Risk Assessment Processes.
In any workplace, ensuring the safety and well-being of employees is paramount. One of the most effective ways to achieve this is through a comprehensive risk assessment process. This process helps identify potential hazards, evaluate the risks associated with them, and implement measures to control or eliminate these risks.
This is a continuous and ongoing process, as shown in the diagram above.
Step 1: Identify Hazards
The first step in the risk assessment process is to identify potential hazards in the workplace. Hazards can be anything that may cause harm, such as:
- Mechanical Hazards: Machinery, equipment or other items that could cause physical or impact harm.
- Chemical and Biological Hazards: Harmful substances or chemicals, including pathogens.
- Source of Energy: Such as electricity, heat, noise, light and radiation.
- Body Stressing or Impact Hazards: Activities which cause stress to the body. For example poor workstation design, repetitive movements, manual handling tasks and slip and trip hazards.
- Gravity: Activities where a person can fall or an object can fall on people.
- Psychosocial Hazards: Events, circumstances or systems of work which can lead to psychological illness, including stress, harassment, workplace violence and fatigue.
Step 2: Assess the Risks
Once hazards are identified, the next step is to assess the risks associated with each hazard. This involves evaluating the likelihood of the hazard causing harm and the severity of the potential consequences. Consider the following factors:
- Frequency of Exposure: How often employees are exposed to the hazard.
- Duration of Exposure: How long employees are exposed to the hazard.
- Severity of Potential Harm: The potential impact on health and safety.
It can be useful to use the Likelihood Consequence Table to help with assessing the risks (see below).
Step 2: Implement Control Measures
After assessing the risks, it’s crucial to implement control measures to mitigate or eliminate the risks. Control measures can be categorized into:
- Elimination: Removing the hazard entirely from the workplace.
- Substitution: Replacing the hazard with a less dangerous one.
- Engineering Controls: Isolating people from the hazard through physical changes to the workplace.
- Administrative Controls: Changing work procedures or policies to reduce exposure to the hazard.
- Personal Protective Equipment (PPE): Providing employees with protective gear to minimize exposure.
It can be useful to use the Hierarchy of Control diagram to help you during this process (see below).
Remember that you must always use the highest possible level of control possible.
Step 4: Monitor and Review
Risk assessment is not a one-time activity. It’s essential to continuously monitor and review the effectiveness of the control measures. Regularly update the risk assessment to reflect any changes in the workplace, such as new equipment, processes, or personnel. Encourage employees to report new hazards and participate in the risk assessment process.
It is also important to make sure that your new control measure have not inadvertently introduced a new risk or hazard into your work environment.
Documentation
Documenting the risk assessment process is crucial for accountability and compliance. Keep detailed records of identified hazards, risk assessments, and implemented control measures. Communicate the findings and safety measures to all employees to ensure they are aware of the risks and how to protect themselves.
Consultation
Don't forget that at every stage of the risk assessment process, you must consult with the workforce. This is a legal obligation, but it is also extremely useful to the employer, as the workers who are doing the job are in the best position to identify risks and hazards in their own work environment and to find ways to control them too.
By following these steps and principles - organisations can create a safer work environment, reduce the likelihood of incidents and injuries, and promote a culture of safety. Remember, a proactive approach to risk assessment not only protects employees but also enhances productivity and morale.
