is a total commitment from management down to the workers on the tools: to report, consult and continually educate on hazards and risks. Let's take a moment to emphasize the importance of fostering a workplace culture where the fundamentals of safety are never overlooked. It's essential to speak up about potential hazards and engage in open consultations with all levels of a business to ensure everyone feels valued in the conversation surrounding workplace safety and no hazard goes un reported. Additionally, having the right safety structures and knowing your emergency procedures inside and out is crucial for swift action during unexpected situations, so take the time to familiarize yourself with them. A tidy worksite not only enhances efficiency but also minimizes risks, so commit to keeping your workspaces organized and clutter-free. Furthermore, taking regular breaks is vital for maintaining focus and mental well-being, allowing us to perform our best each day. Finally, looking out for your co-workers is not just a gesture of camaraderie – it helps create a supportive environment where everyone can thrive. After all, we all have loved ones waiting for us at home, and adhering to safety protocols ensures that everyone onsite can return safely to their families. Let's remember: safety is truly everyone's responsibility! Together, we can make a difference and cultivate a safer workplace for all. If you our need need any support, assistance or guidance with setting up, maintaining or educating your workplace in Regional Victoria, please reach out to the BeSafe team via info@besafevictoria.com.au
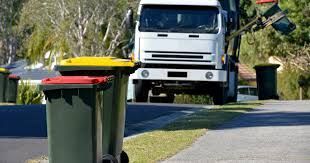
The regulator has declared that inspectors will commence visits to recognized workplaces in the sector starting this week, focusing on safety concerns related to loading and unloading, vehicle upkeep, and load securing. Sadly, since 2019, eight truck drivers and waste collectors involved in waste and recycling transportation have lost their lives, primarily due to vehicles rolling away or being involved in collisions. Among these heart-breaking incidents are two workers who were tragically crushed between their trucks and brick walls in separate occurrences: one in St Albans in July 2021 and the other in Melbourne's CBD in June 2023. Beyond these fatalities, over 400 truck drivers and garbage collectors in the waste and recycling industry have sustained serious injuries warranting workers compensation over the past five years. The most prevalent causes of injury include body stress, falls, being struck by moving objects, and incidents involving vehicles. WorkSafe Executive Director of Health and Safety Sam Jenkin said the transportation of waste carried unique risks that employers must take every reasonable step to control. "Workers in the waste transport sector often work in confined conditions with unpredictable loads that can become unstable, while improper maintenance can lead to damaged vehicles, skips, bins and lifting gear – putting workers and others at risk," Mr Jenkin said. The focus on waste management transport is part of a wider WorkSafe push to improve safety in the heavy vehicle transport industry, through strategic visits, compliance and enforcement, and industry partnerships. For More Information: https://www.worksafe.vic.gov.au/news/2024-10/inspections-put-spotlight-waste-transport-harm
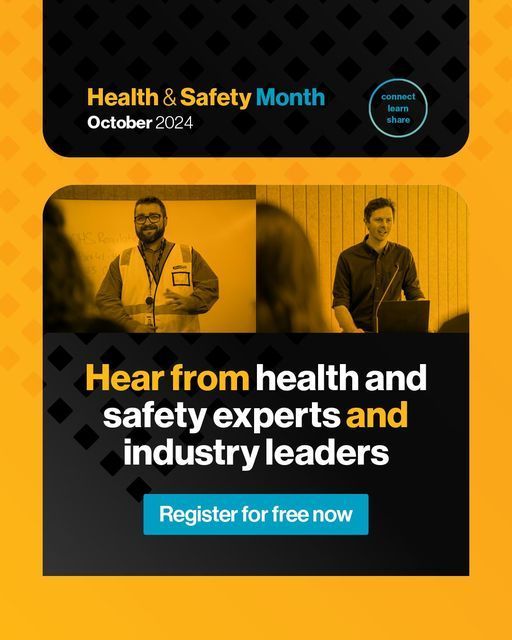
It's officially Health and Safety Month, making this the ideal moment to enhance your workplace safety! Gain new skills, knowledge, and tools to create a safer environment. Whether you’re an employer or an employee, WorkSafe has an event just for you. View all events and register today at worksafe.vic.gov.au/events