Plumber Fined
The director, 31, was sentenced in the Mansfield Magistrates' Court on Wednesday 2 October after pleading guilty to a single charge of failing to ensure that a workplace under their management or control was safe and without risks to health.
He was fined without conviction and also ordered to pay costs of $4,249.
In February 2022, the director and his 19-year-old apprentice had completed the installation of a hot water service at a property in Bridge Creek when it was decided that the client would join them on the return trip to Mansfield. The court heard that since the director's work ute had only two seats, there was a conversation about the apprentice being transported in the toolbox mounted on the rear tray. During the estimated 20-25 minute drive, the apprentice recorded a video expressing his discomfort and the heat he experienced in that cramped space. Upon reaching Mansfield, the apprentice's brother observed him being released from the toolbox, his face red and hunched over, while the director and client stood nearby, laughing and enjoying beers.
The incident was reported several months later, after the apprentice confided in his mother, who then notified his support officer at Apprenticeships Victoria.
WorkSafe's investigation revealed that certain tools had been left in the toolbox alongside the apprentice, posing a risk of severe injury or fatality should the ute be involved in an accident or come to an abrupt halt.
It was reasonably practicable for the director to reduce the risk by not driving the ute, or not allowing it to be driven, when a person was in the toolbox.
WorkSafe Executive Director Health and Safety Sam Jenkin said there was no excuse for putting a young apprentice in such a vulnerable position.
"Illegally transporting this young apprentice in the back of a toolbox was extremely unsafe and could have had absolutely catastrophic consequences," Mr Jenkin said.
"WorkSafe will continue to hold employers accountable when they fail to prioritise safety and wellbeing, particularly for young workers who won’t always have the confidence to speak up if something is wrong."
For more information: https://www.worksafe.vic.gov.au/news/2024-10/plumber-fined-after-driving-ute-teen-toolbox
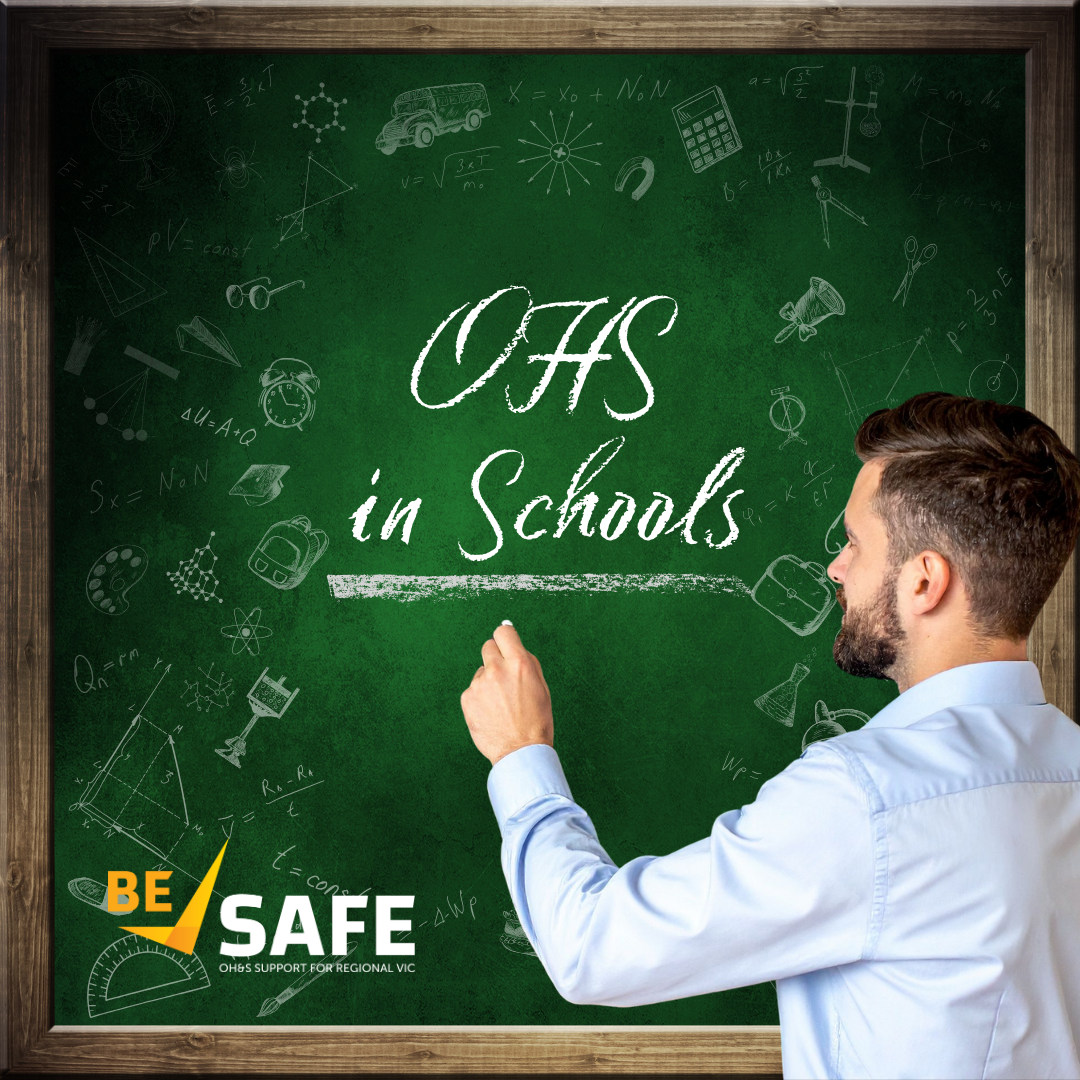
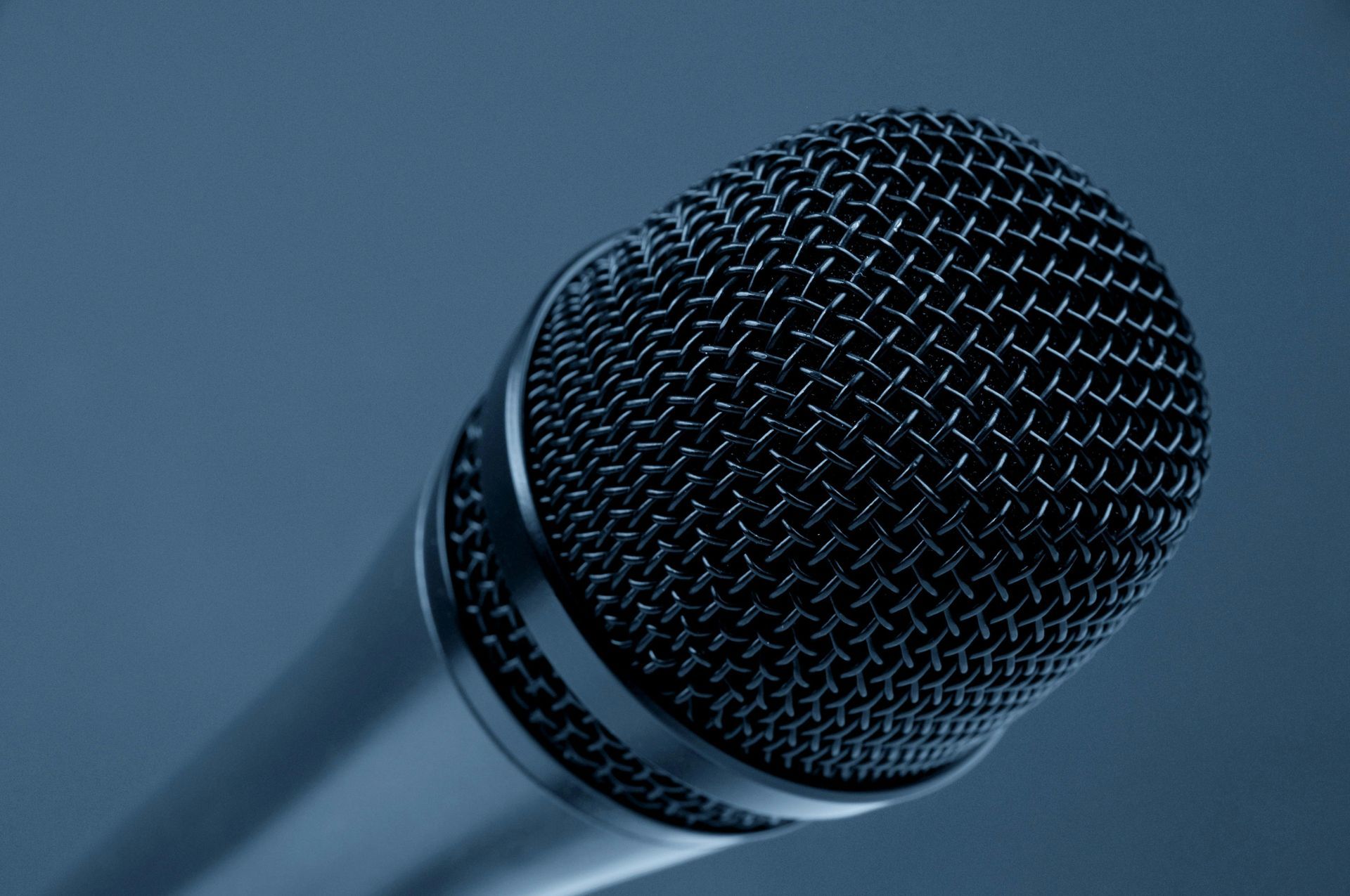