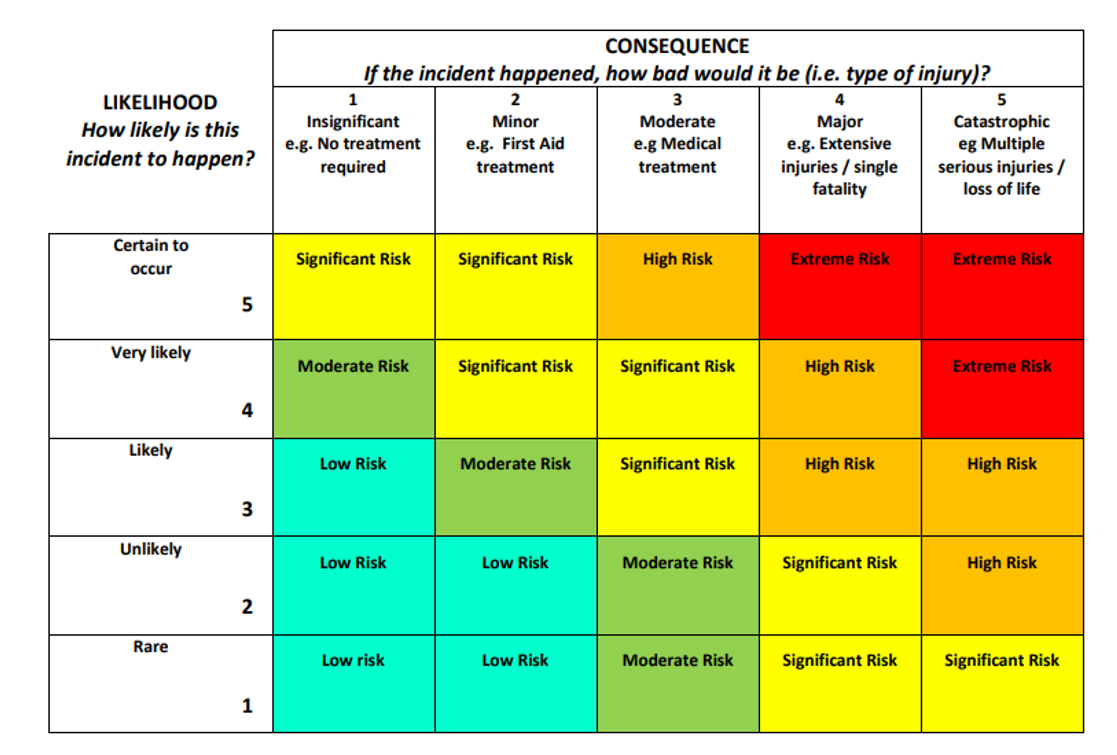
