Falls from heights are still a leading cause of injury and death.
Falls are still a leading cause of injury and death, and they have been for a very long time. So why aren't we better at eliminating the risk of falls in the workplace?
Falls from heights can occur due to various hazards. These includes scaffolds, ladders, roofs, trucks, holes, pits, shafts, trenches, and mezzanines. in addition, we can at a risk of fall when working on machinery, on slippery or unstable surfaces, on sloping surfaces, or near an unprotected edge.
Don’t forget that falls risks can include a fall from an elevated position or a fall into a pit.
Even a fall from a relatively low height can cause very serious injuries, if not death.
As per the requirements of the Occupational Health and Safety Act 2004 - all fall related hazards must be controlled in the workplace. In addition, when there is the risk of a fall of 2 metres or more, then Part 3.3 of the OHS Regulations comes into play.
Employers must control the risk for falls:
1. You must ELIMINATE the risk if at all possible – by working on the ground or on a solid construction
If this can’t be done, then you could use the following control measures in order of priority:
2. Passive fall prevention device – guarding, railing or scaffolding
3. A work positioning system – so that workers are within a safe area
4. Fall arrest systems – safety harness, safety net or catch platform
5. Use of ladders, or administrative controls – safe work procedures and signage
In addition – you must establish emergency procedures, which includes how you will rescue a fallen worker and provide first aid.
Employers must also provide training and supervision of workers.
As always, you must review the controls that are put in place:
- if things change
- if the HSR requests it
- as part of your obligations to monitor health and safety
Don’t forget there is also a duty to consult with employees and HSR’s when identifying hazards and deciding what control measures to use.
For more information, take a look at: A guide to falls prevention | WorkSafe Victoria
As always, BeSafe is available for help and support HSR Training and support | BeSafe | Regional Victoria
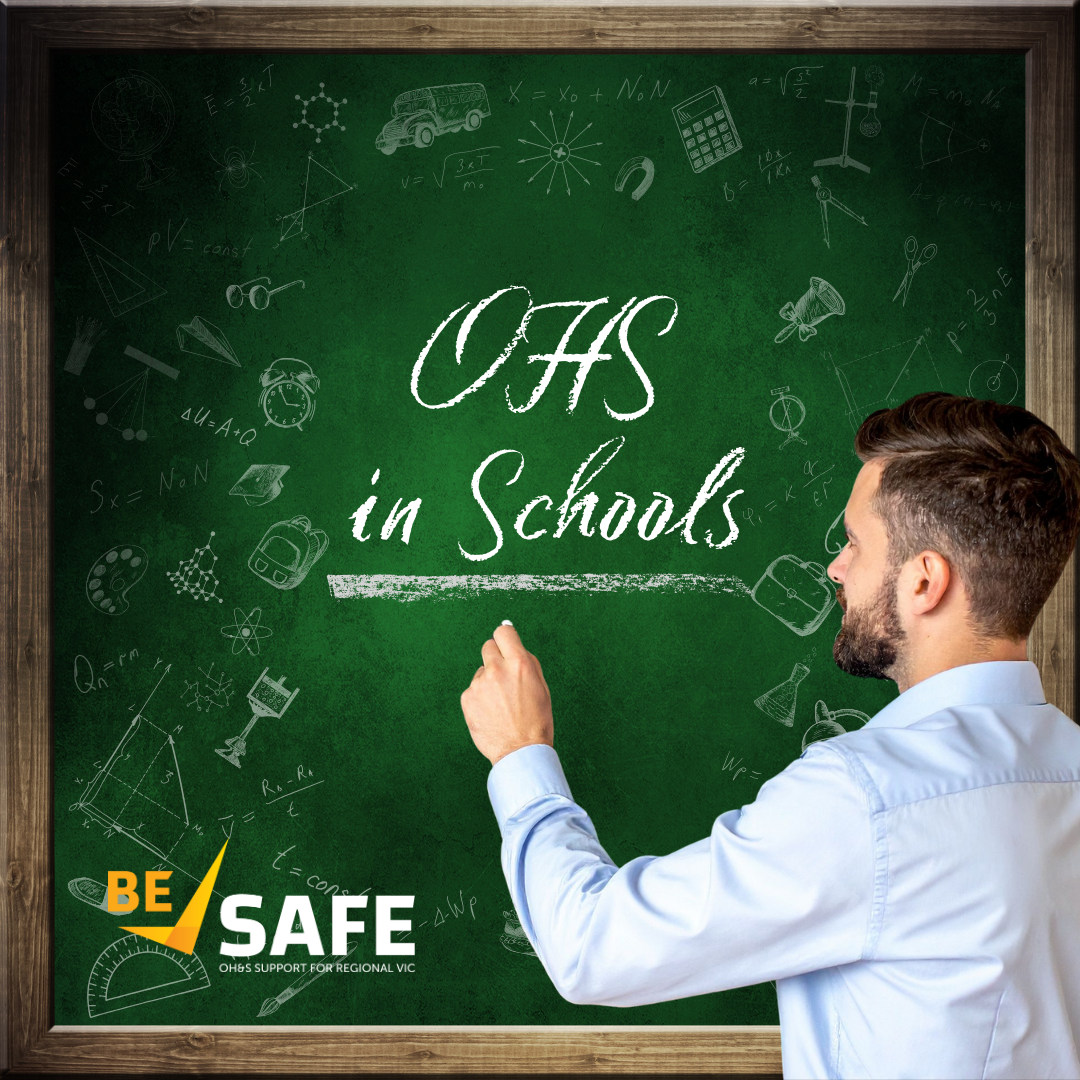
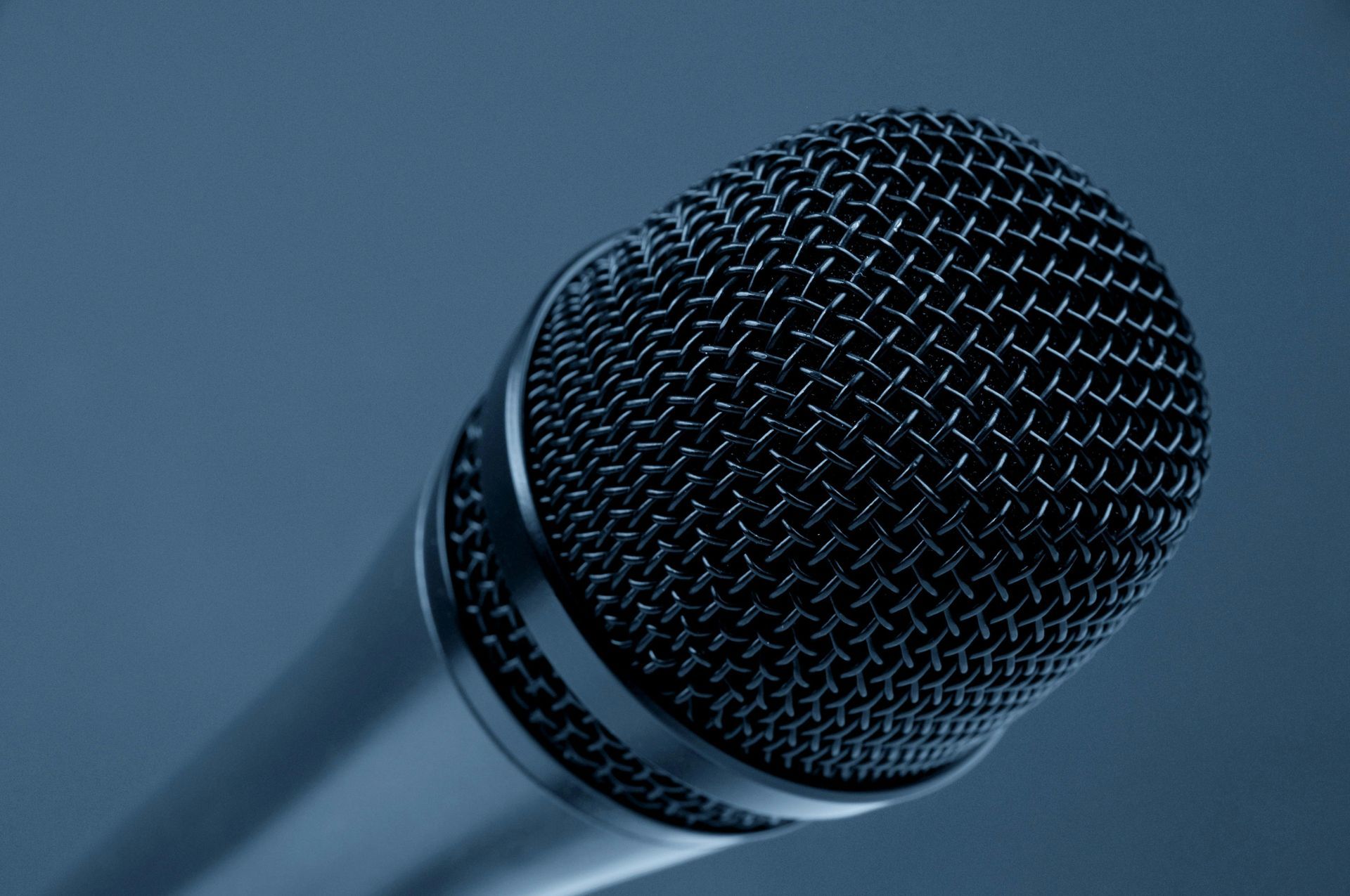