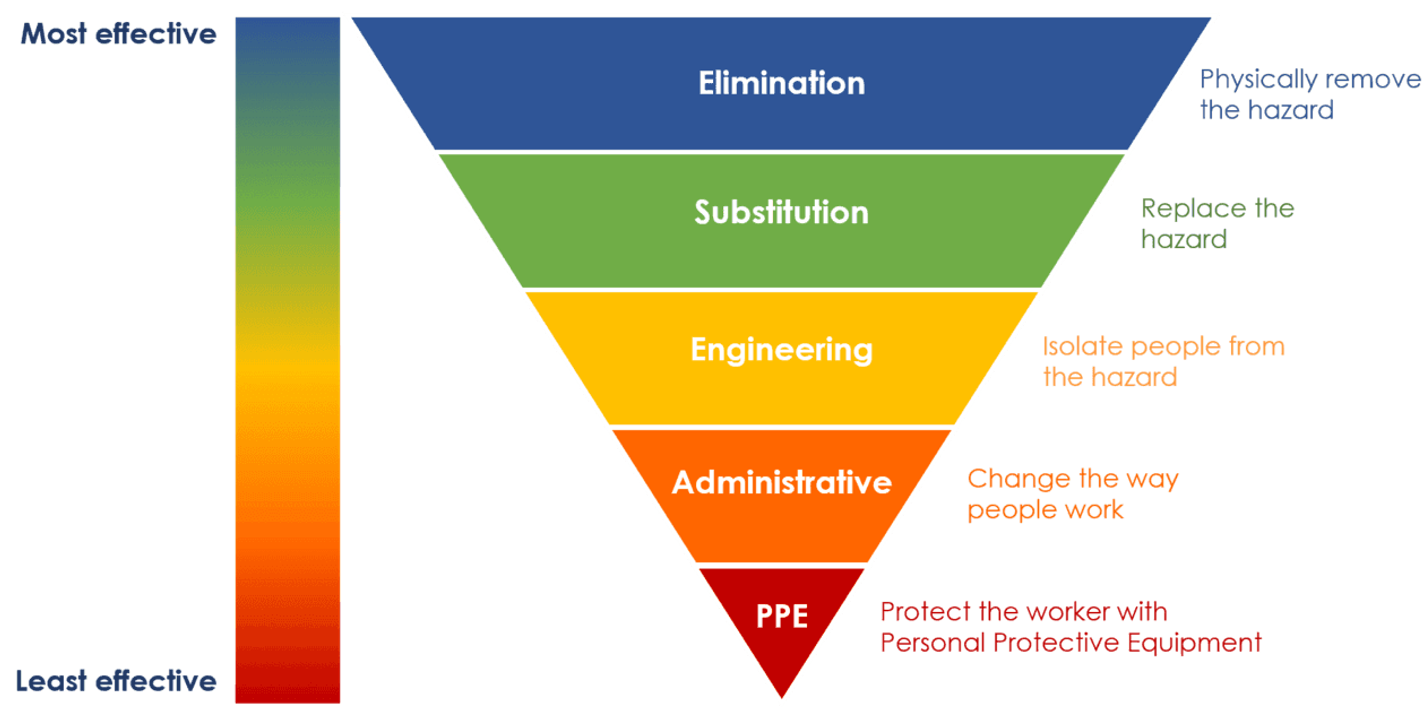
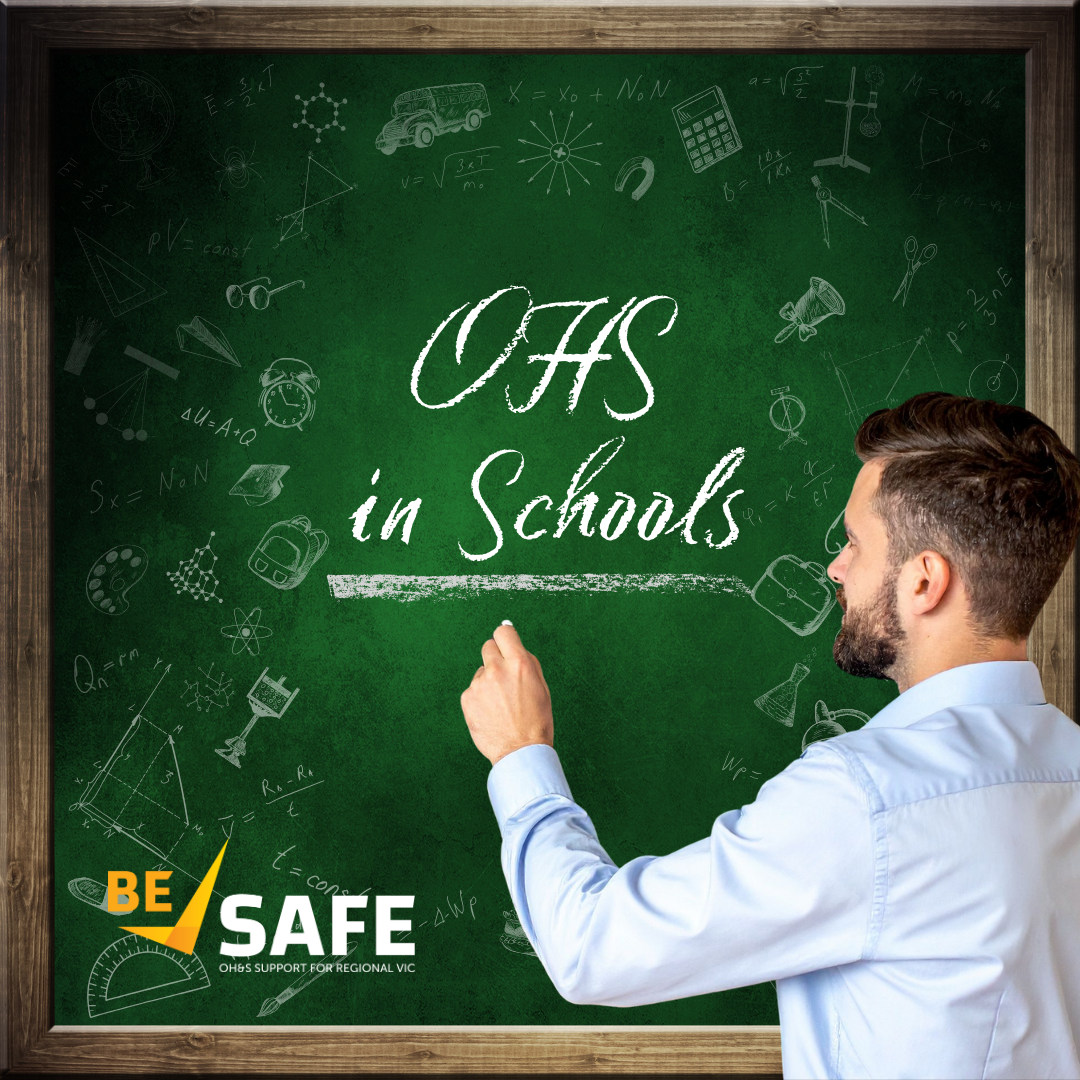
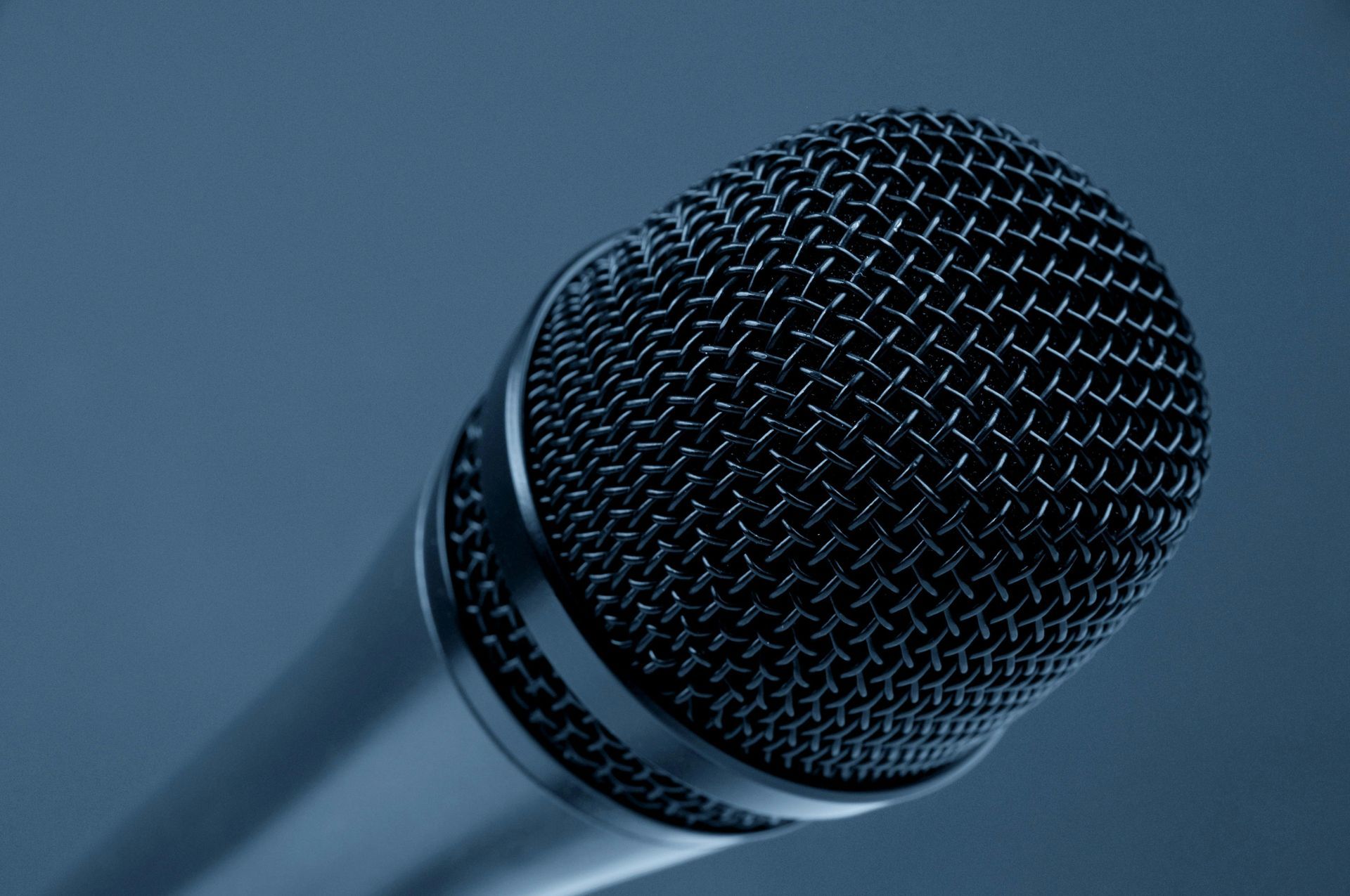